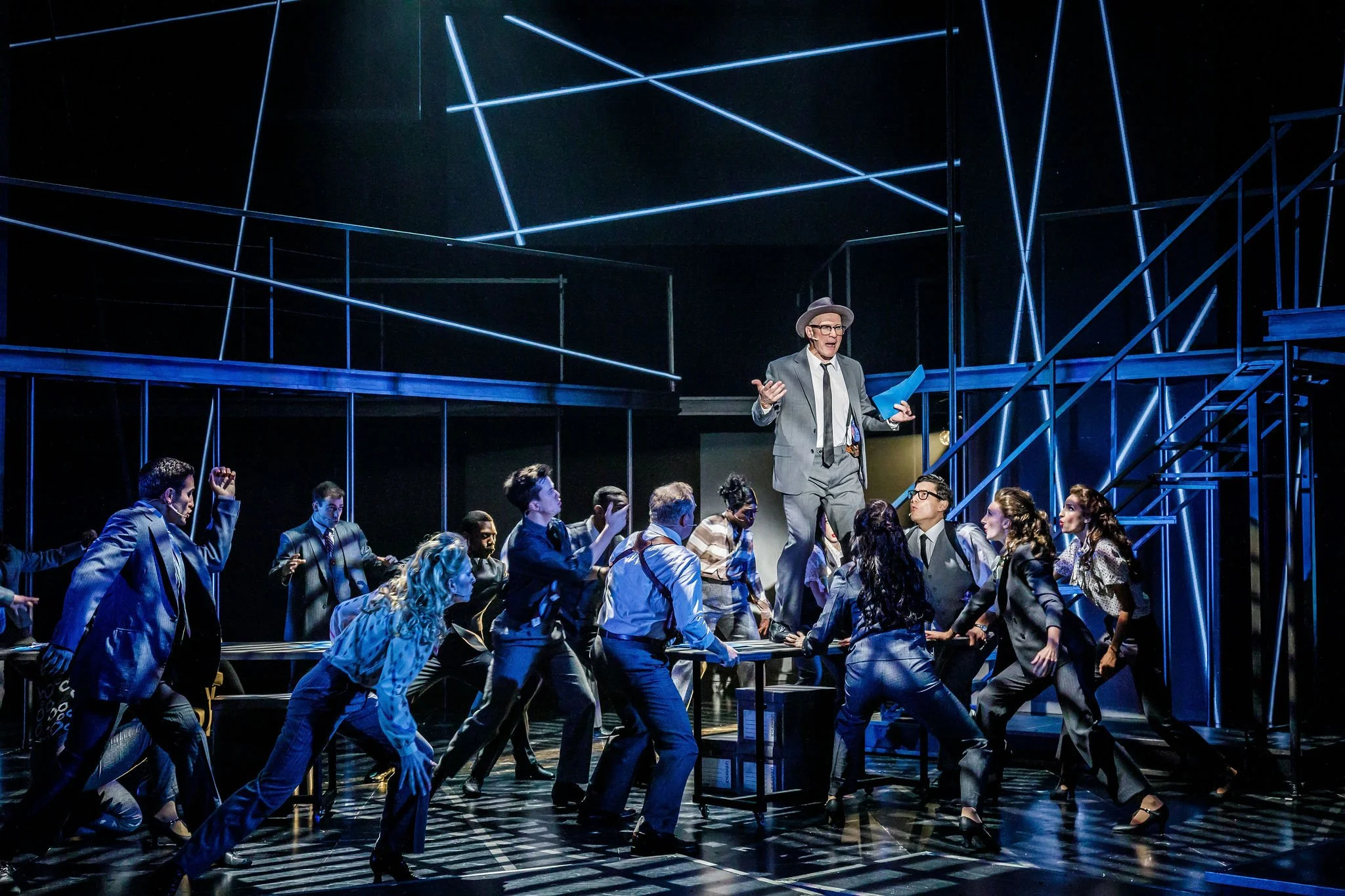
CATCH ME IF YOU CAN
The Rev Theatre Company
Directed by Brett Smock
Scenic Design:
Adam Koch
Video Design:
Steven Royal
Lighting Design:
Jose Santiago
Sound Design:
Kevin Heard
Costume Design:
Tiffany Howard
Wig Design:
Alfonso Annotto
Summer 2022, Assistant Technical Director
I spent the summer 2022 as the ATD of The REV Theatre Company. This was special to me, as I completed my first professional contract at this same company as a carpentry intern in 2019. The Technical Director, Rocky Love, allowed me to focus on improving the skills I was interested in, and as such put all of my efforts into my drafting and engineering. I had only become familiar with AutoCAD a couple months prior, so I grew a lot that season.
Catch Me If You Can is a musical following a world famous scam artist. There are many locations all over the world so we had to create a dynamic set that could transform easily. This was my first professional drafting job so there was a lot to still learn, and through these shows I began to refine my personal drafting style. I spent most of time time in the office during this production, so this page will focus exclusively on my draftings.
The first project I worked on was the SL half of the upper platform level. It was standard 2x4 construction and legged using 1-1/2” Sch 40 pipes connected using “Leg-O-Matic” brand brackets. This was a relatively simple unit, and was really a great opportunity to help integrate me into the company and workflow. As time went on at the company I greatly simplified my drafts to better suit the needs of our team. You can download the PDF version of the package using the button below.

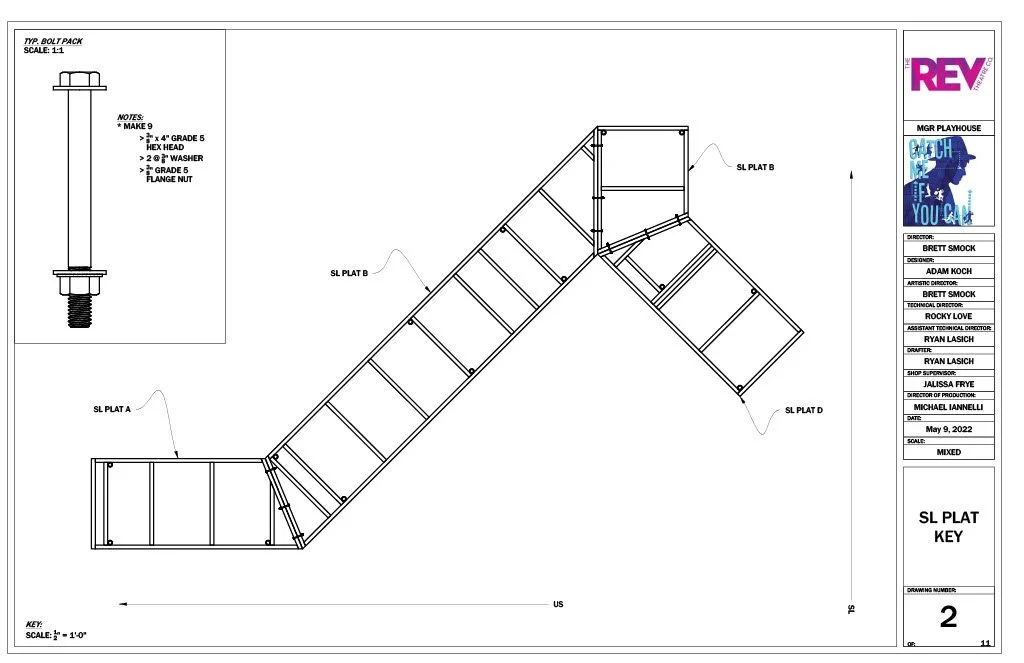
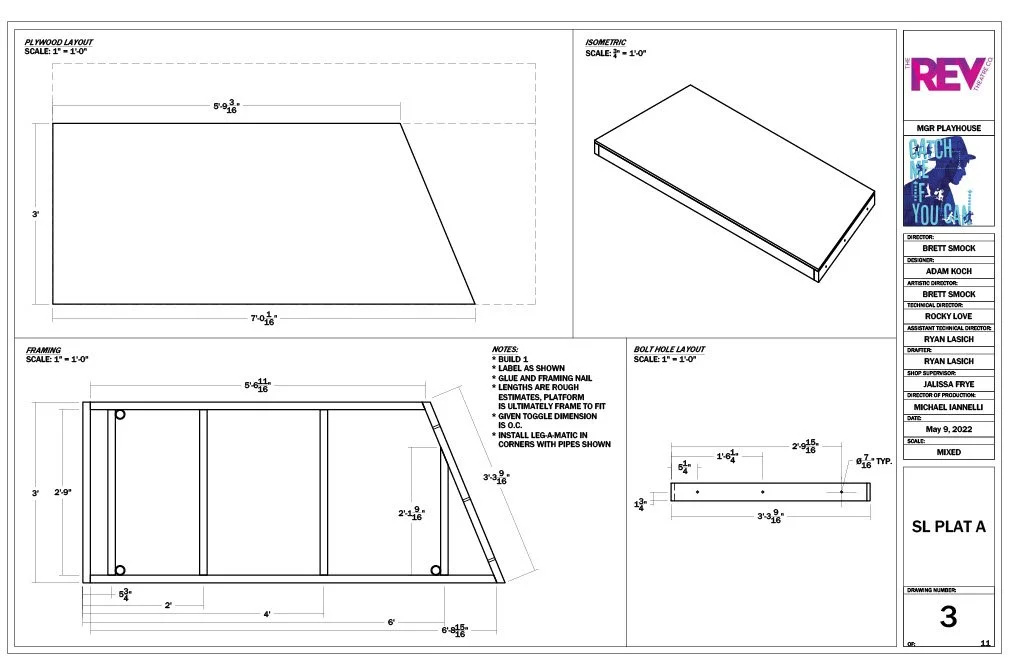

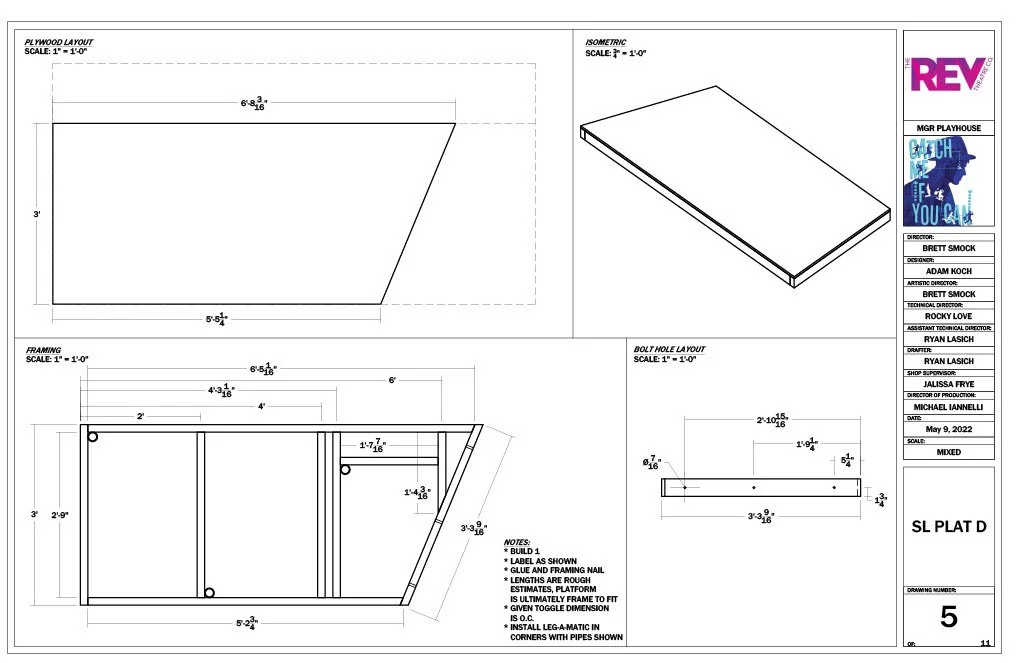

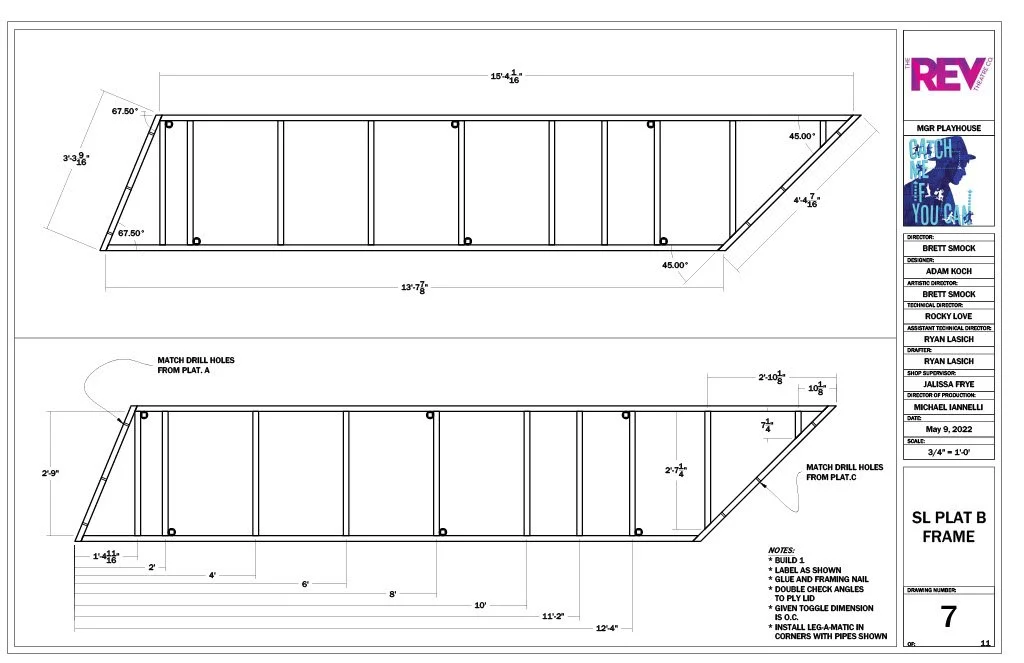
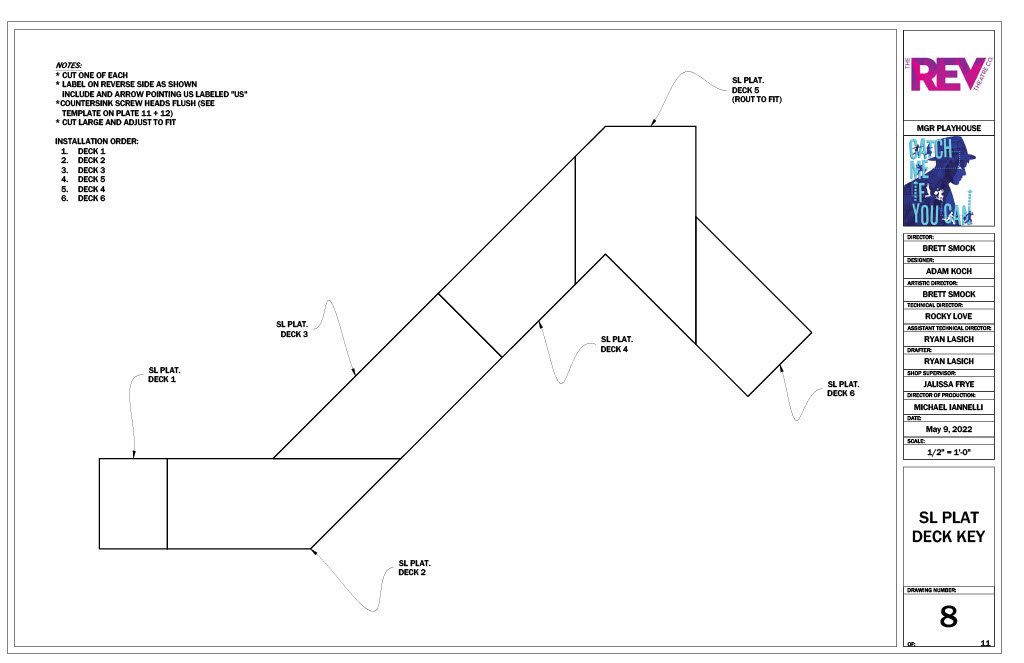
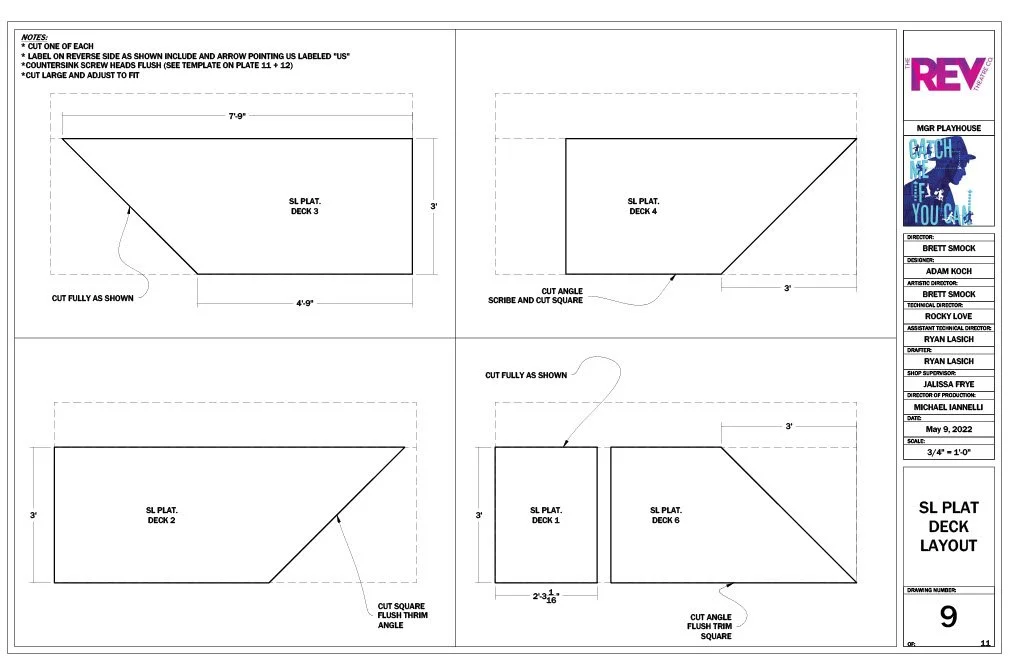
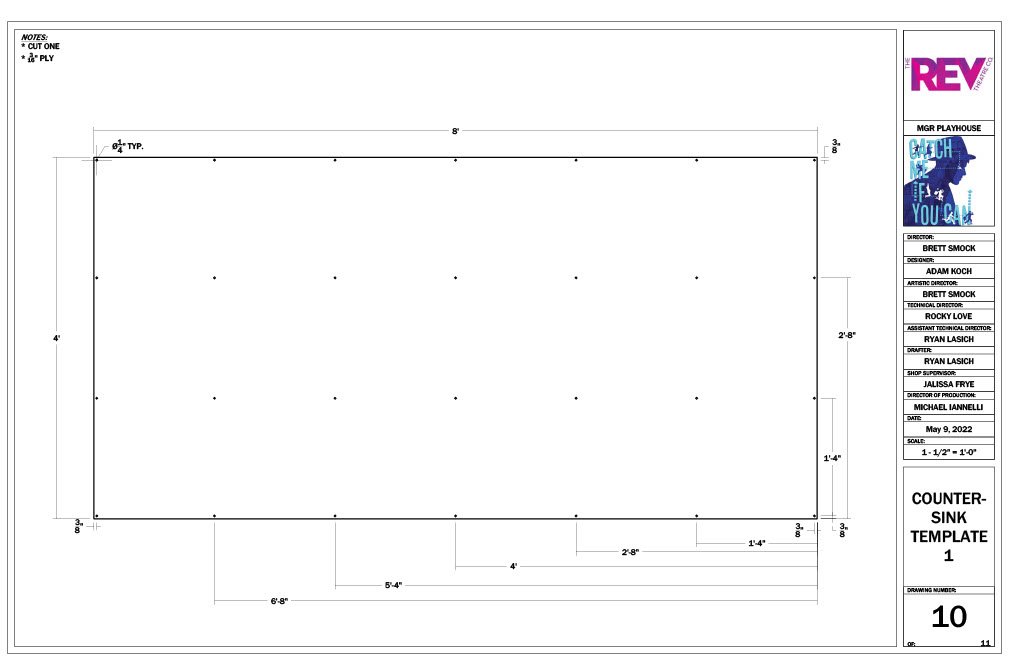
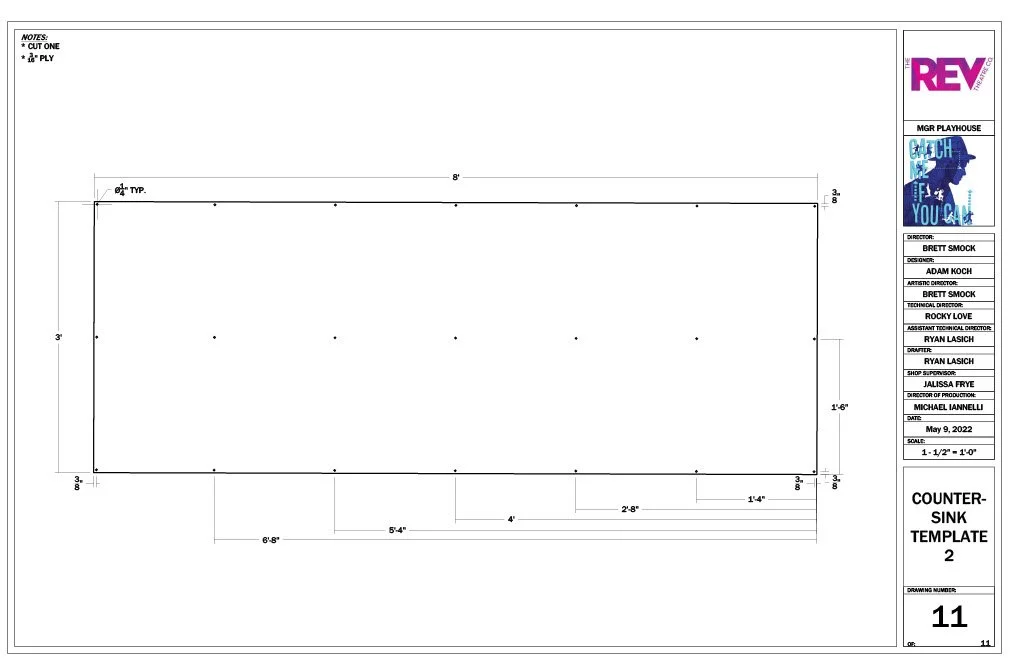
Next I drafted all of the handrails for the upper platform. These were also straight forward in design, 1”x1” steel box tube with 1/4” plate steel based spindles and 1-1/2”x1-1/2” top rails. These had to hug the angles of the platforms, leading to some interesting welding connections. There were also several spindles made to create an aircraft cable handrail on the upstage sides of the platforms.
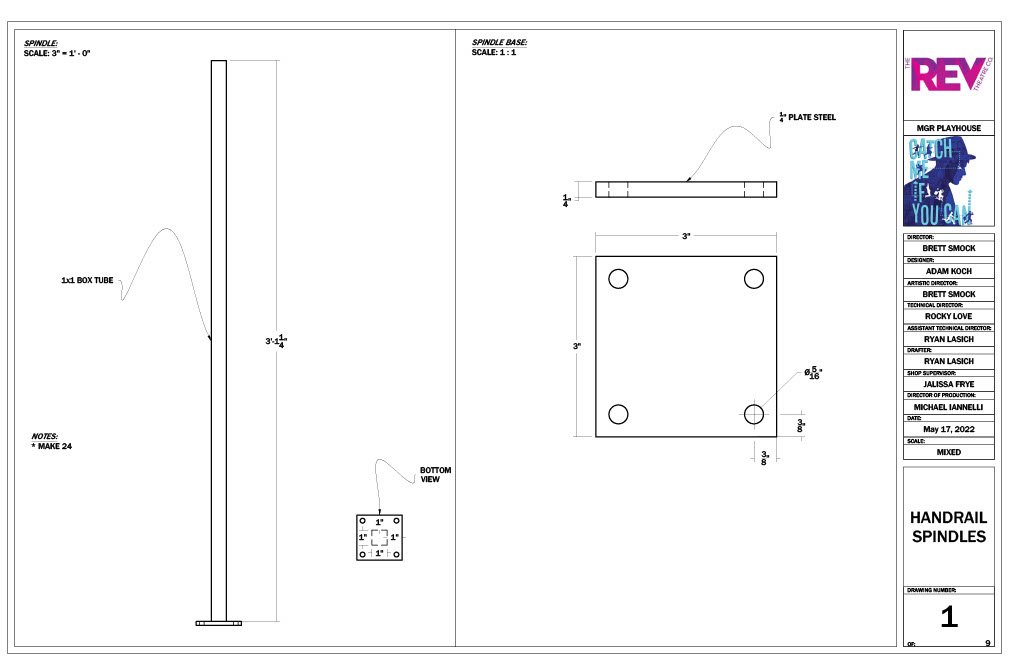
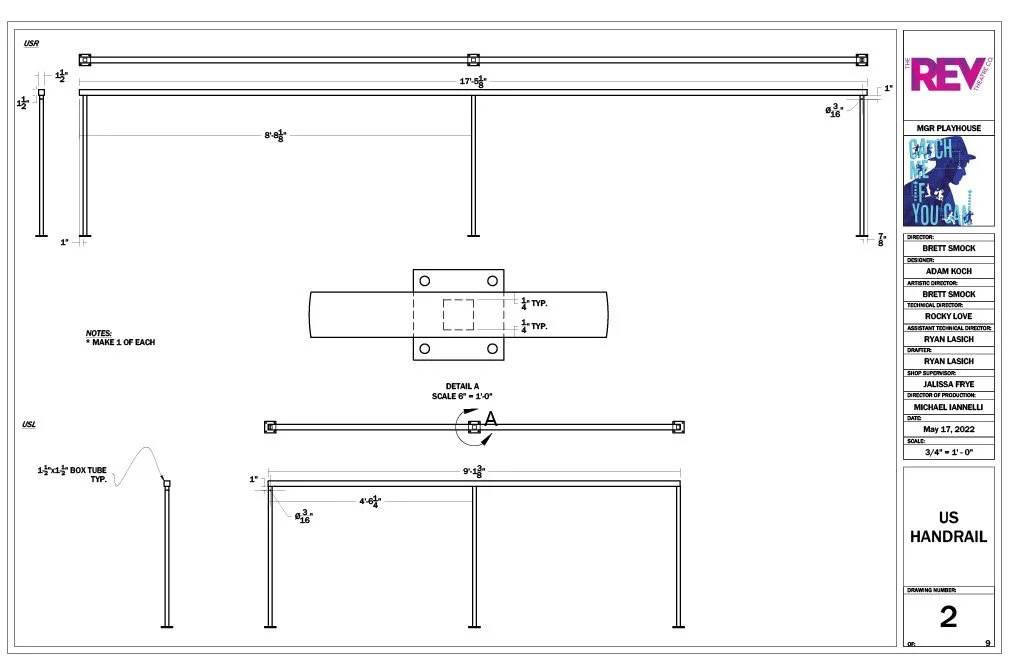
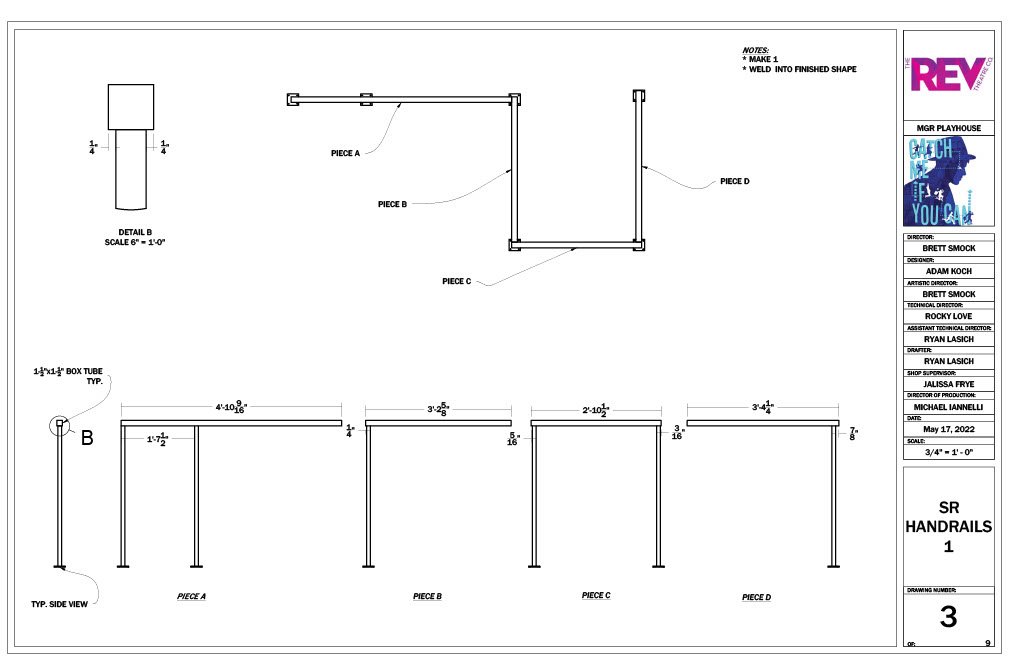
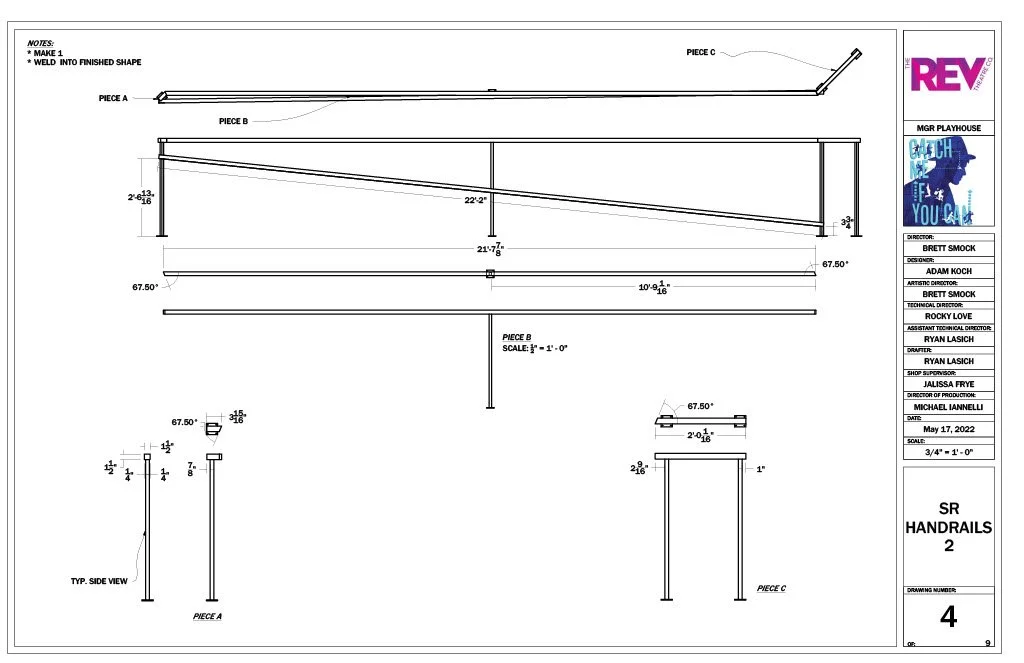
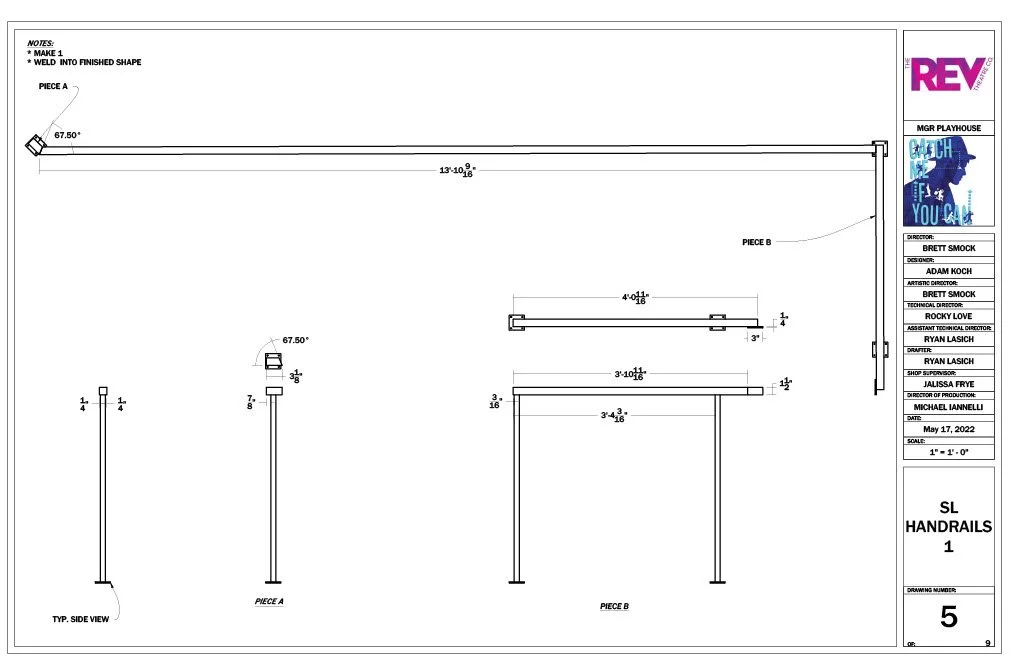
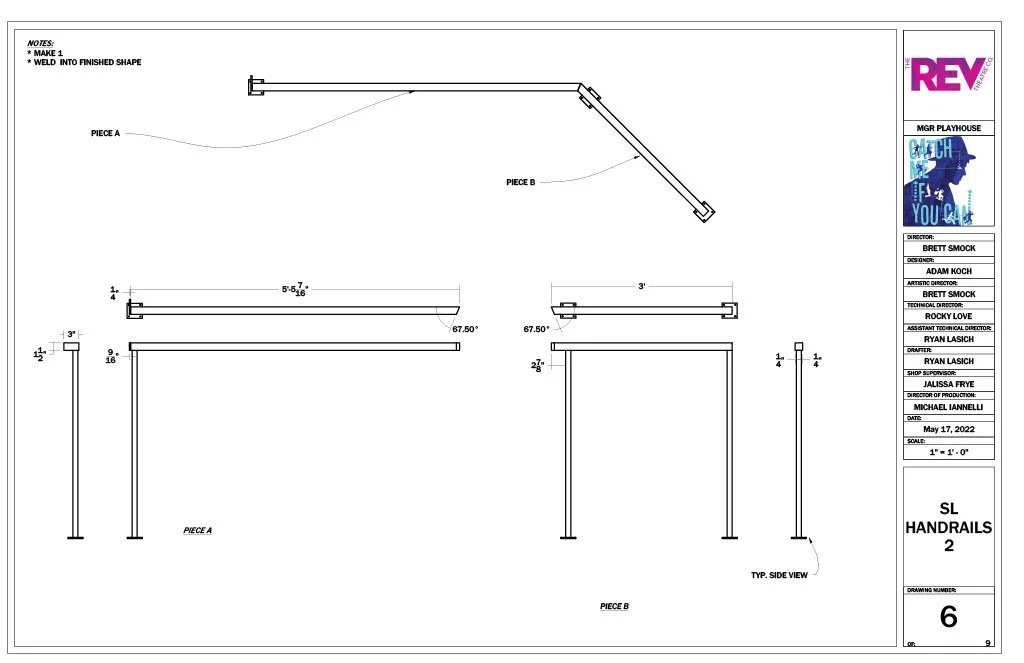
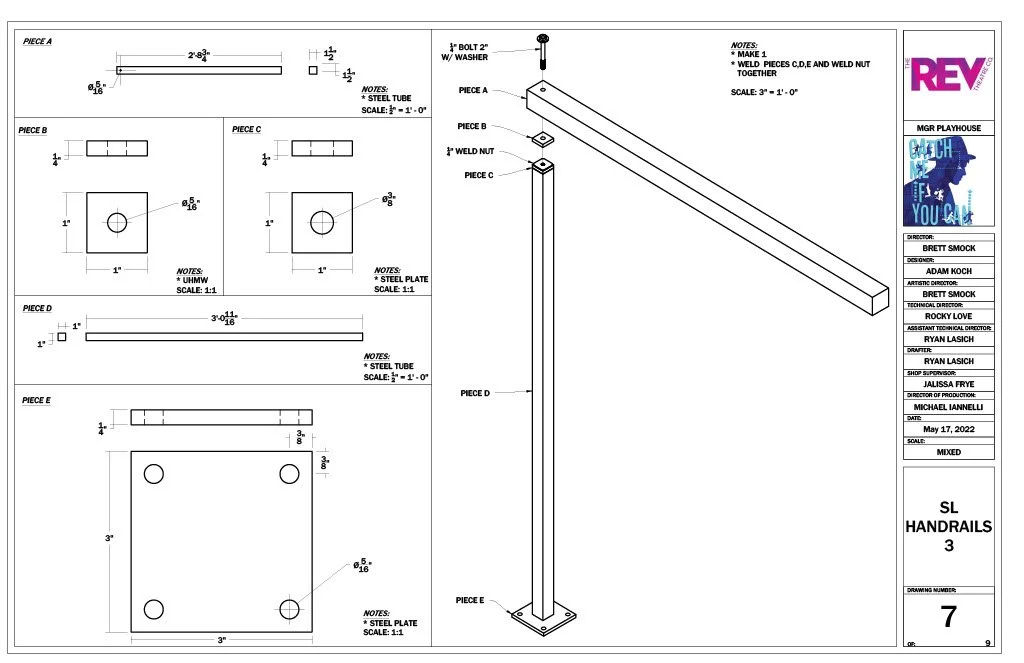
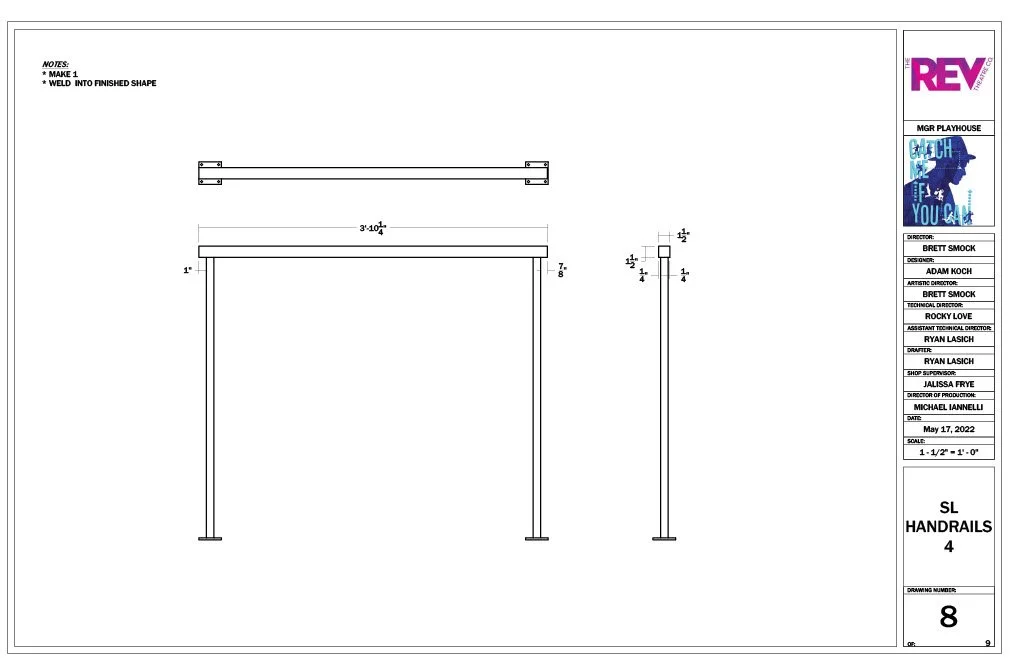
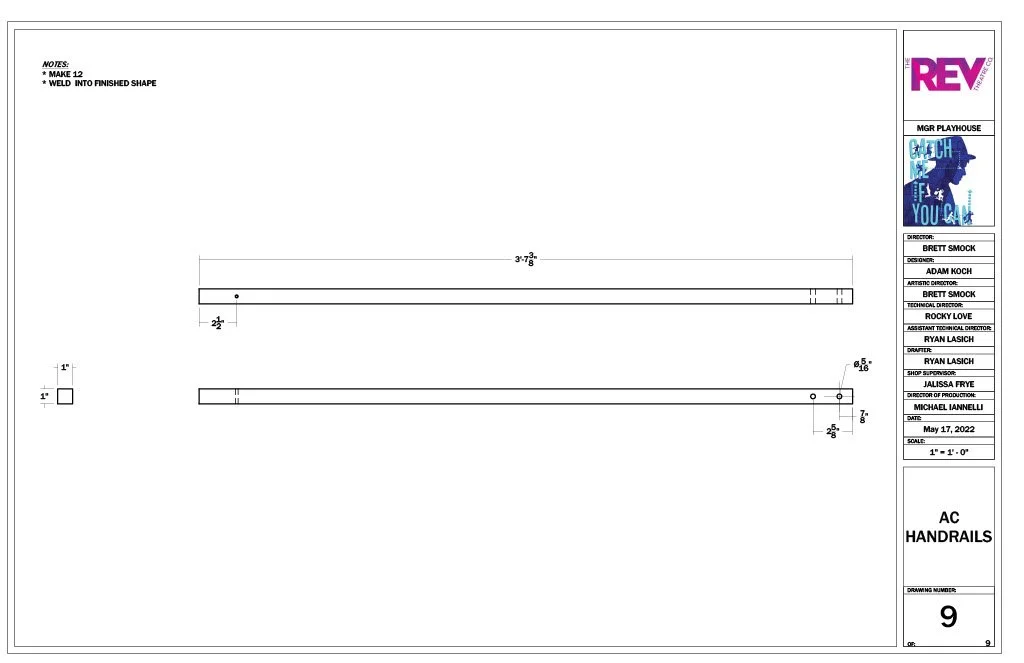
Next was the collection of platforms on the apron. These were mostly stock platforms with some new builds to get the desired size. We also opted to apply facing in space, so we made some stock strips in advance.
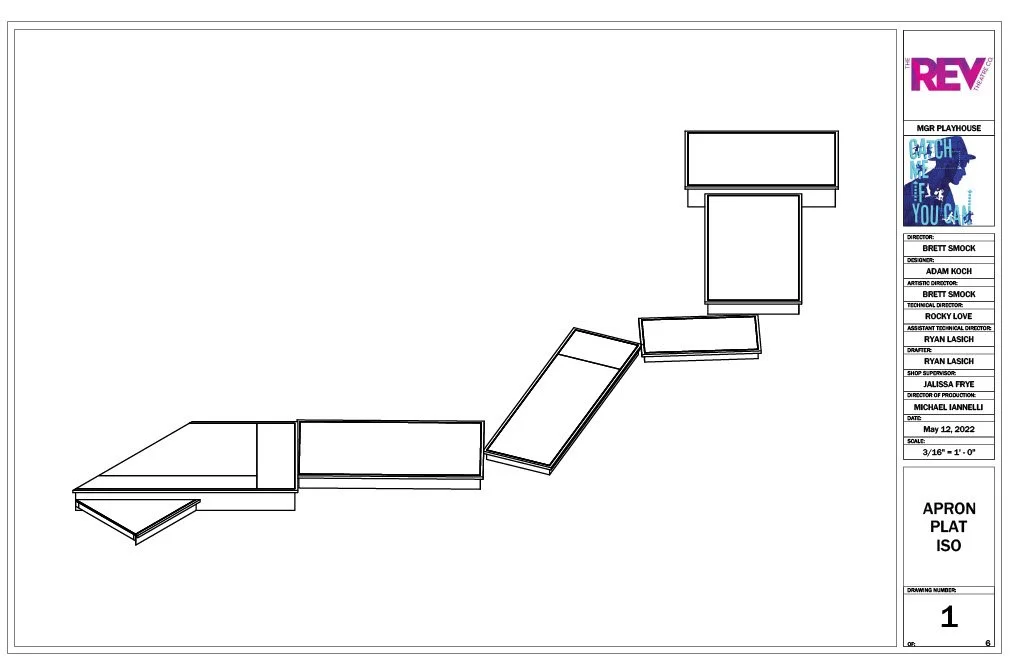

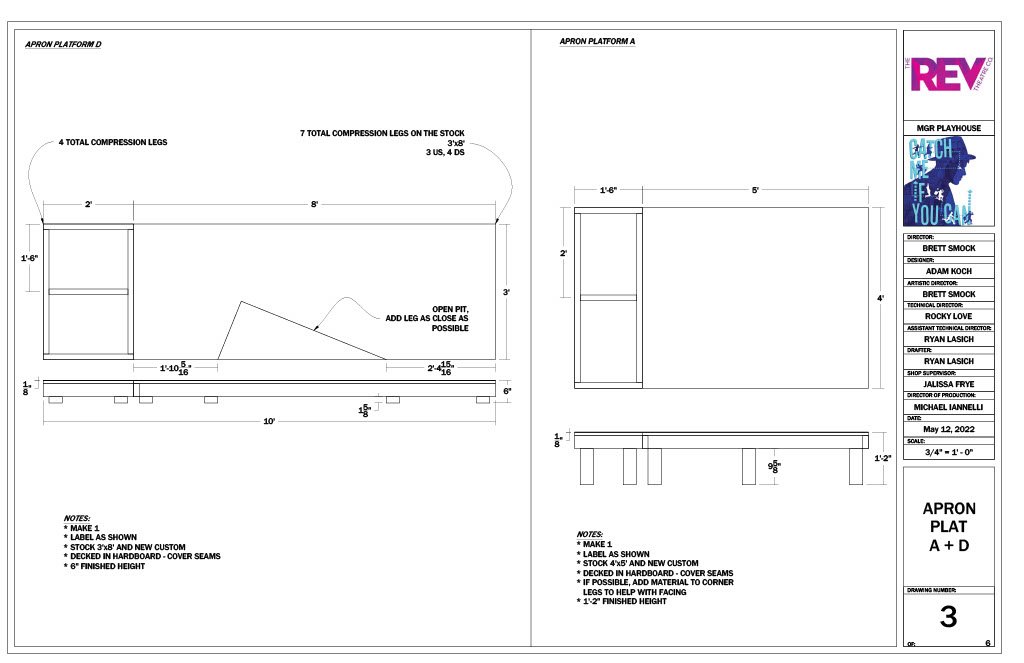
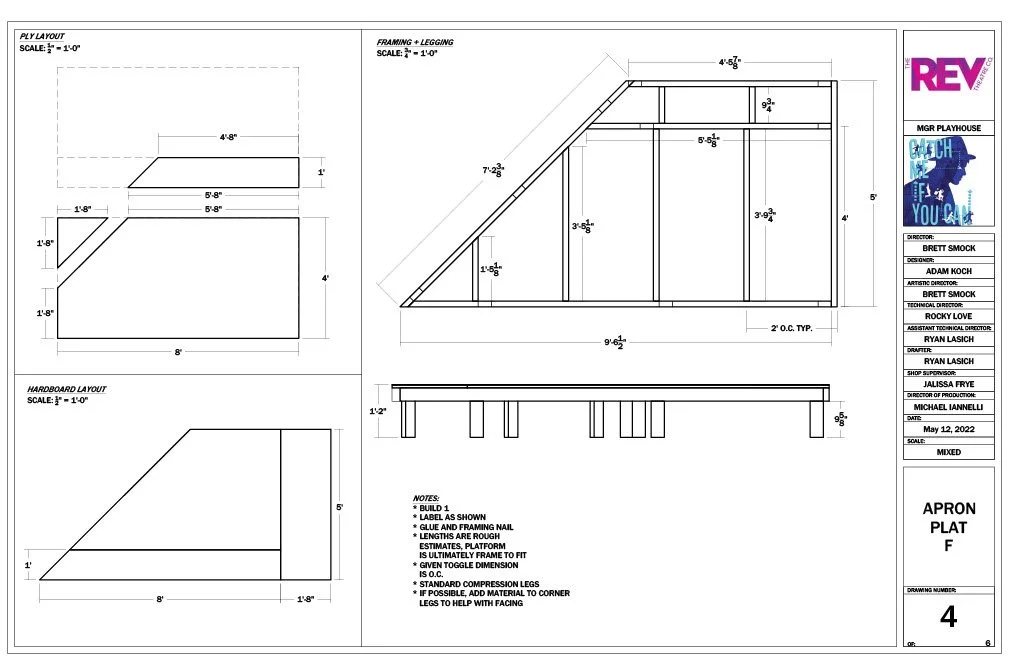
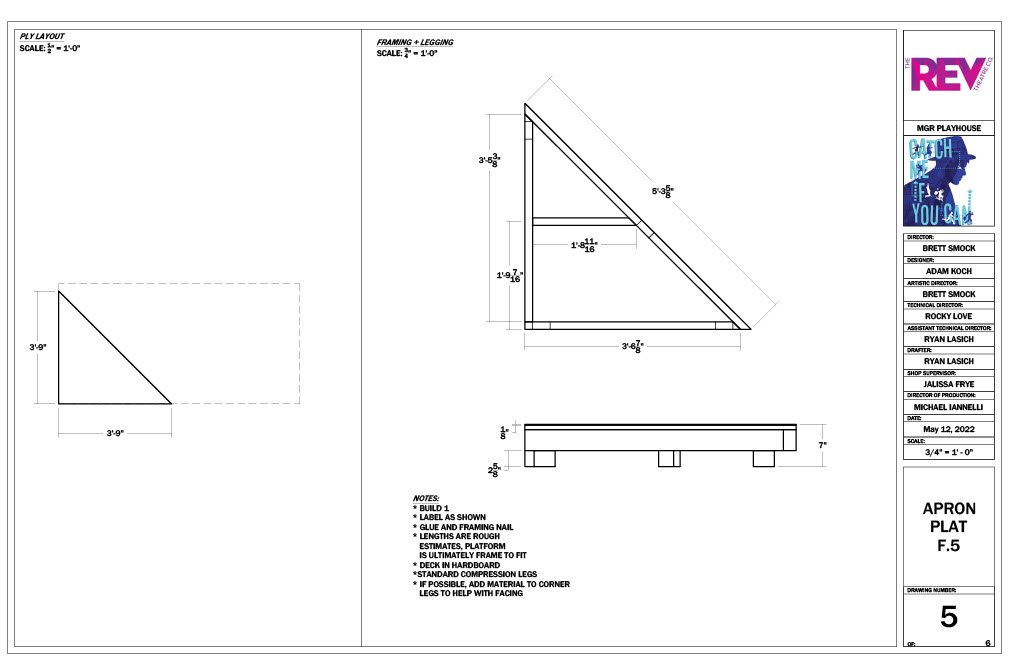
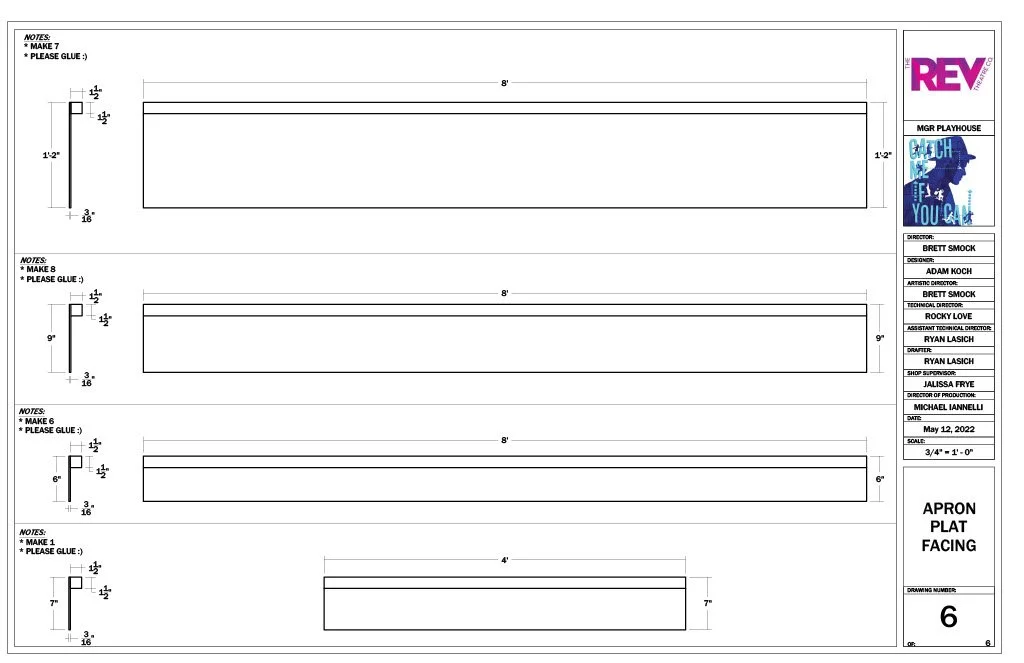
By far the most complex units for the show were the large LED boxes. These were large open frames with steel details bolted to the front. Certain parts of the steel had LED neon strips added to them. To help achieve this, we made several “trough” pieces by plunge routing a straight line through some 1x lumber. These were challenging not only to build, with our limited space, but also to transport over to the theatre. As such, the large US box with its long steel arm was finished in space.
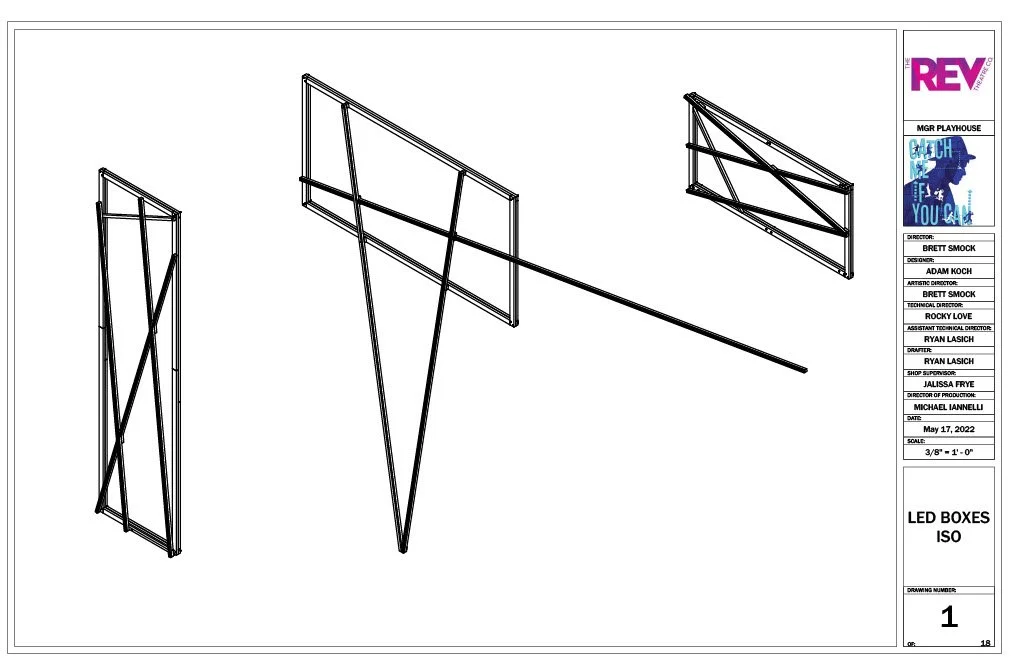
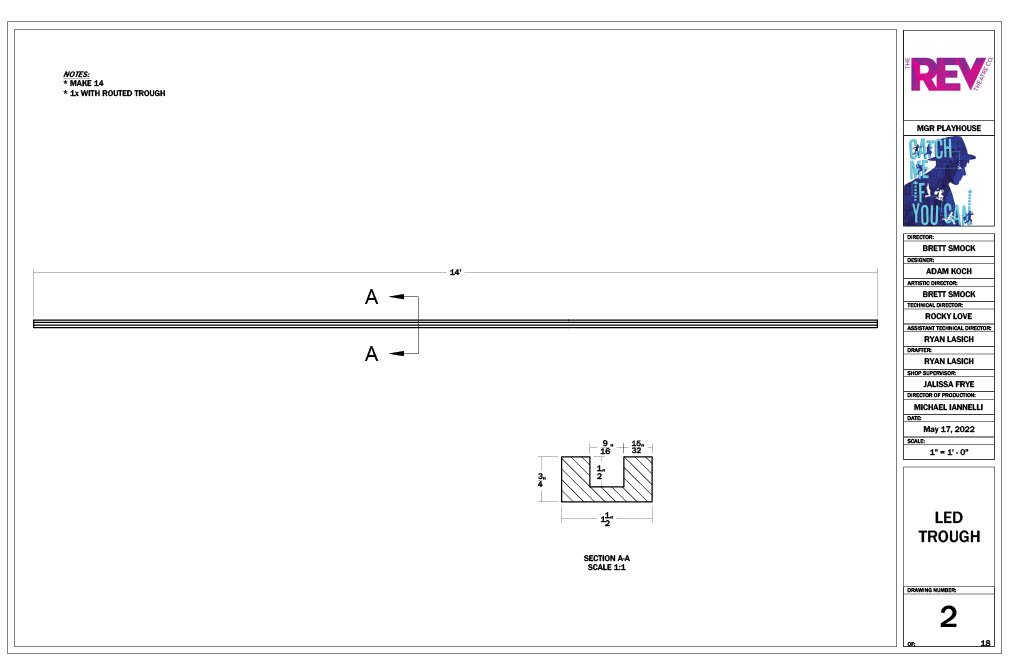
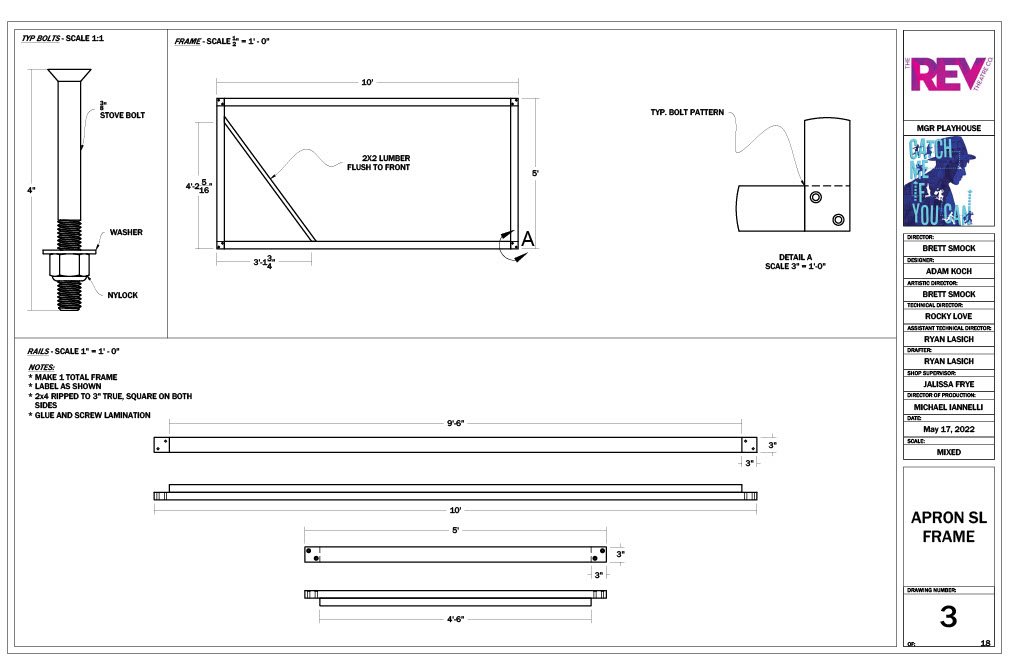
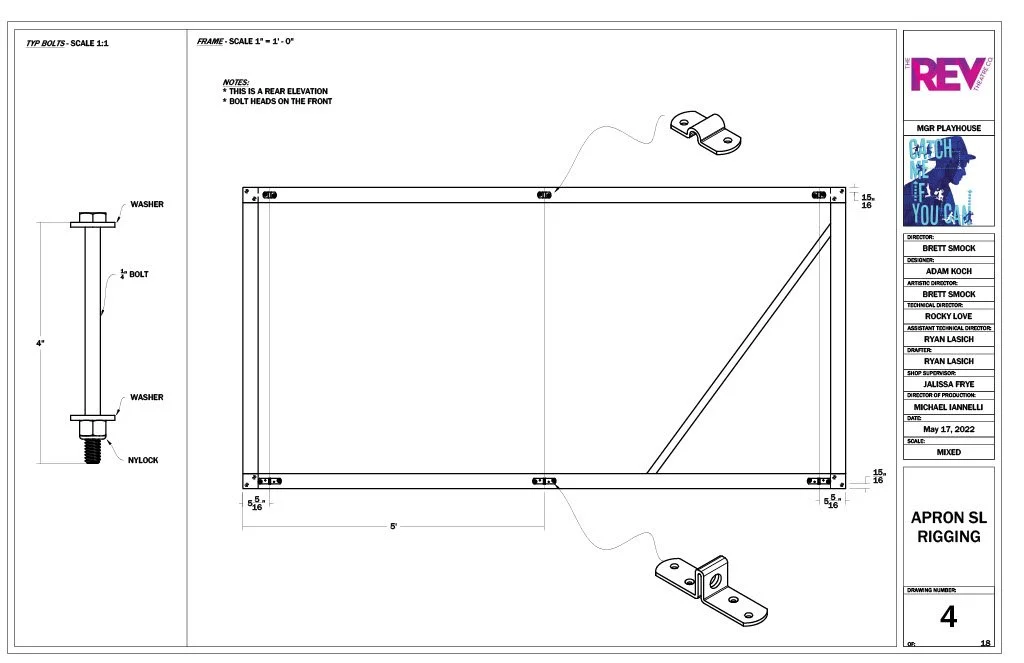

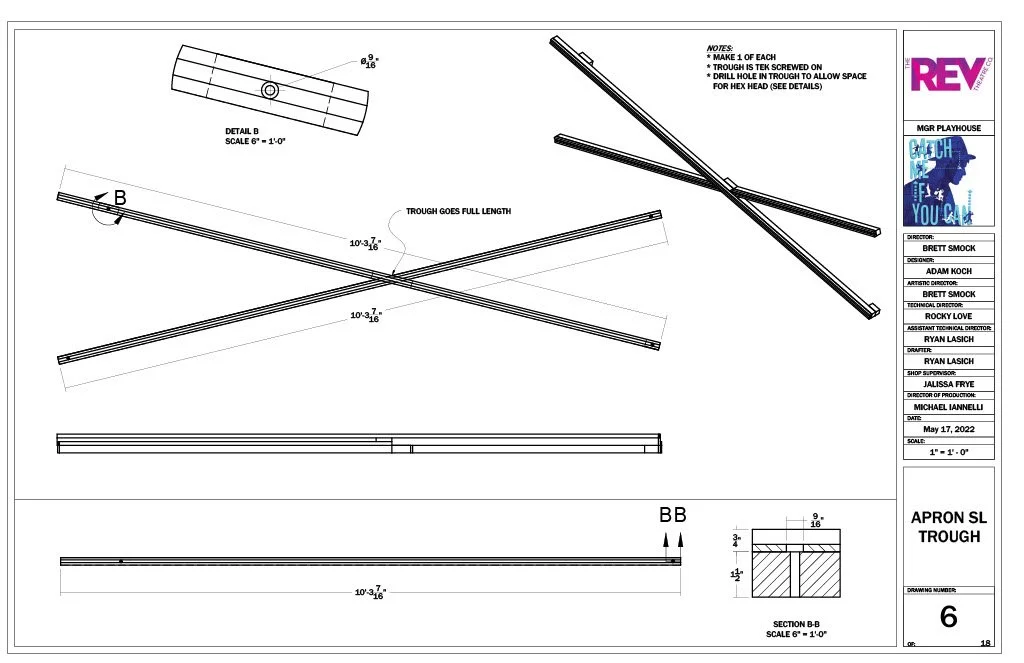

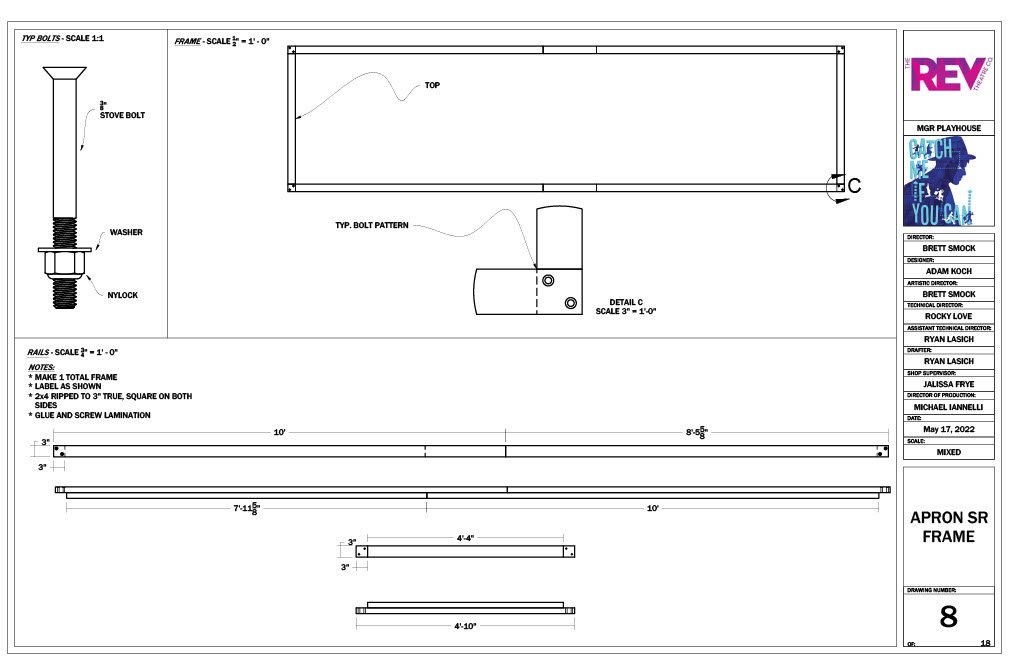
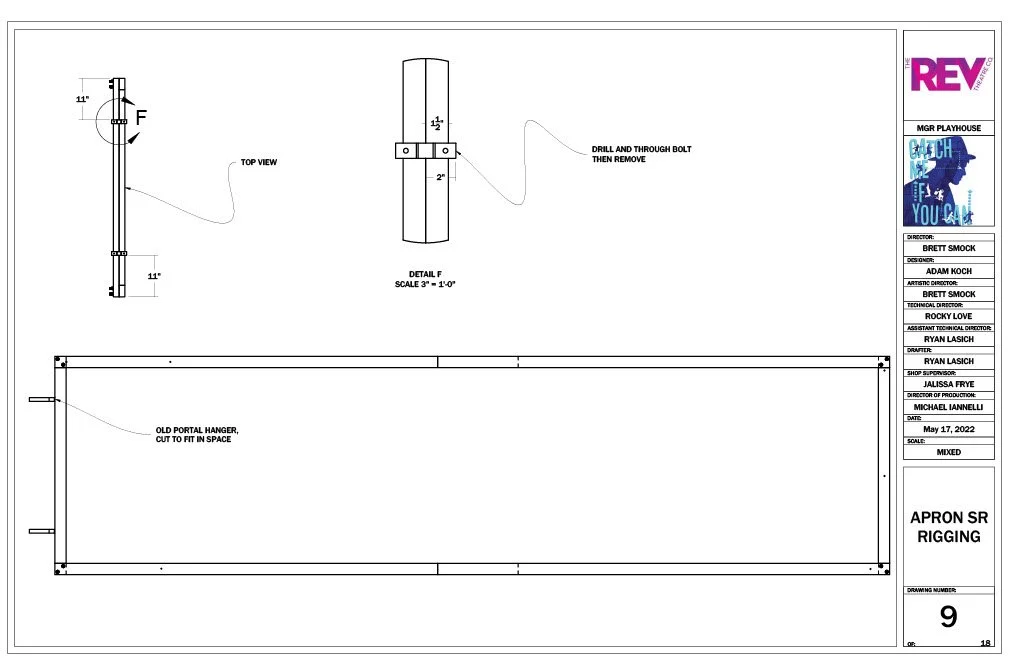
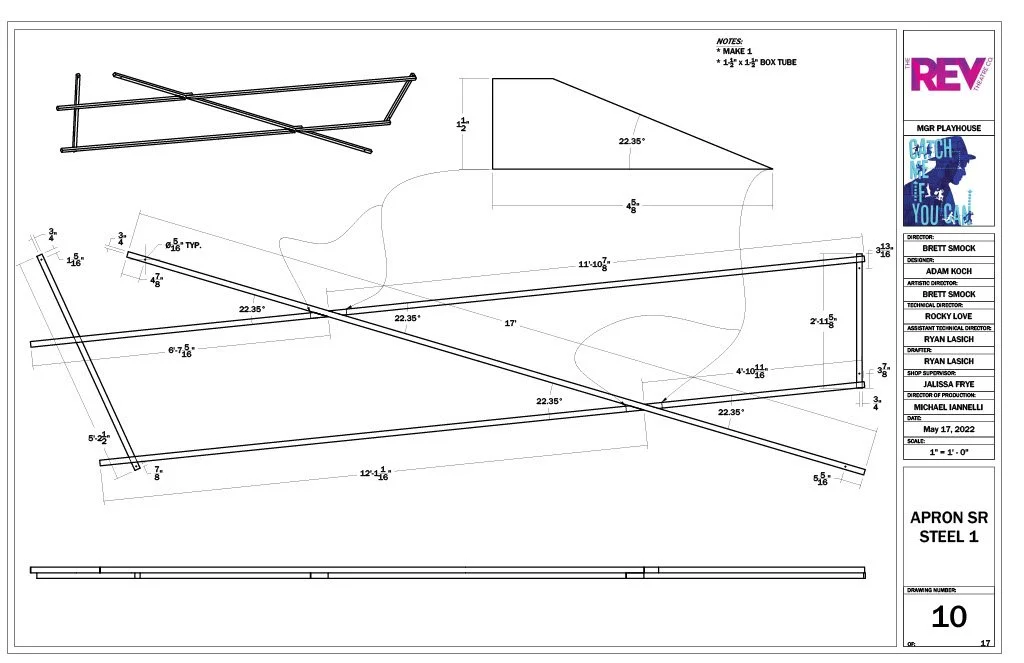
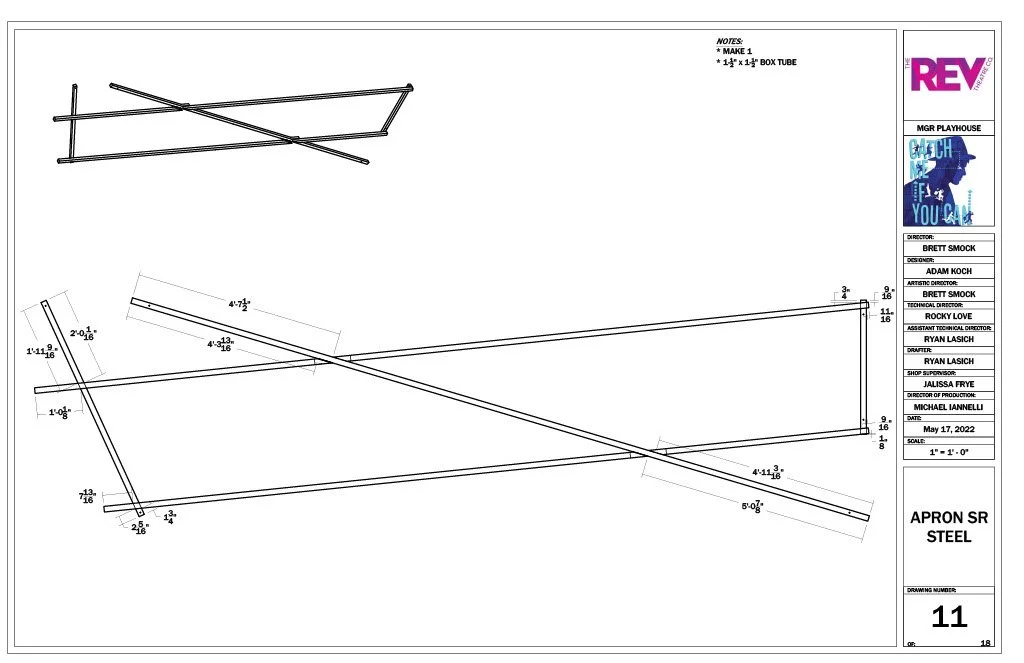
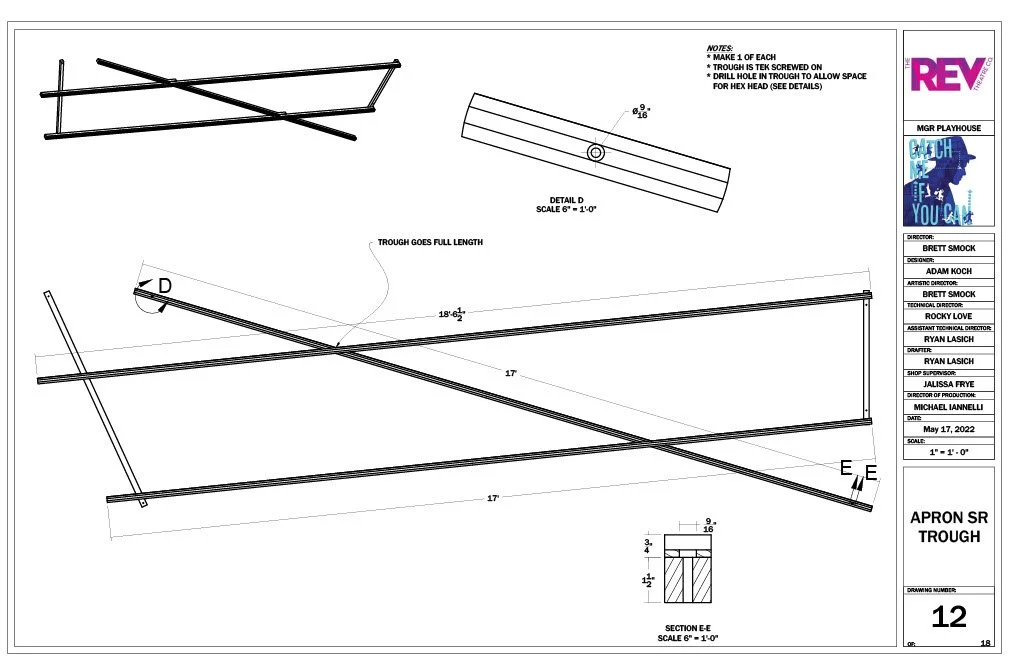


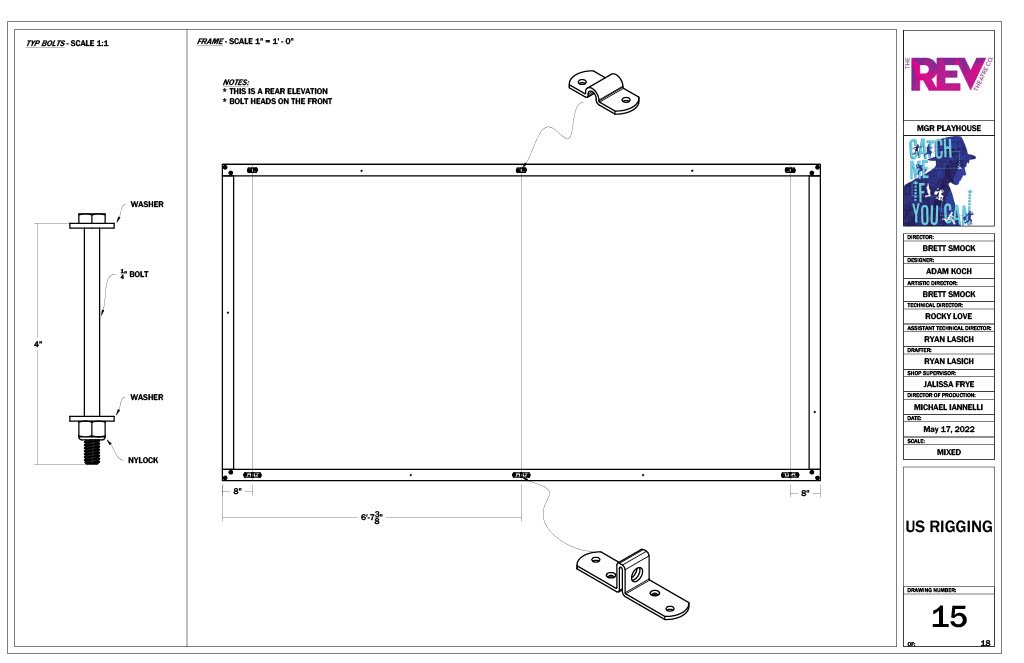

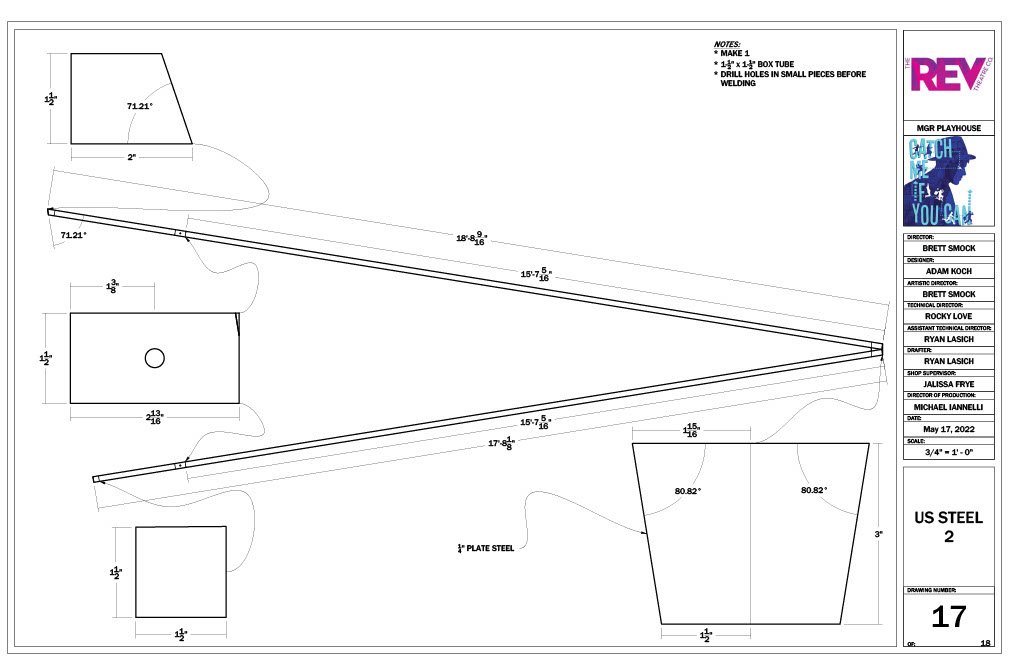

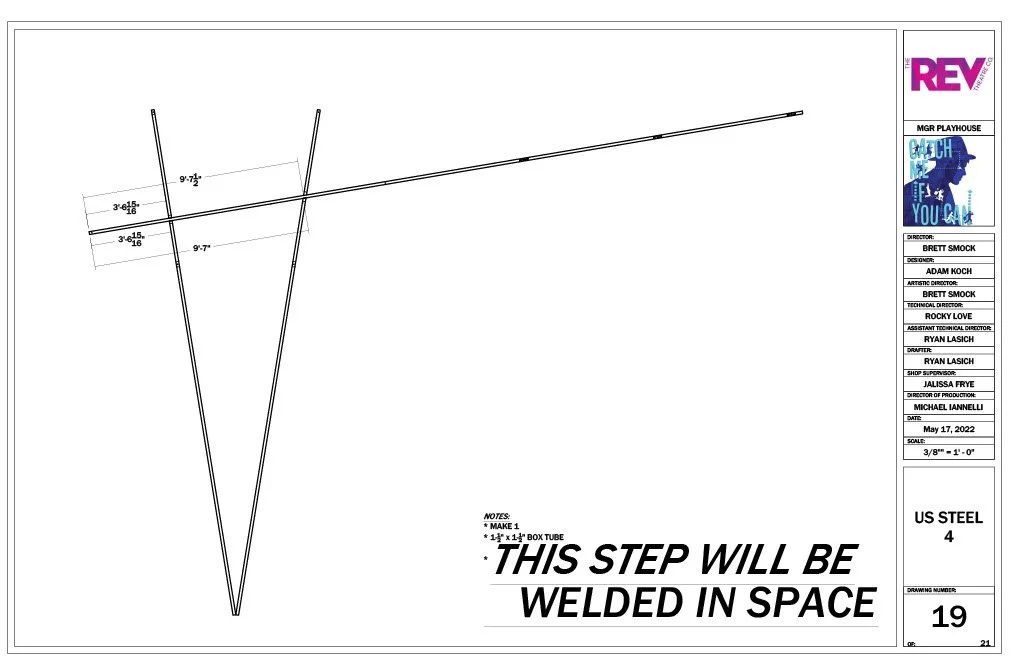


There was a rolling staircase unit that landed at different parts of the upper platform. This was a retrofit of a steel staircase the company had in stock. We had to cut the stairs down and weld it back together to finish the stringer. It was legged and added to a platform.
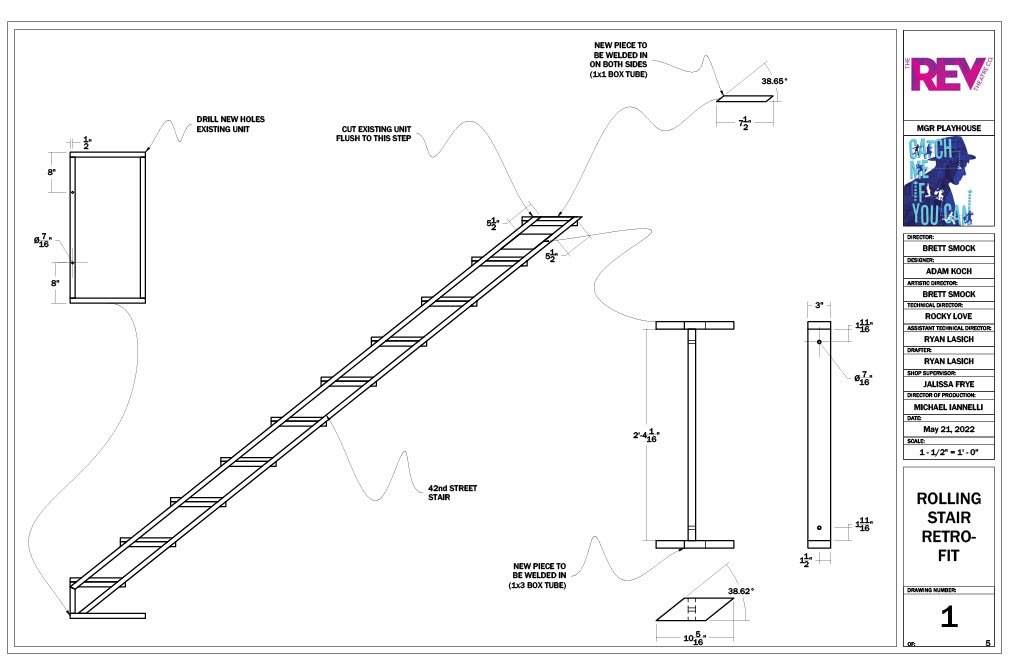
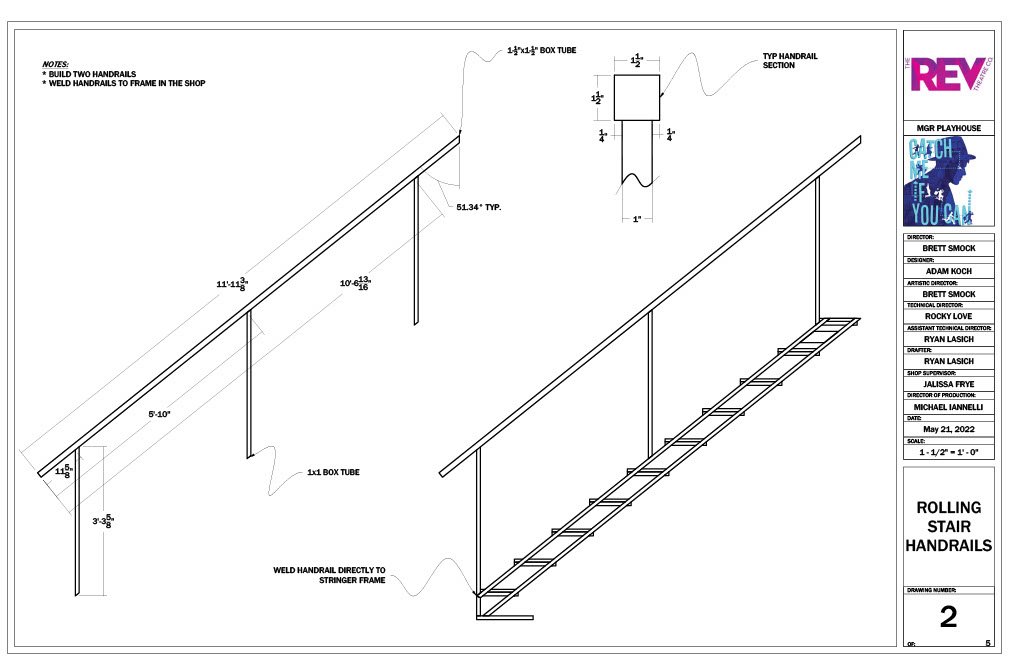
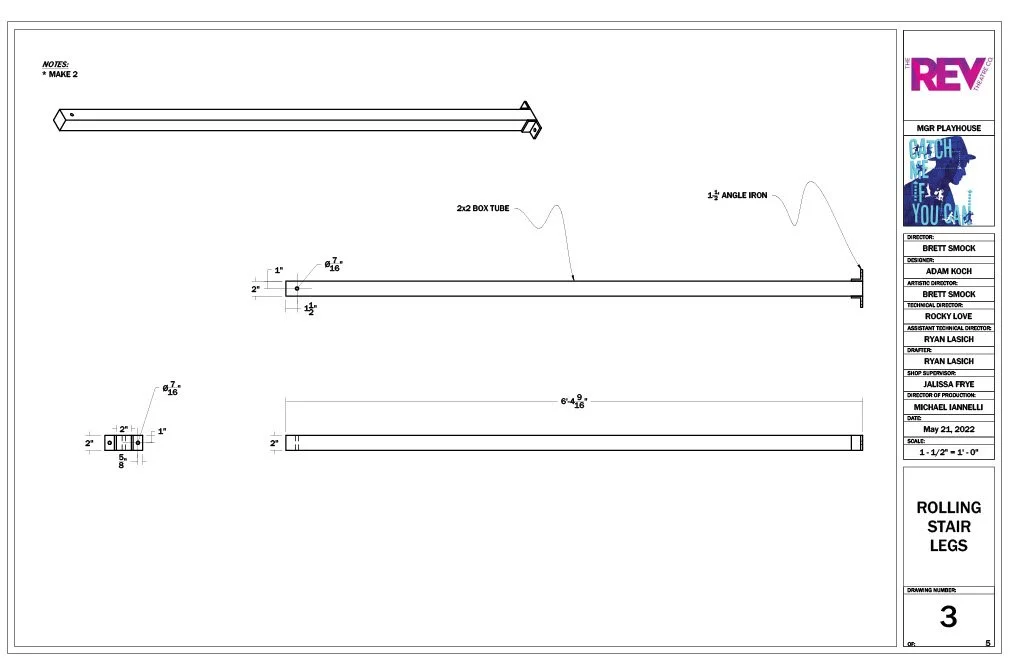
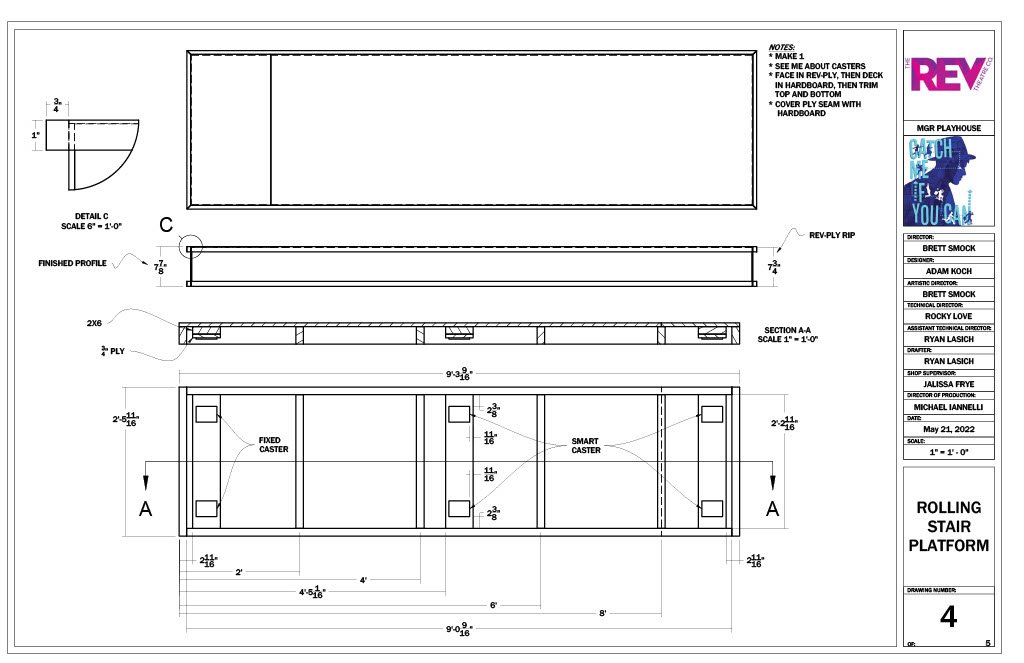
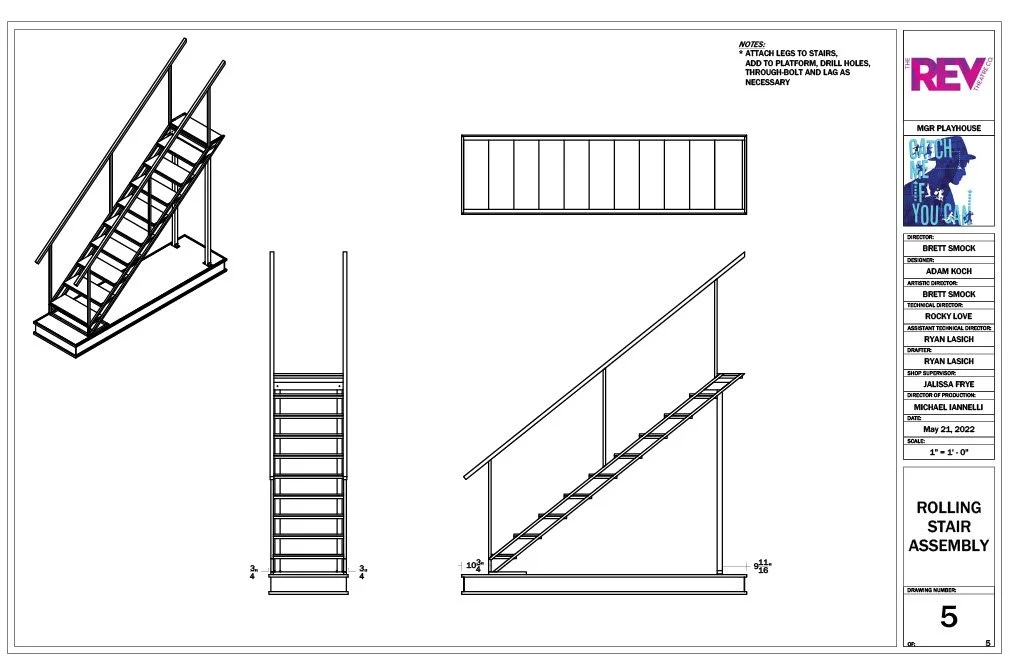
Below is a selection of publicity photos, see credits after gallery.

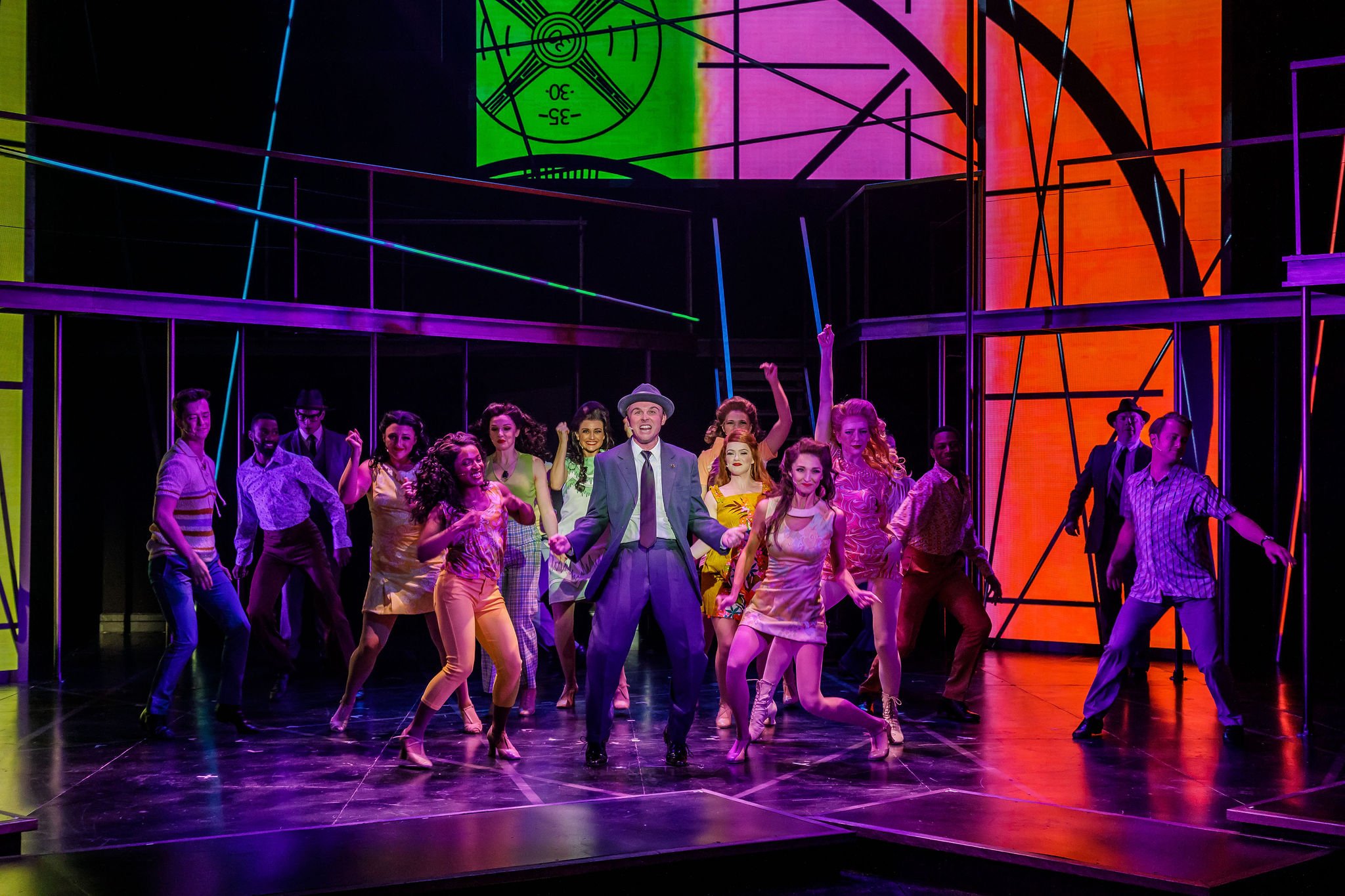
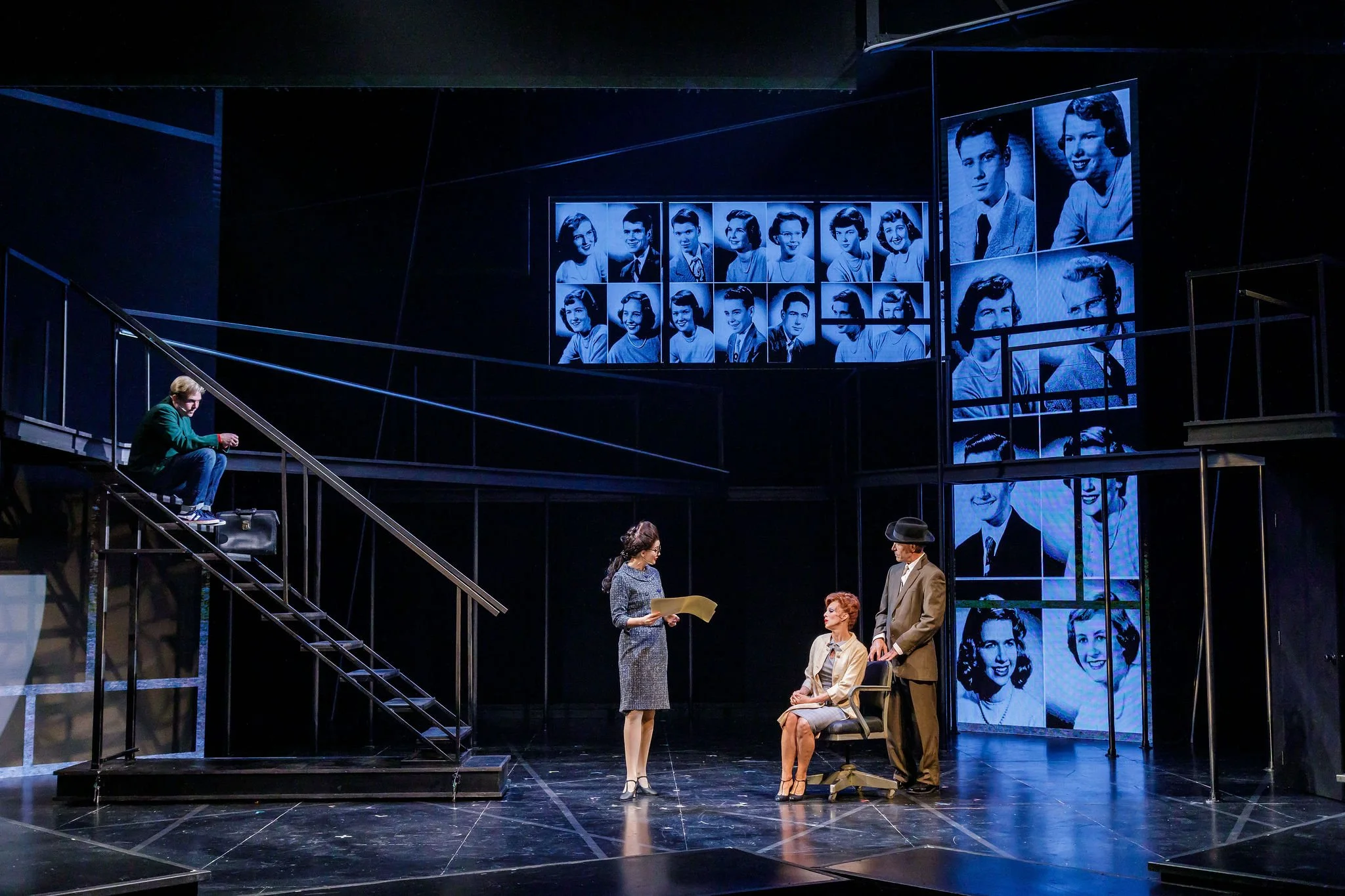

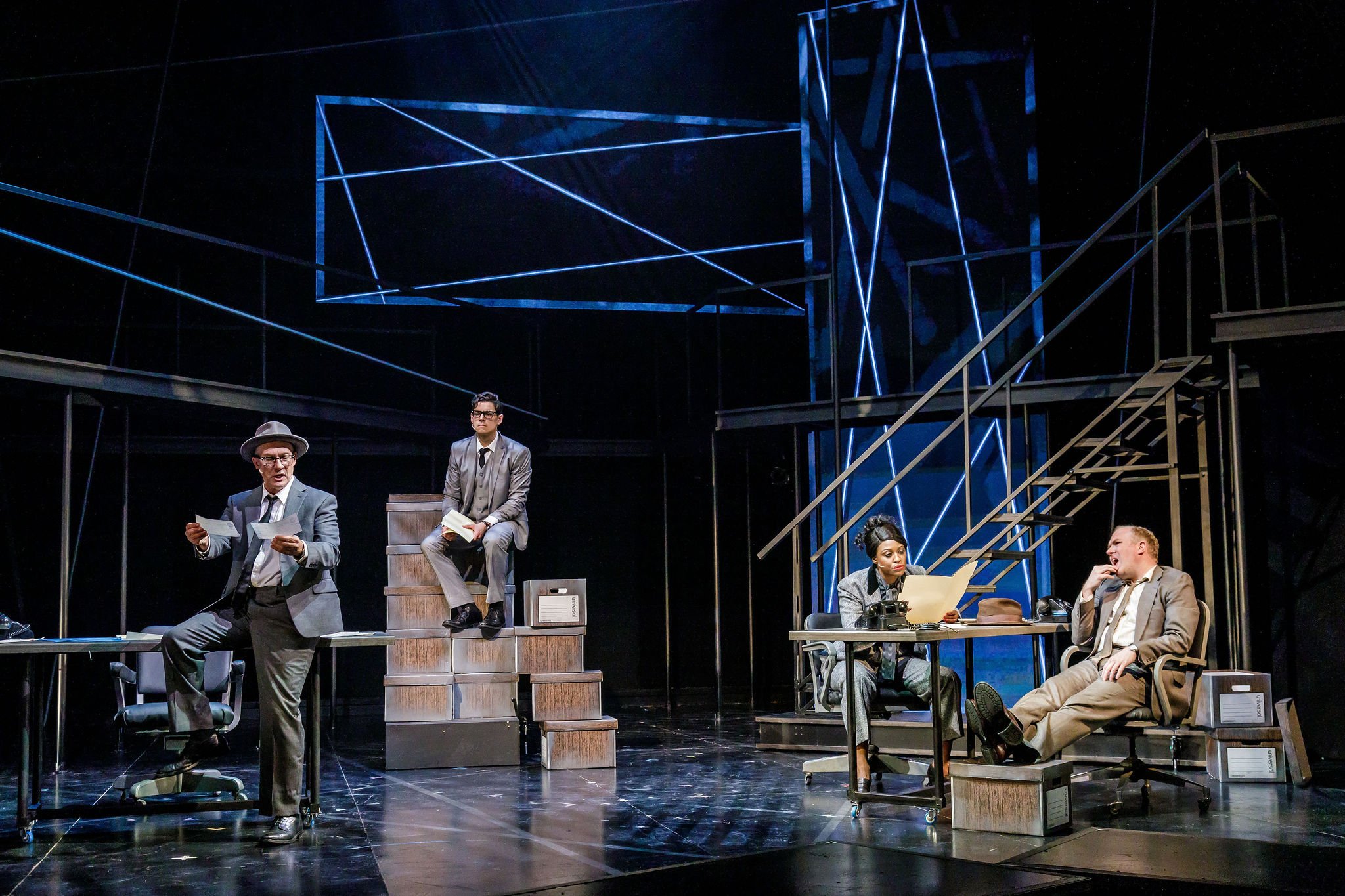
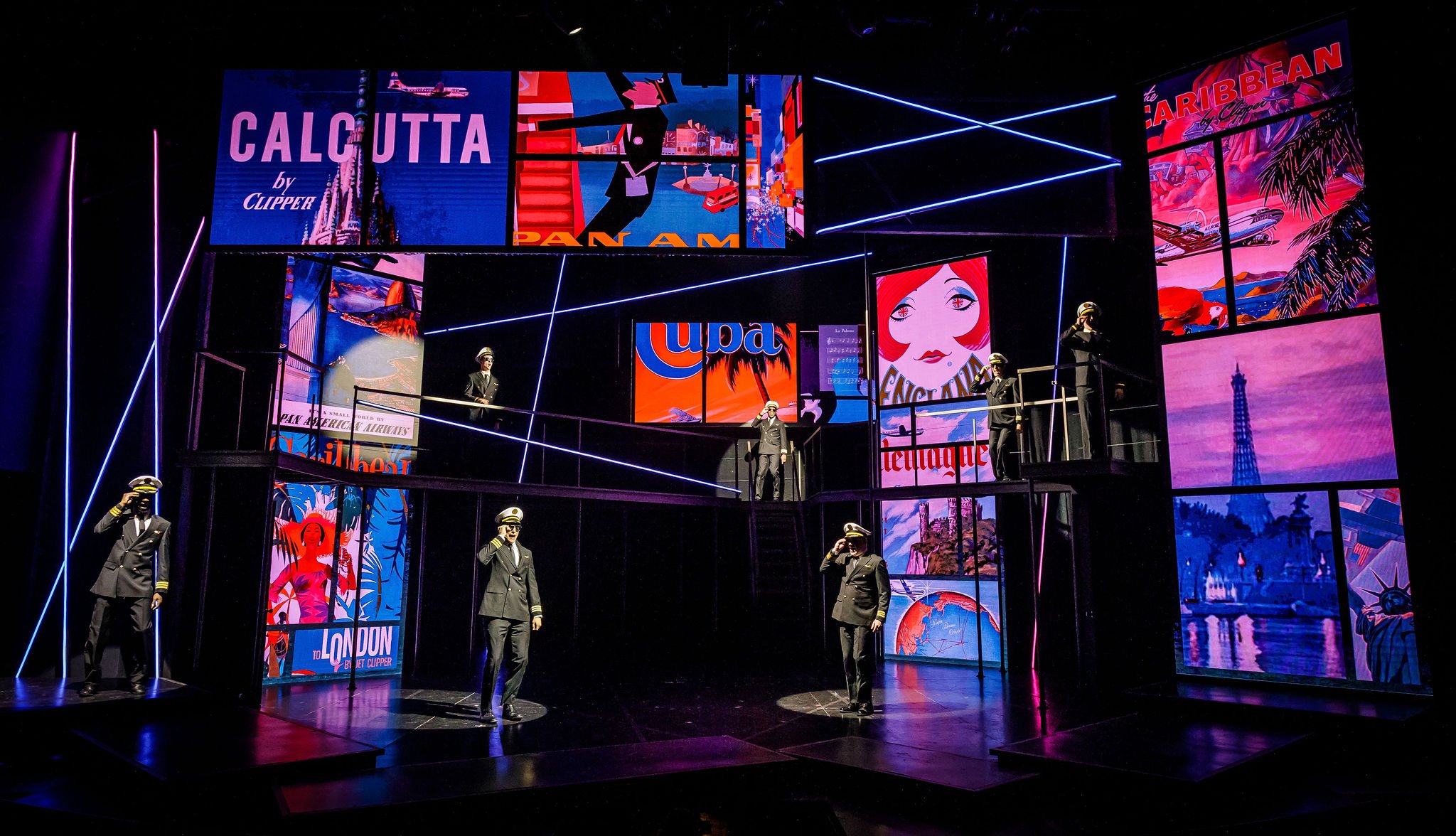


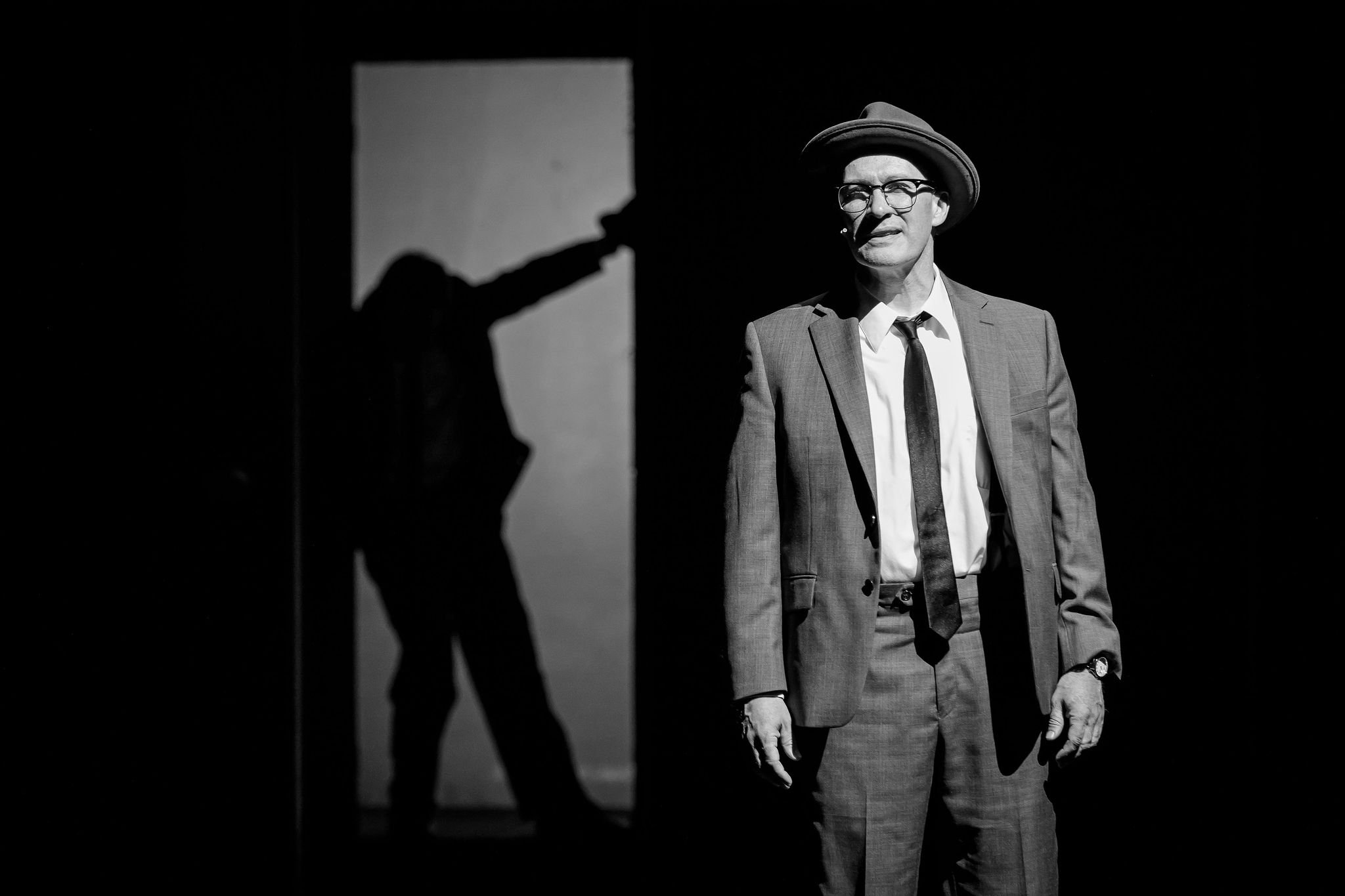


Production Photo credits:
Ron Heerkens Jr. / Goat Factory Media Entertainment
FB: @Goat Factory Media Entertainment
Twitter/Instagram: @gfmedia
Website: goatfactorymedia.com/