
THE HUNCHBACK OF NOTRE DAME
The Rev Theatre Company
Directed by Brett Smock
Scenic Design:
Jeffrey D. Kmiec
Lighting Design:
Jose Santiago
Costume Design:
Tiffany Howard
Wig Design:
Alfonso Annotto
Sound Design:
Kevin Heard
Elyssa Kohen
Summer 2022, Assistant Technical Director
The Hunchback of Notre Dame is the classic story of the hidden recluse in a bell tower. For this production, our director looked at the team and asked “if we’re in a bell tower, why not just build a bell tower?” This question permeates the design in its simplicity. Gold ladders with gothic arches, old wooden floors, and bells. Hunchback was a great example of not doing much, but doing it well.
Hunchback had a very minimal design, and I took on as much as I could. I started with the the large platform centerstage. It was a 1’ tall platform, surrounded by a 6” step, and came with its own small challenges. The first challenge was the lighting inset into the deck. Each of the steel ladders were up-lit by units in the deck under plexiglass. I wanted the lights to be accessible at any time in case they needed to be serviced. This lead to removeable portions of 3/4” ply laminated with masonite to match the final floor treatment. The other major challenge was the 6” platform needed to extend over the edge of the stage into the audience. The front of the stage had facing that stuck up a couple of inches and was not removeable, so the platform framing had to be notched to fit. The legs also had to come down to the concrete floor in the audience so the structure had to be self supporting. Below is my drafting package for the platform. You can download the PDF version of the package using the button below.
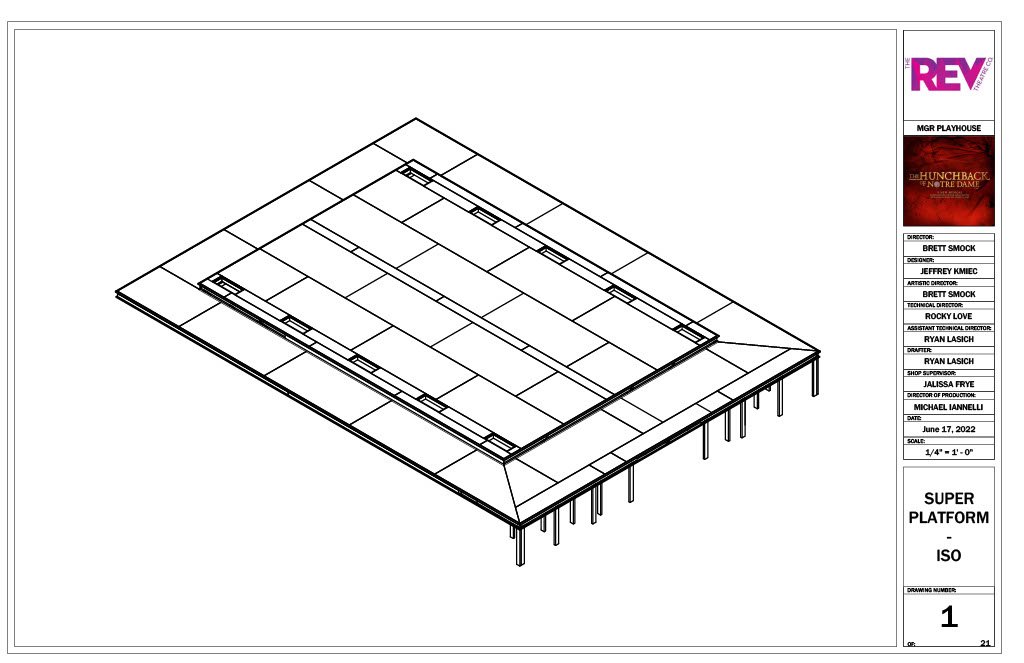
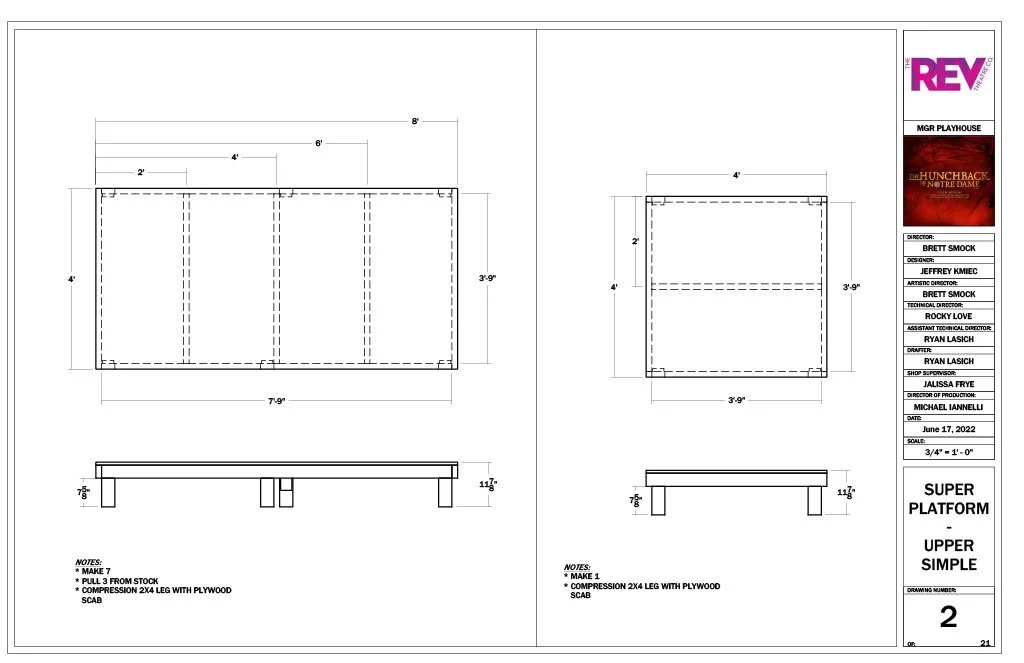

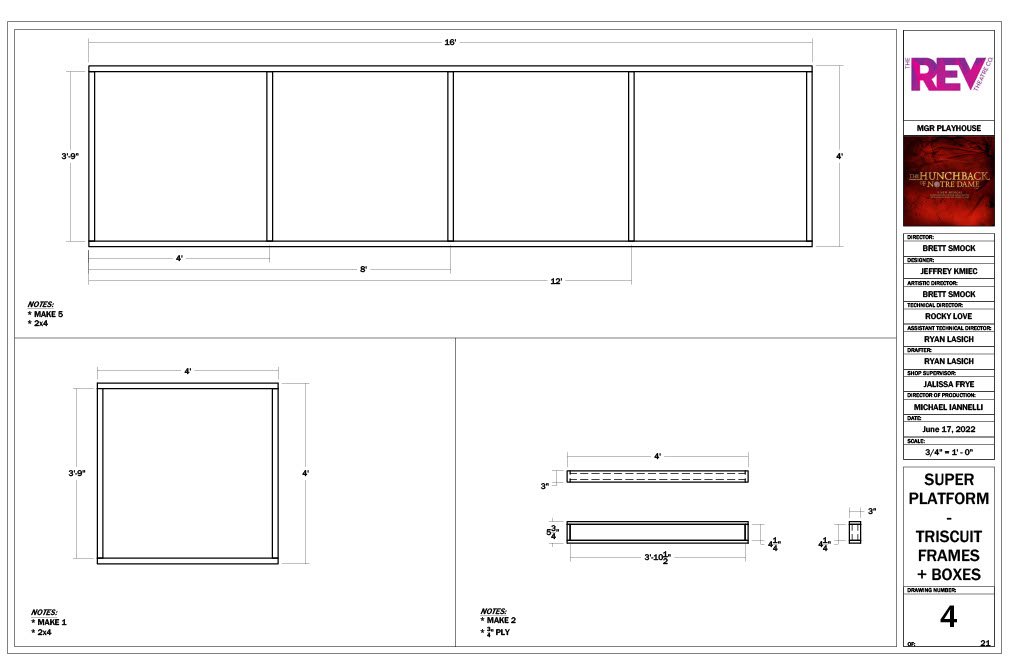
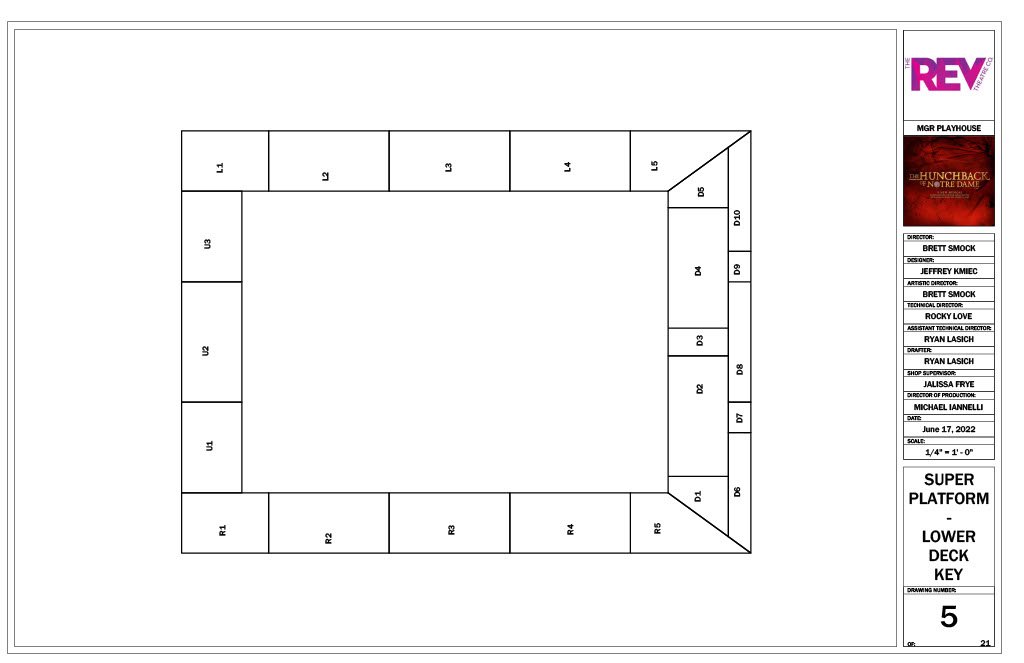
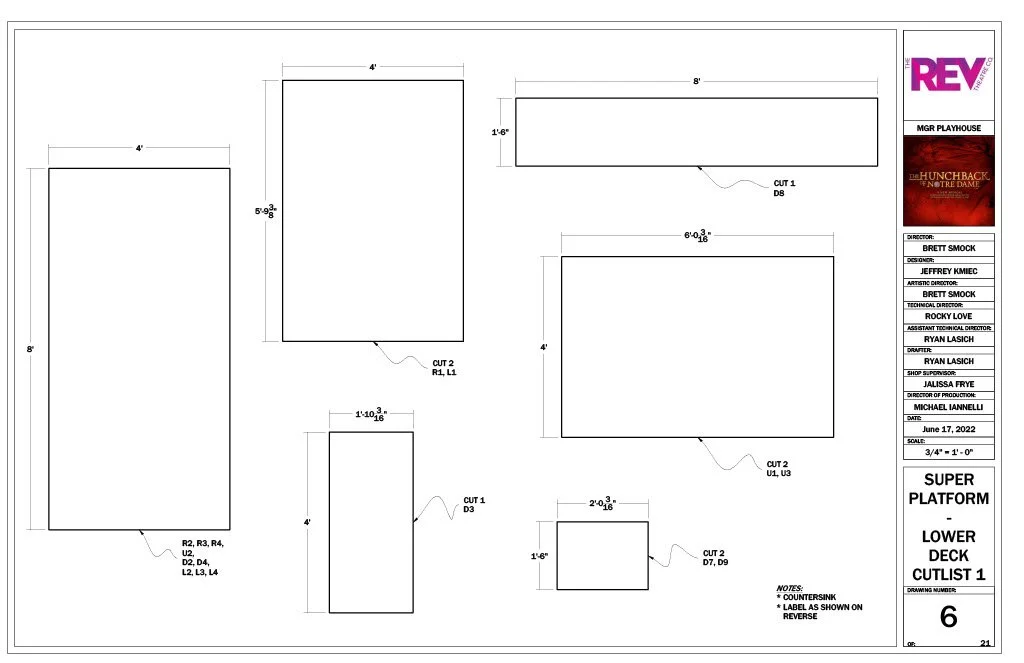
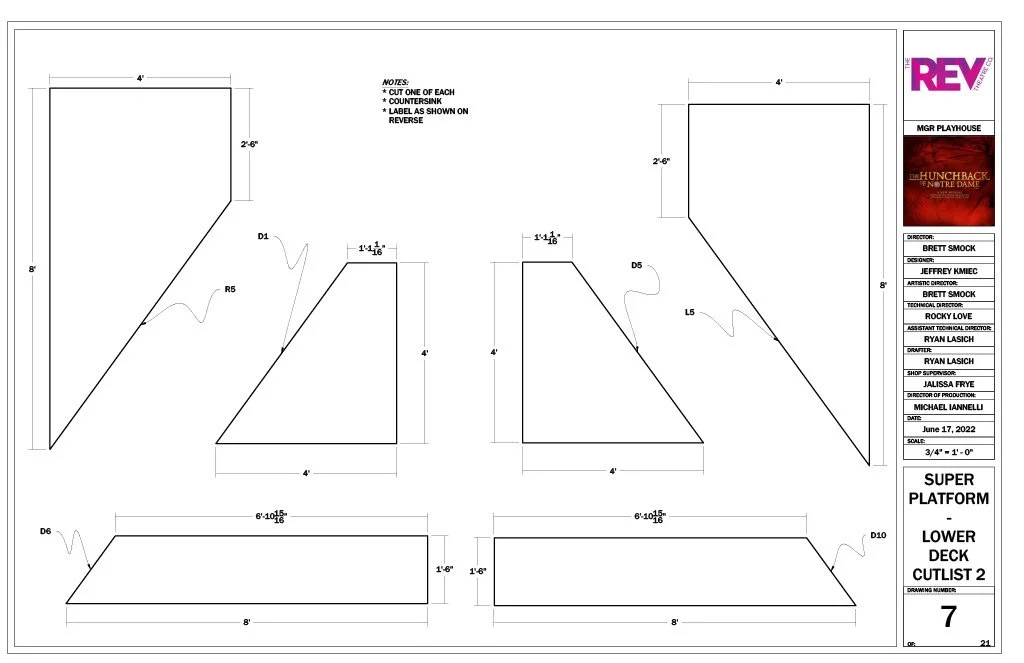
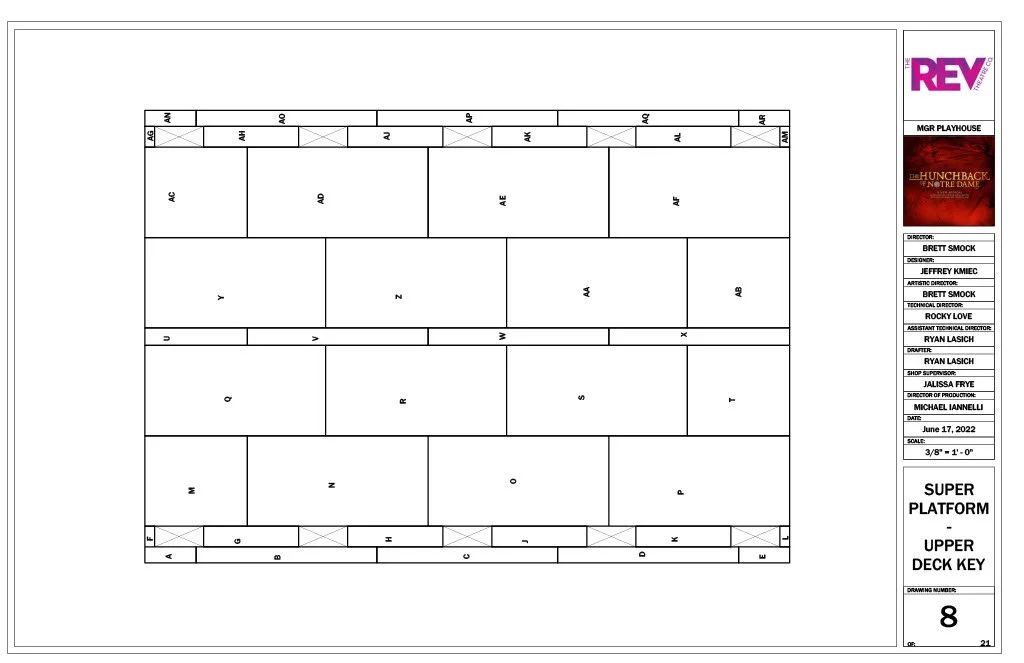

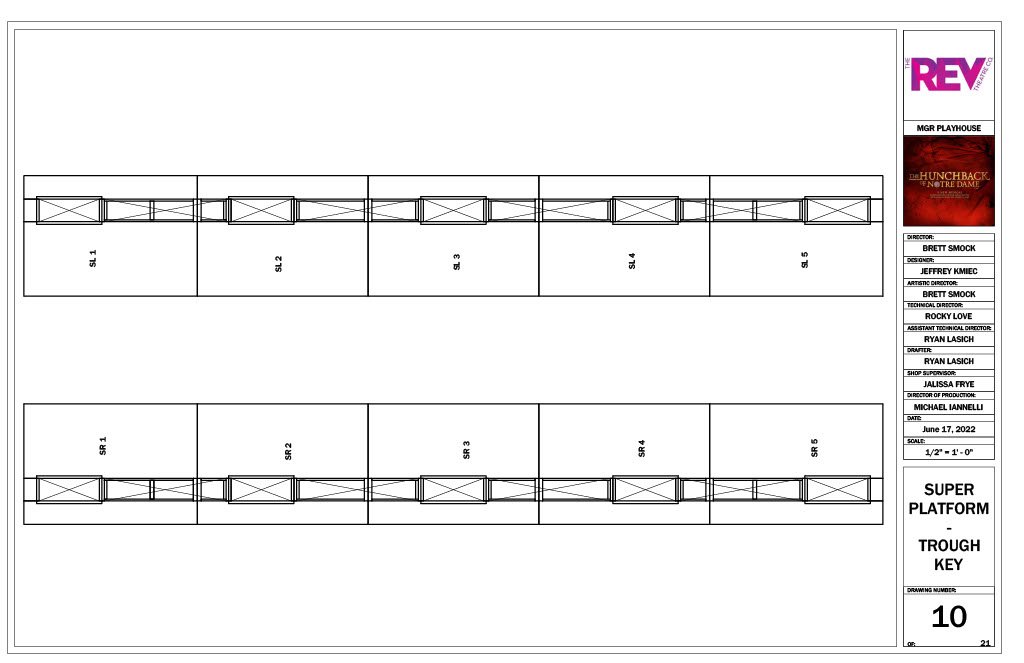
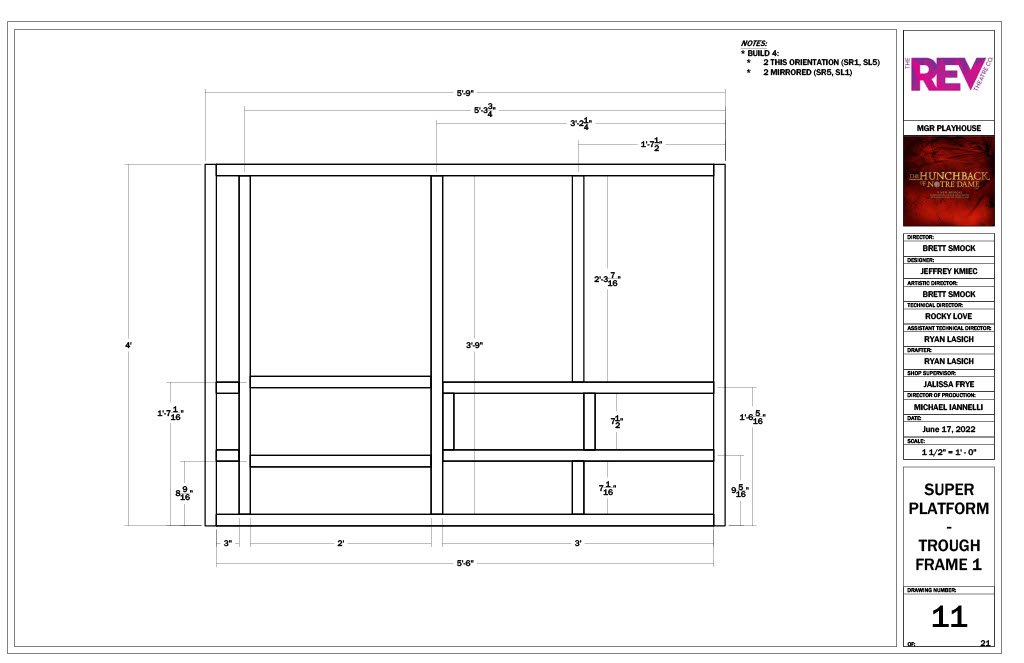
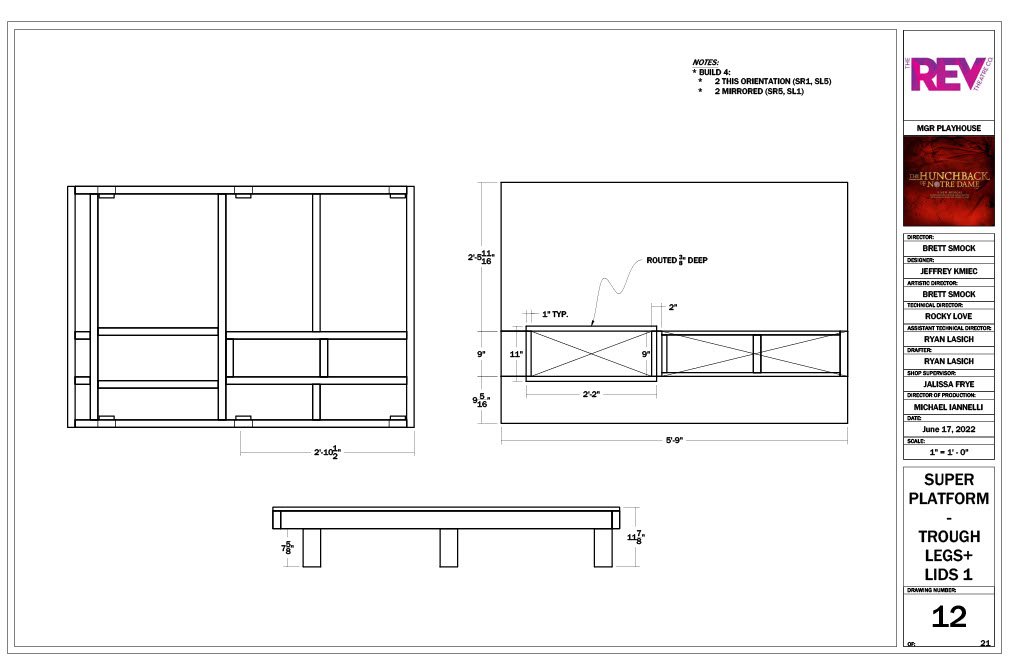



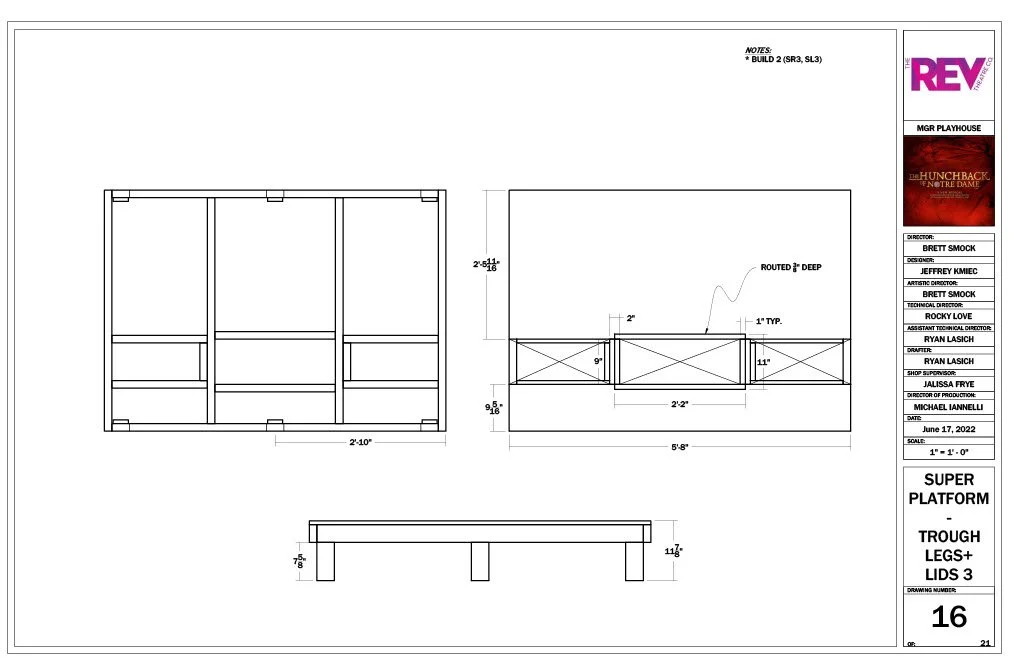
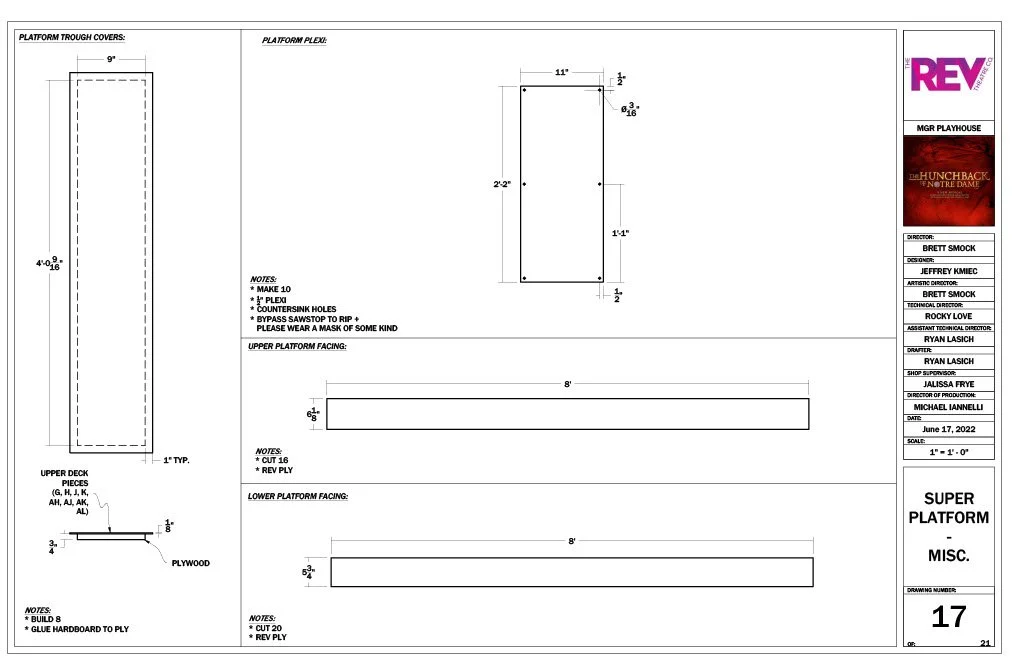
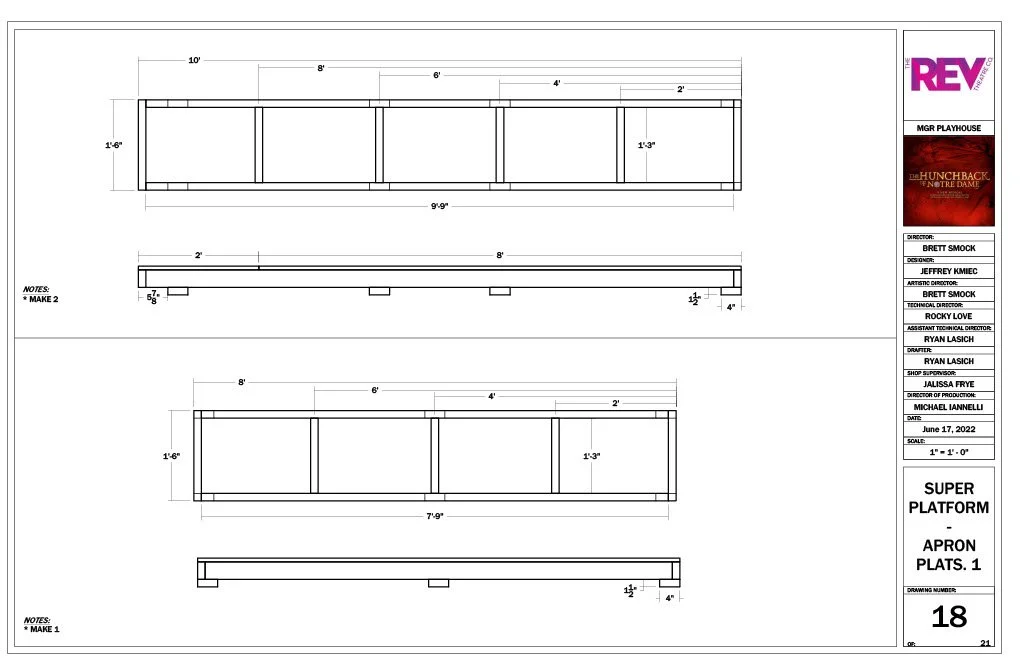
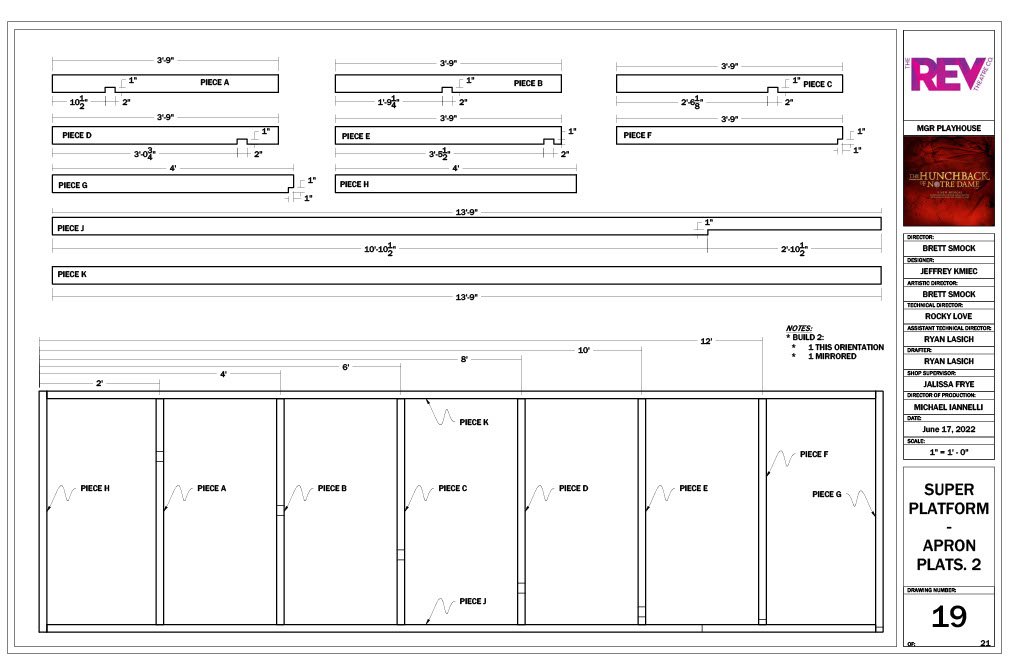

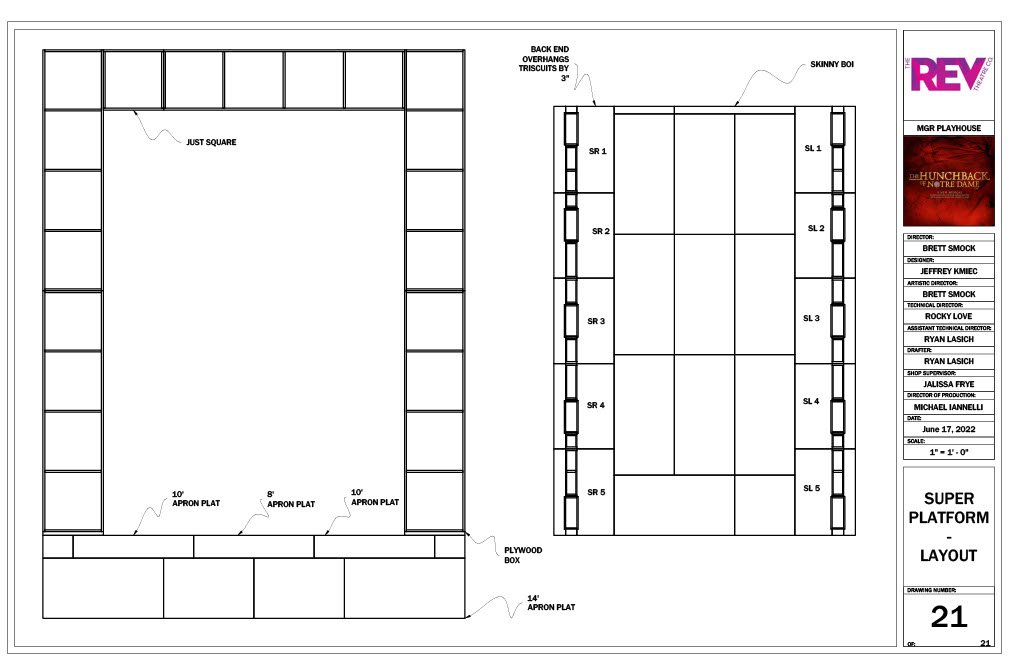
My next project was creating the iconic bells. We needed 20 identical bells, and our designer plates were a little open for interpretation. The TD came up with bolting two garden platers together to make the actual bell itself, so I was tasked with figuring out the top of the bell. We needed to be able to put a pipe through the bell to hang it and it needed to be able to ring without sound. We also did not have something like a CNC machine, so all of the parts had to be easy to cut and the assembly process had to be easily repeatable. Since the design was minimal I was able to join the shop floor much more during this process, and I greatly enjoyed working with the shop to define this process. We essentially made plywood boxes that had a lot of accents. Some of the parts had templates printed 1:1 on the plotter, and we would trace the other pieces based on the initial cut out. The drafting package below lacks assembly drawings, since I knew I would assemble all of the boxes myself after the carpenters cut out the pieces.
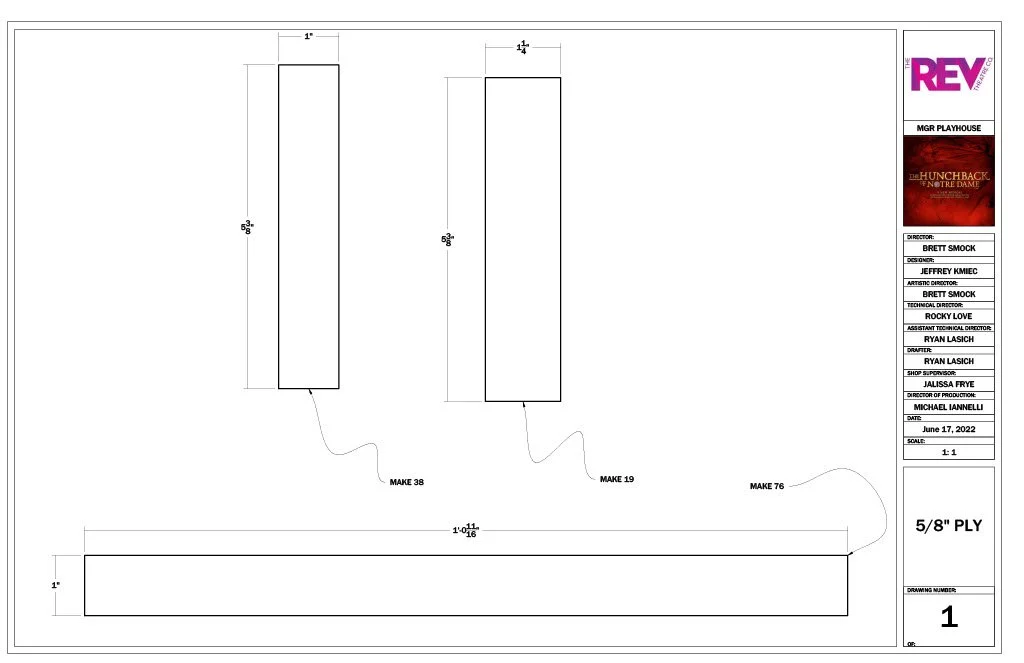
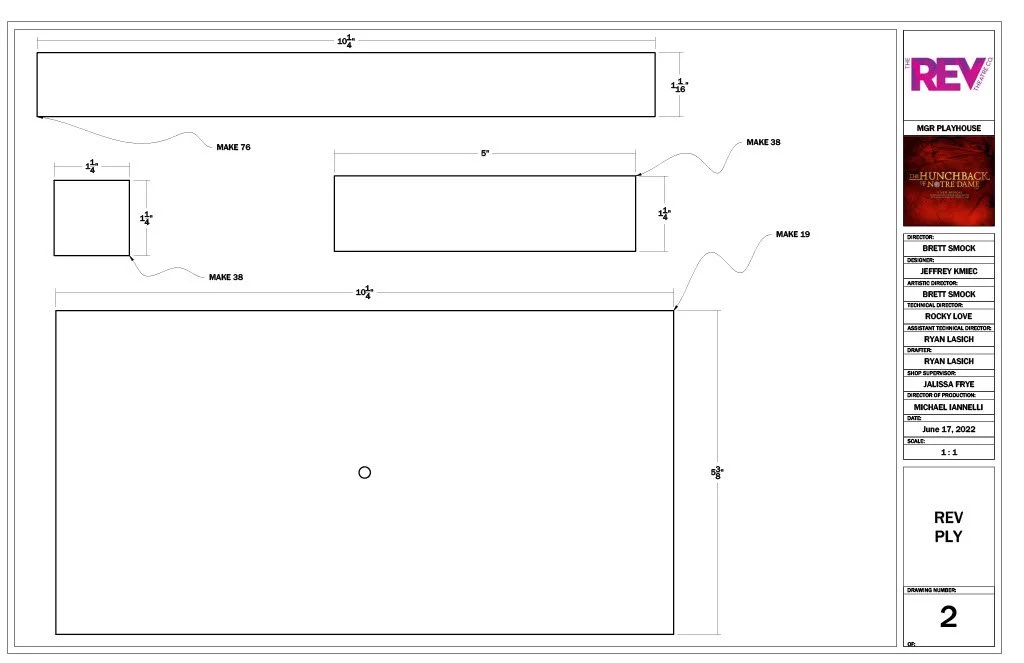

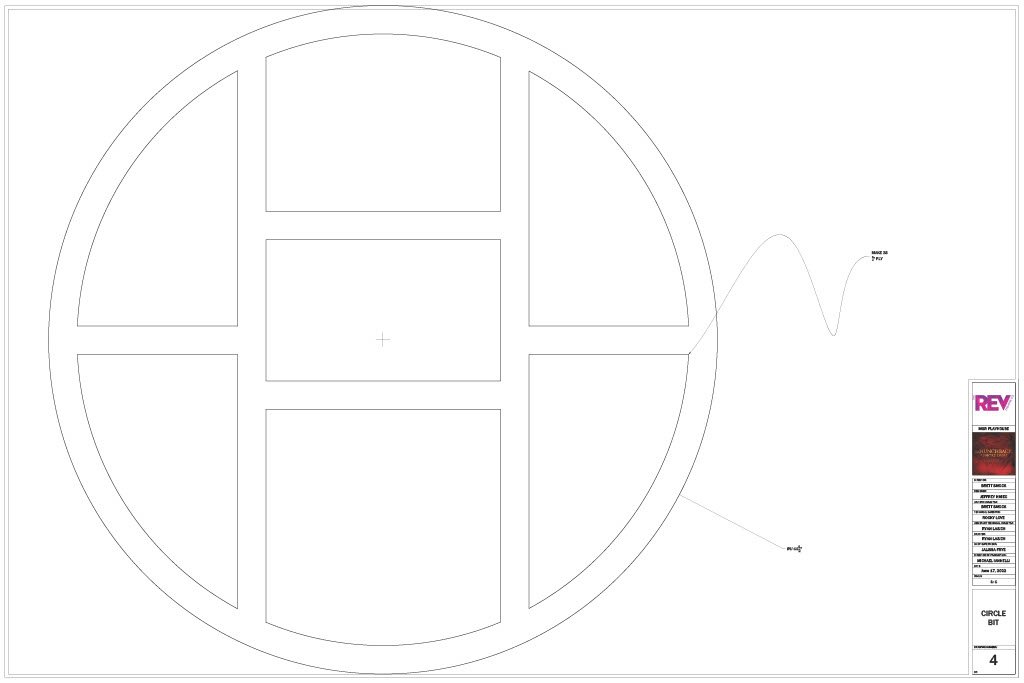
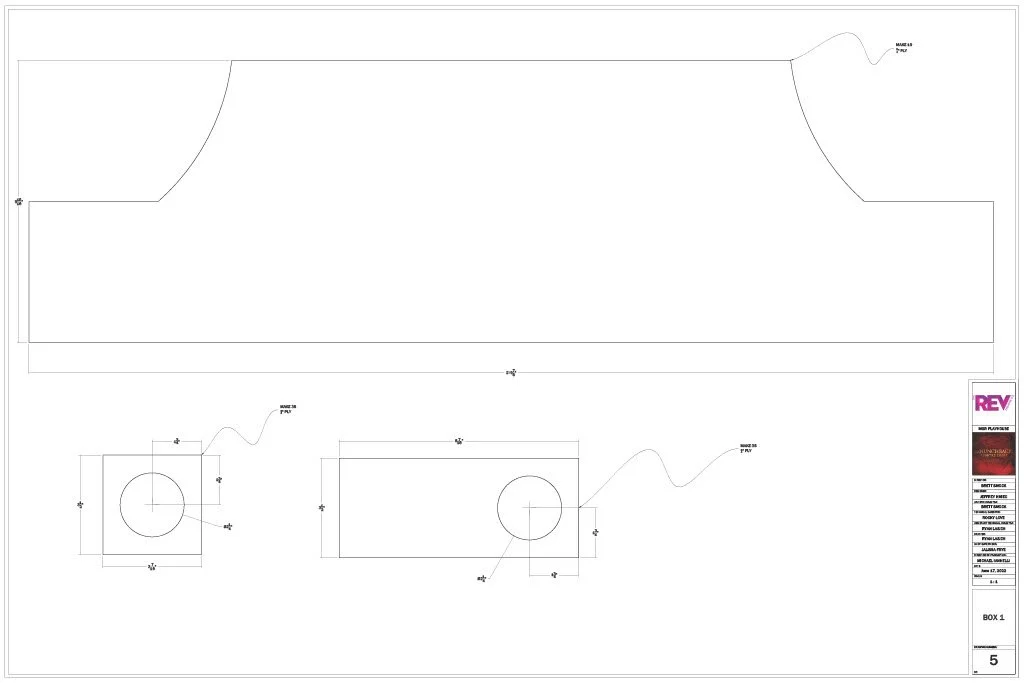
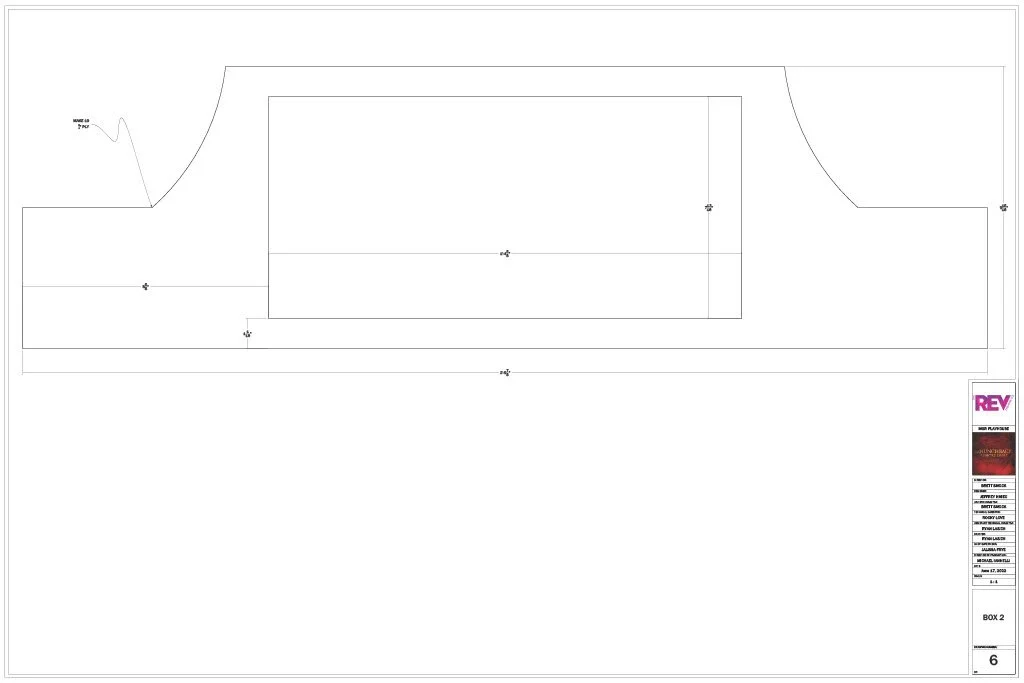
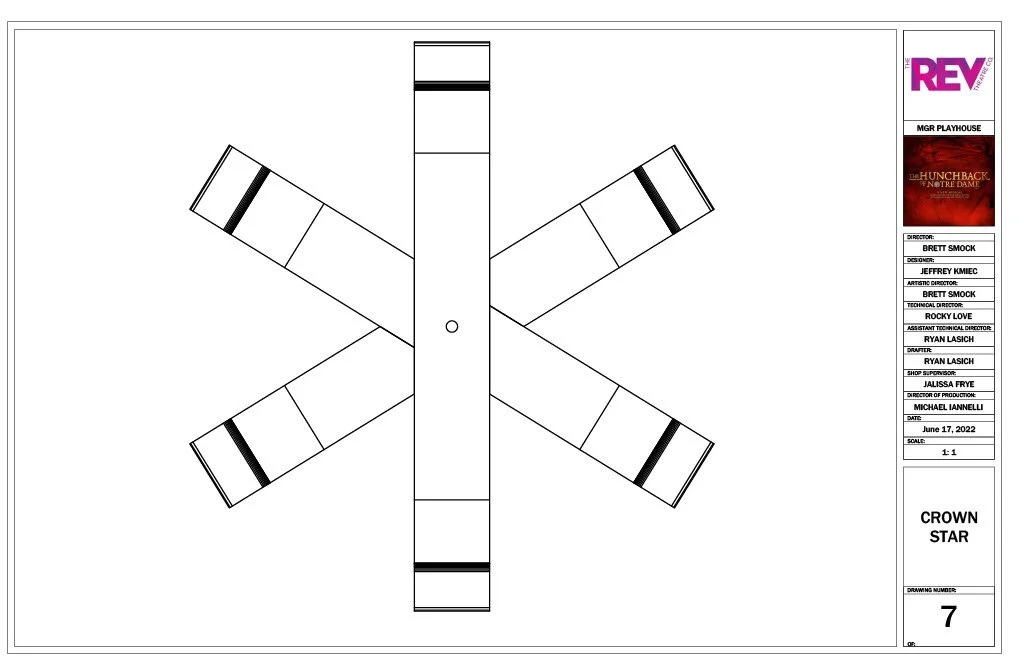
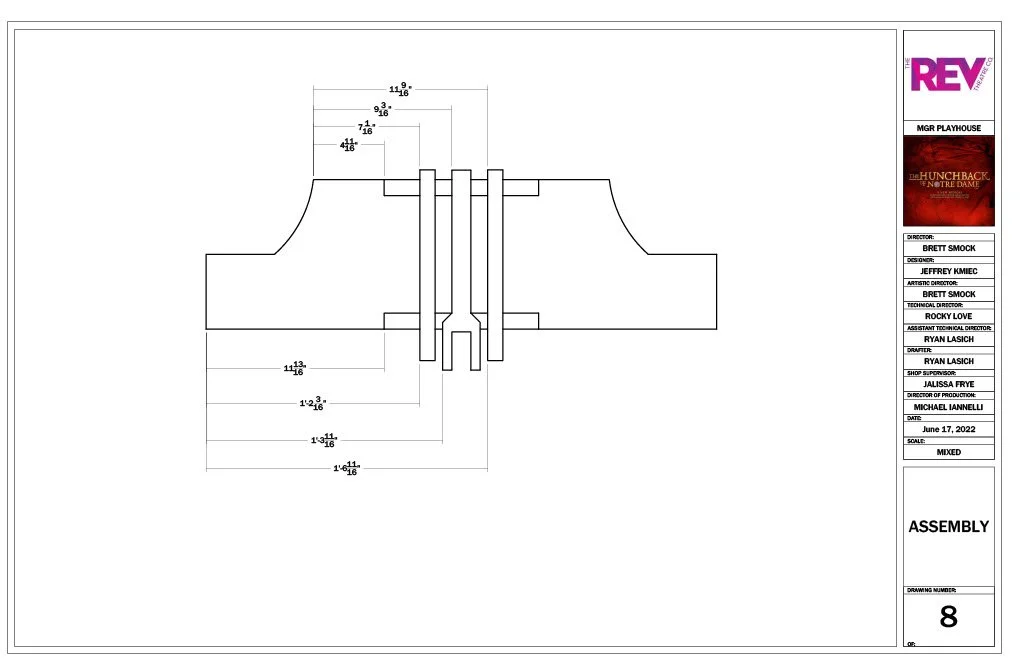
Below are some process photos from the bell process.
Below is a selection of publicity photos, see credits after gallery.

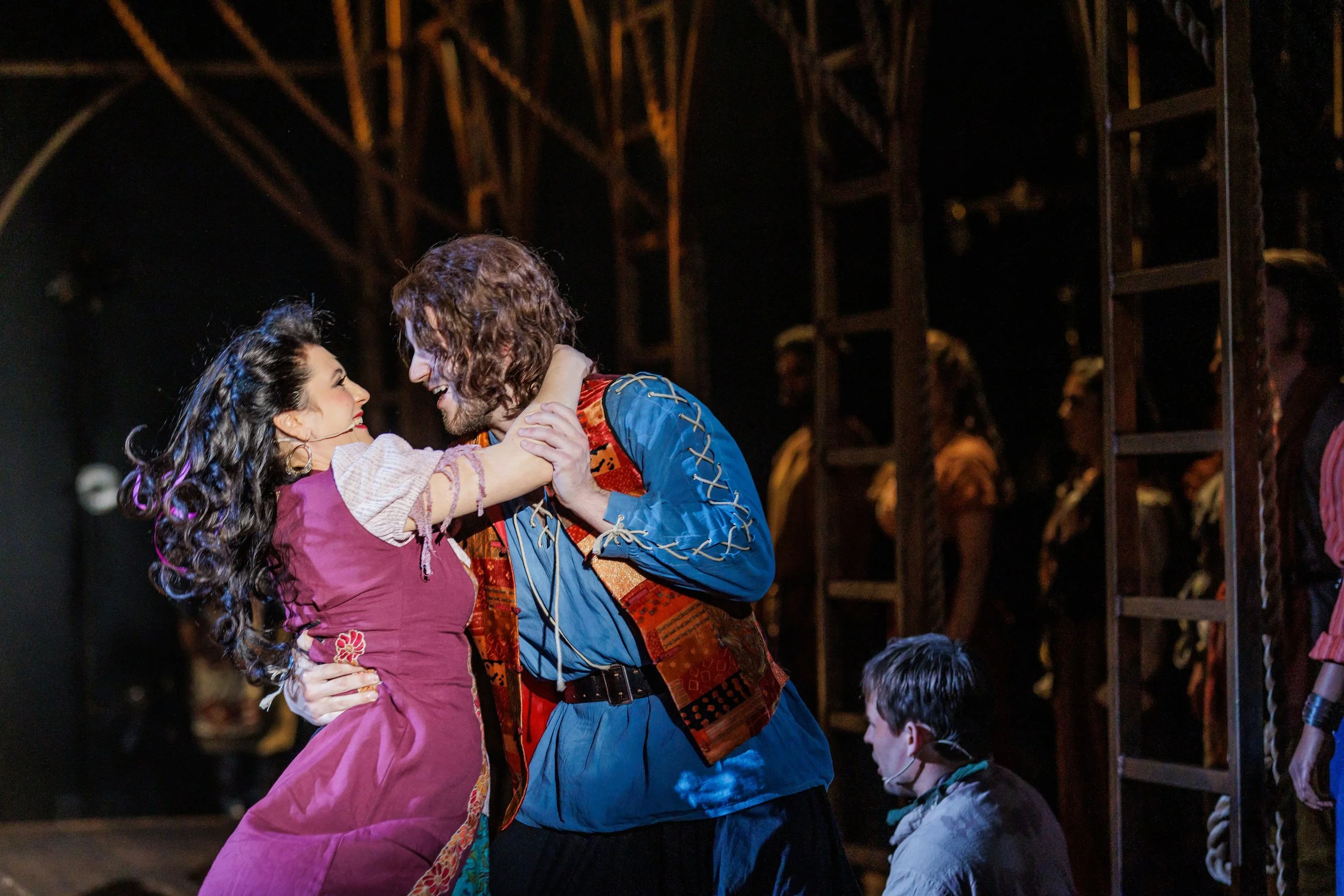
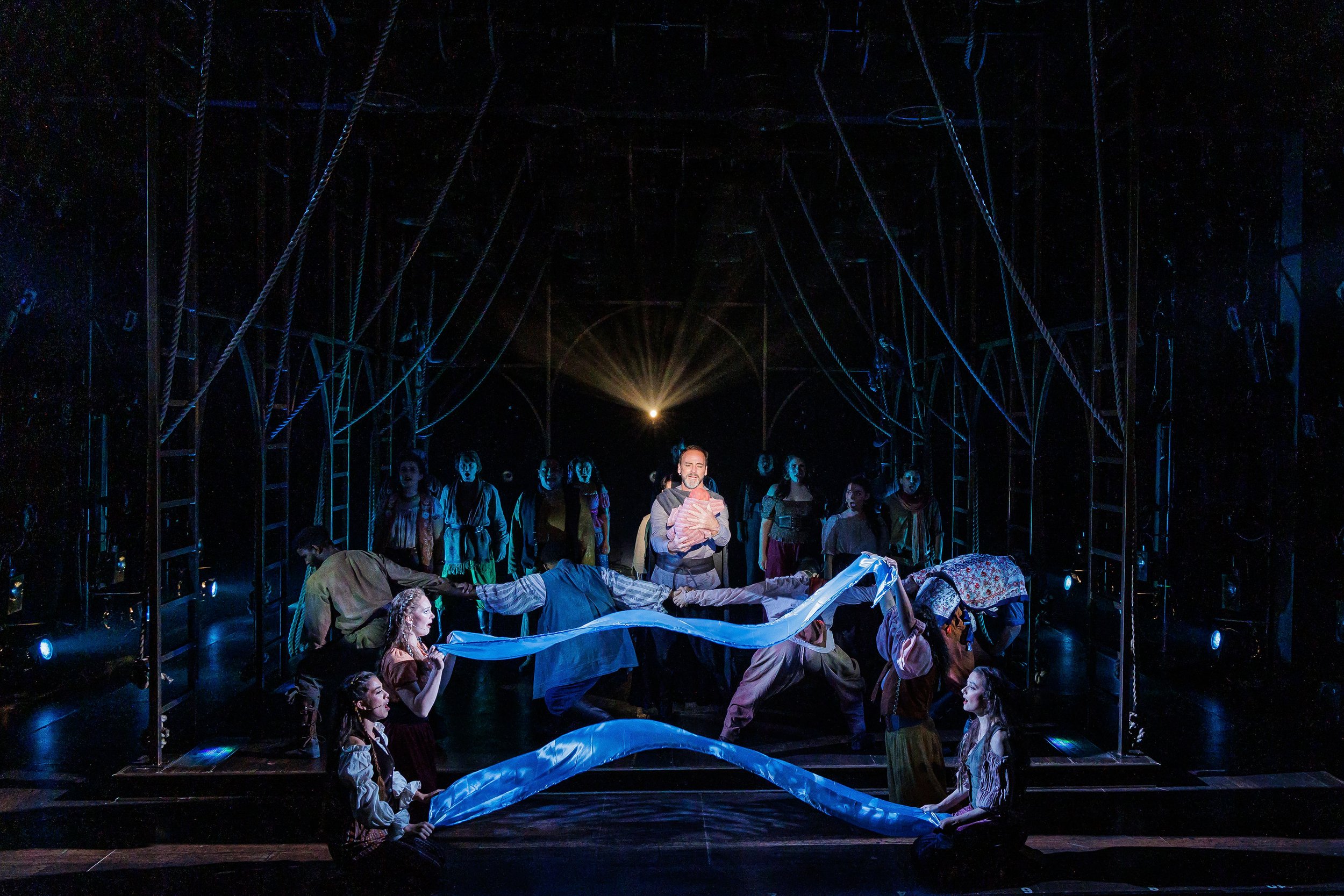
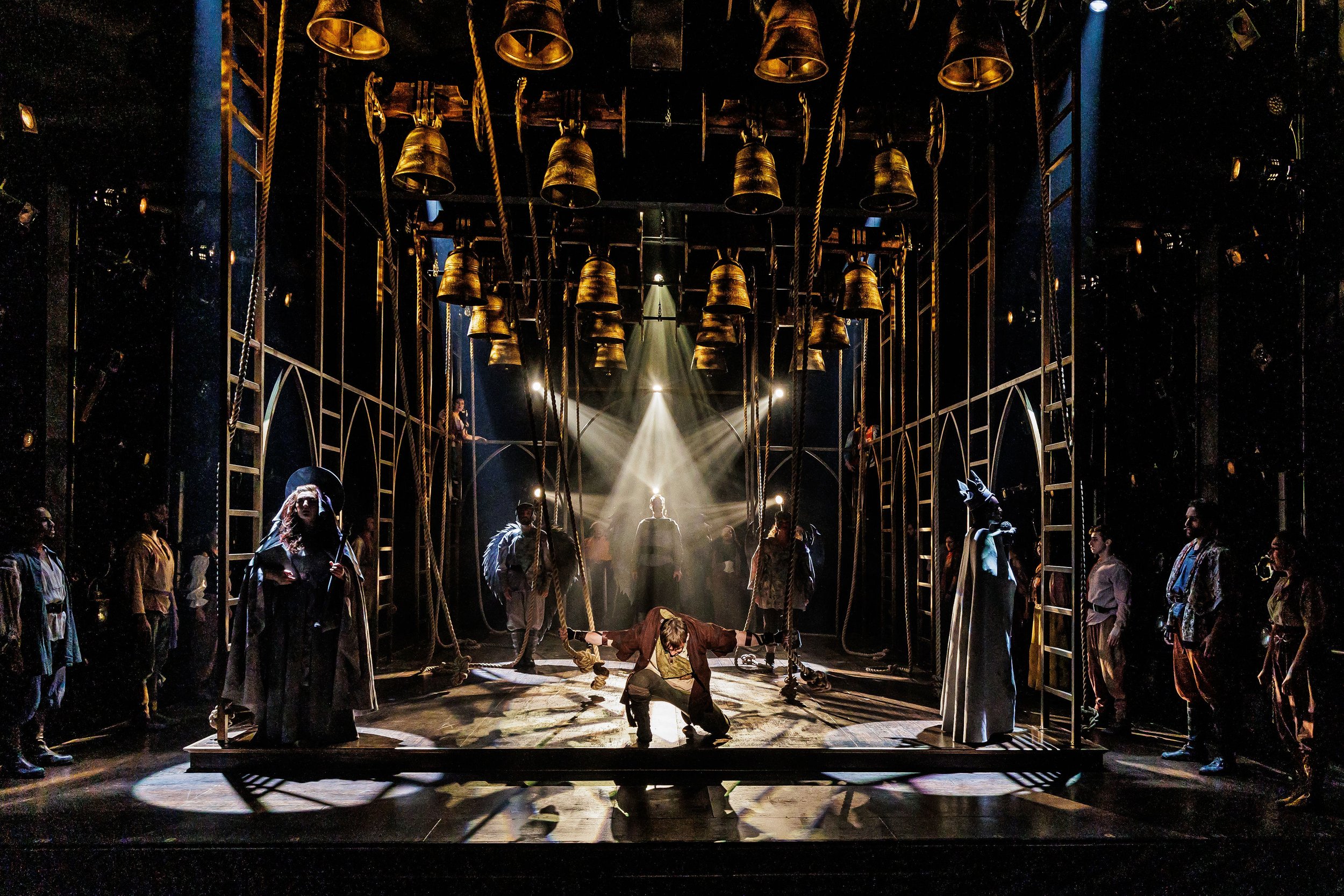
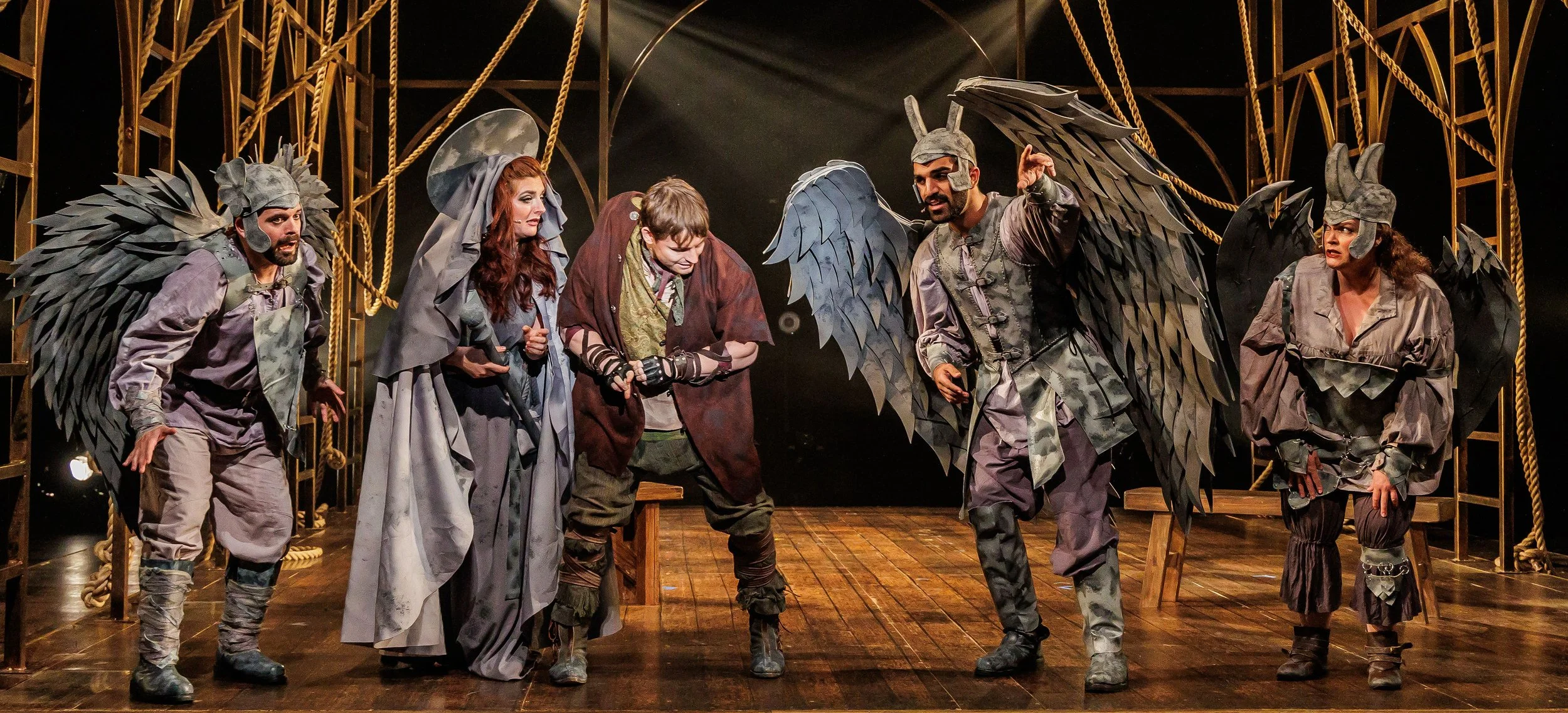
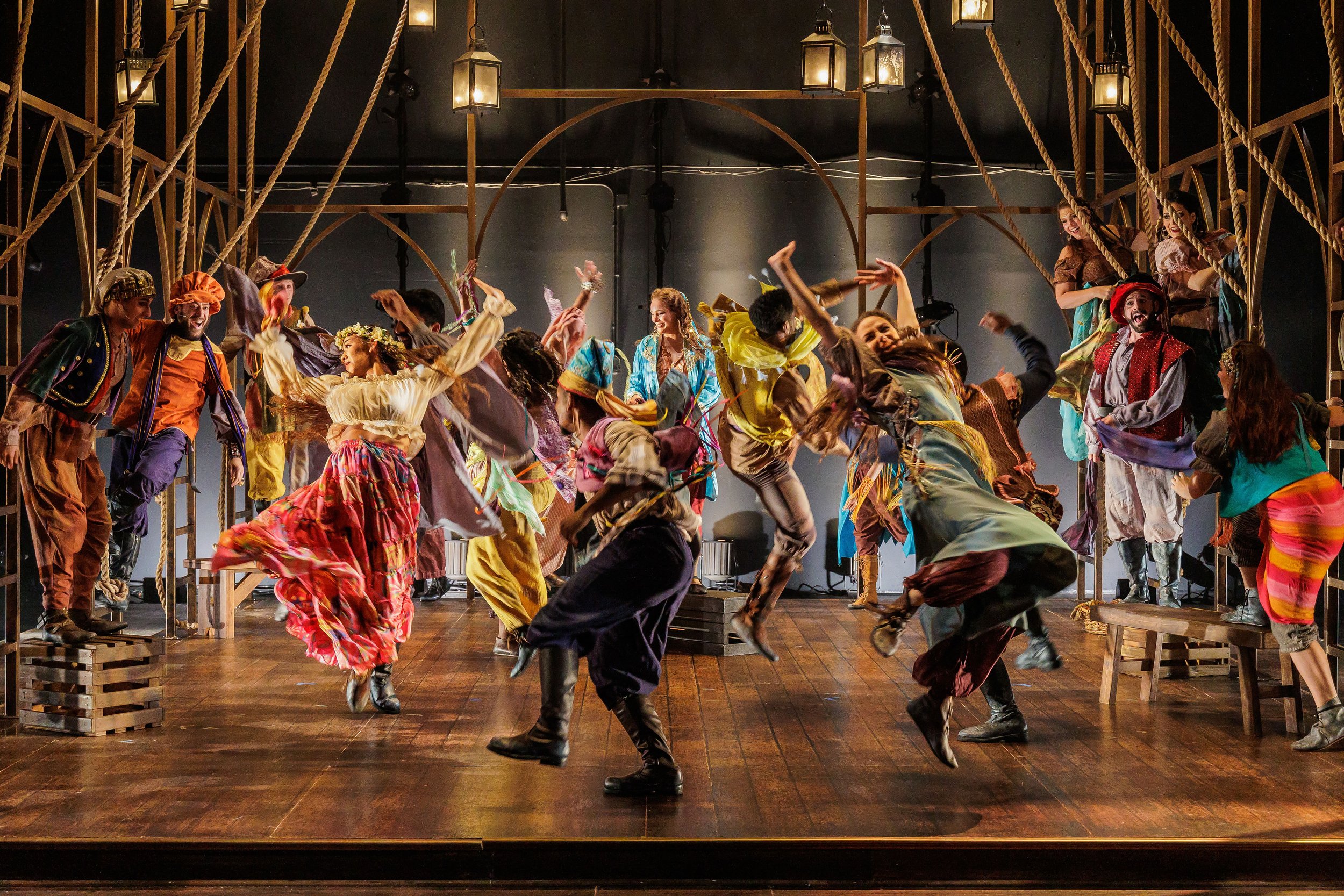

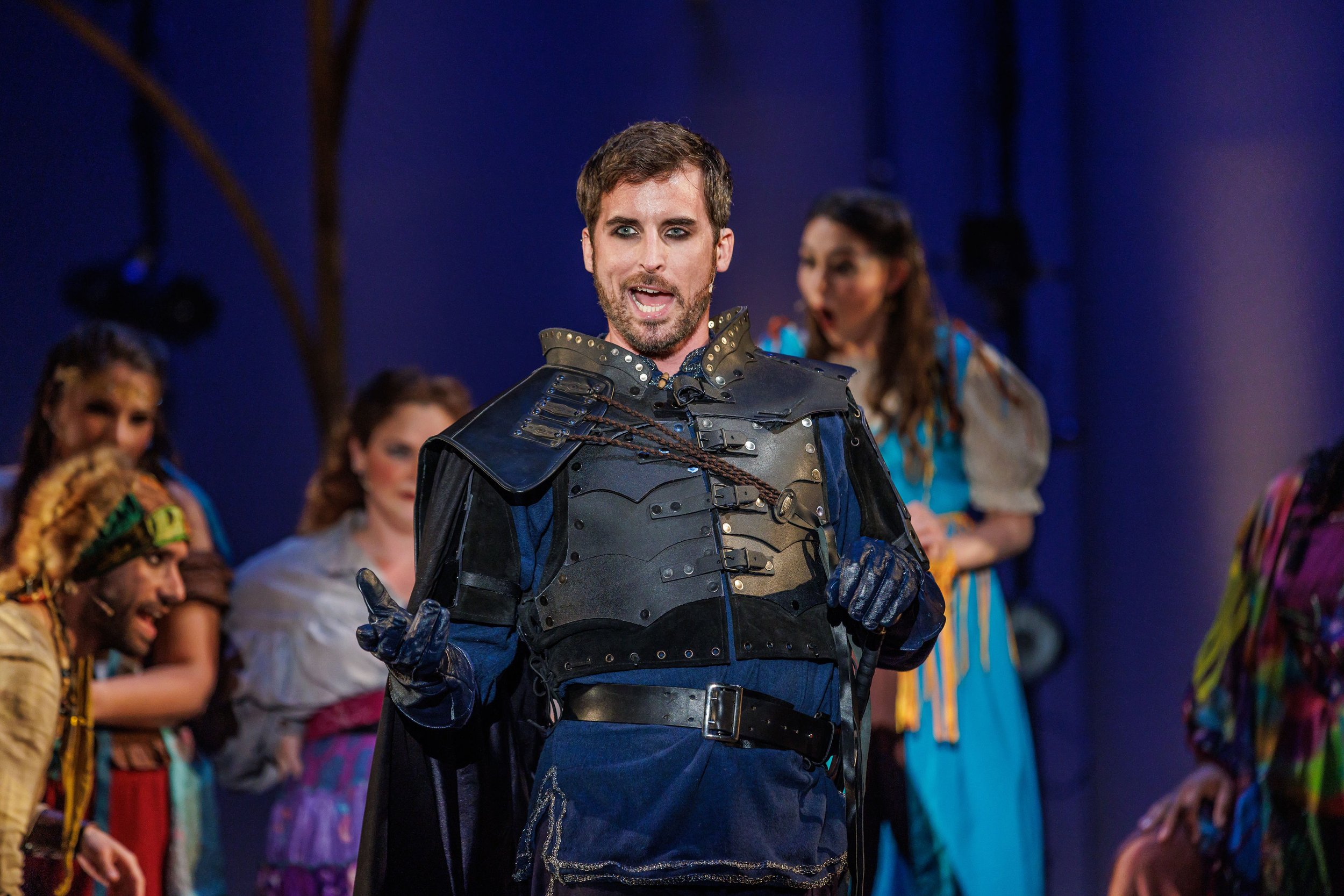
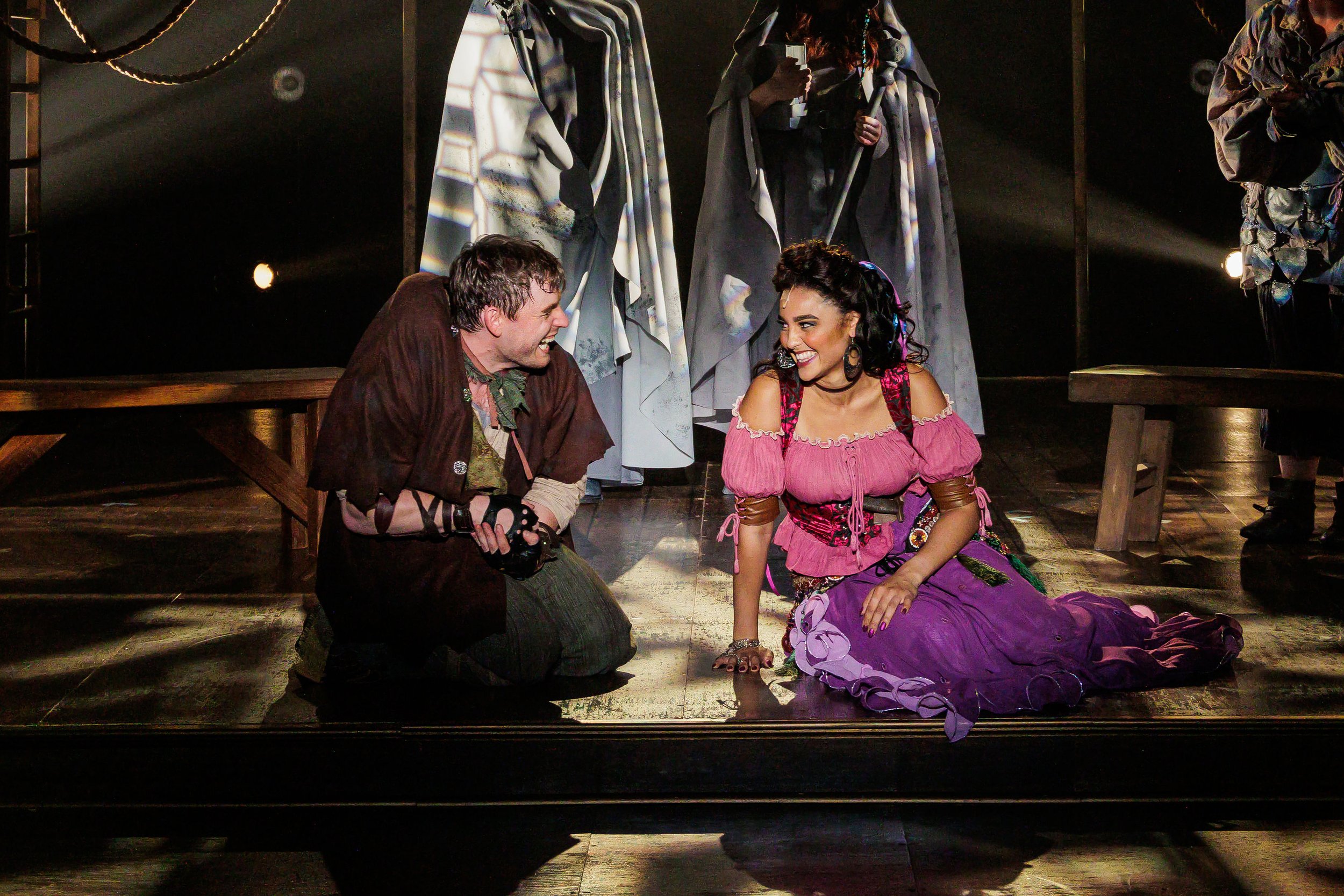
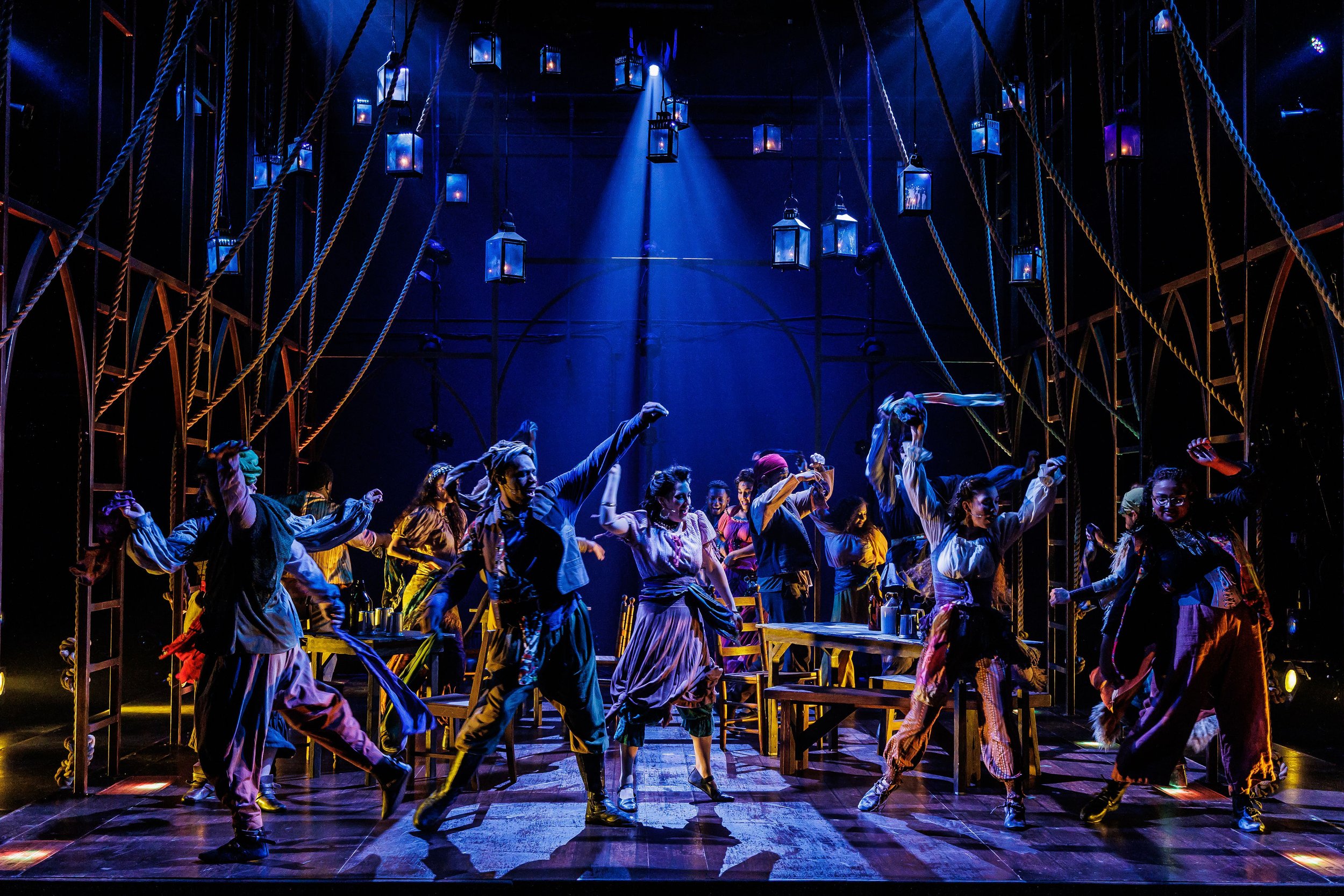


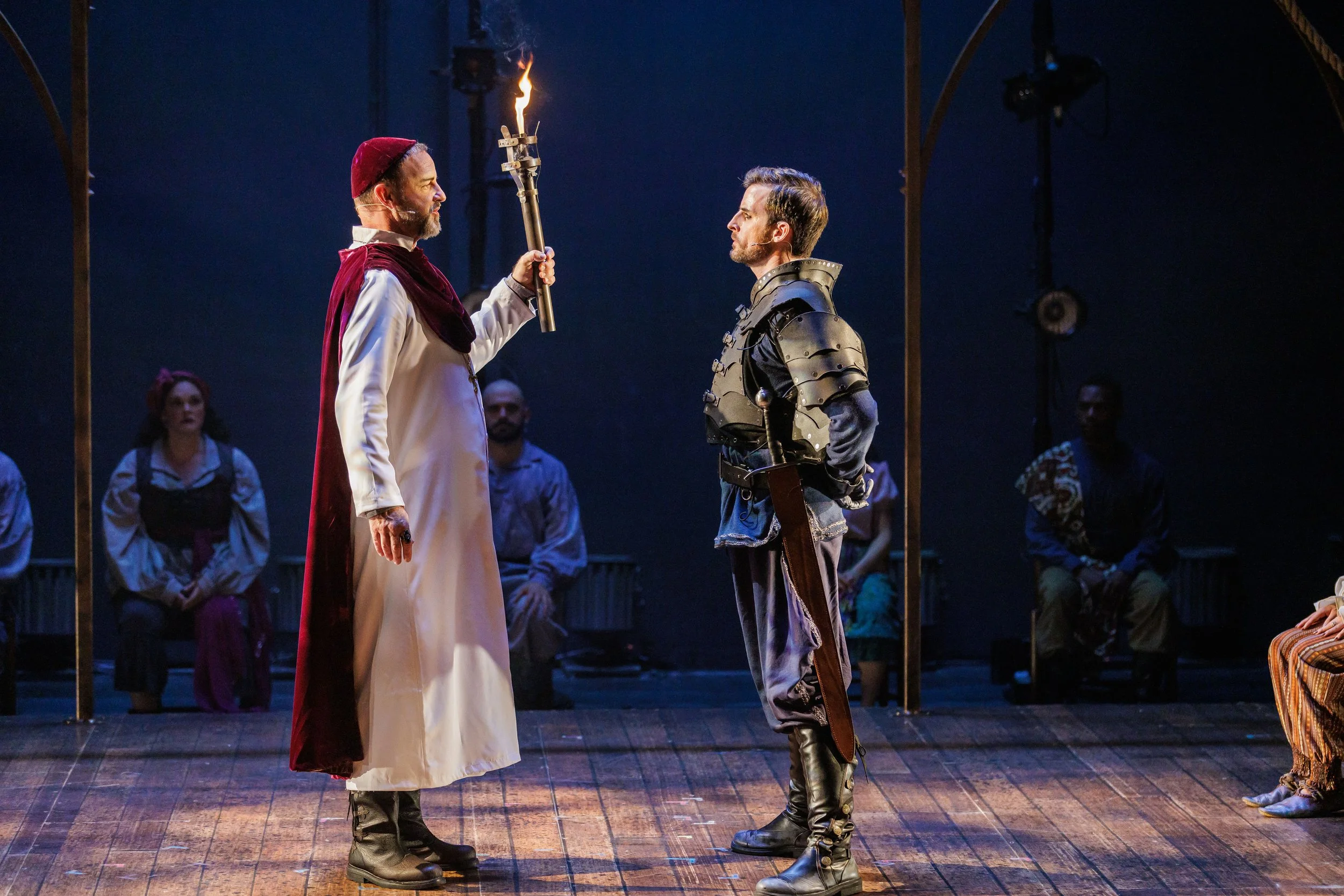
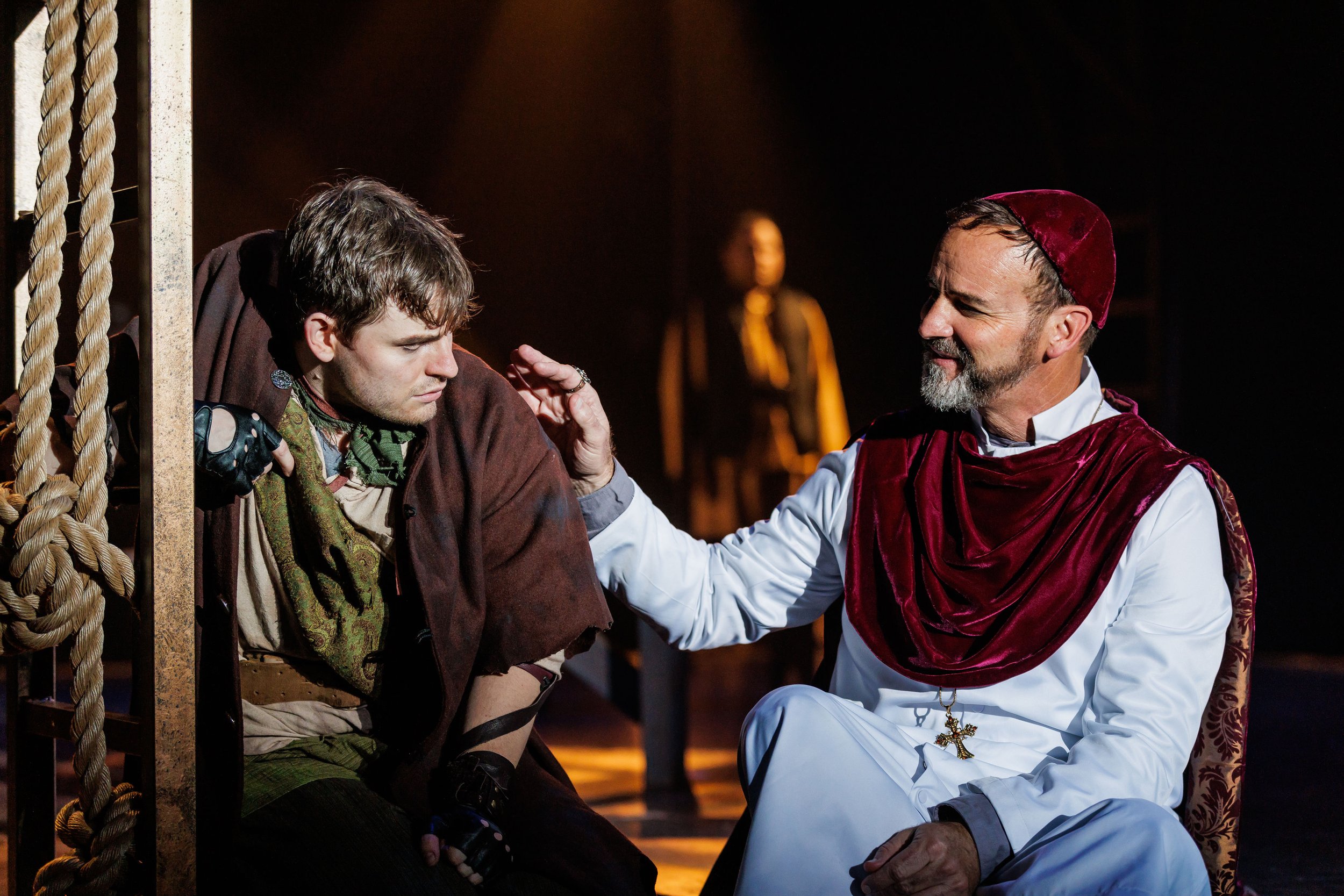
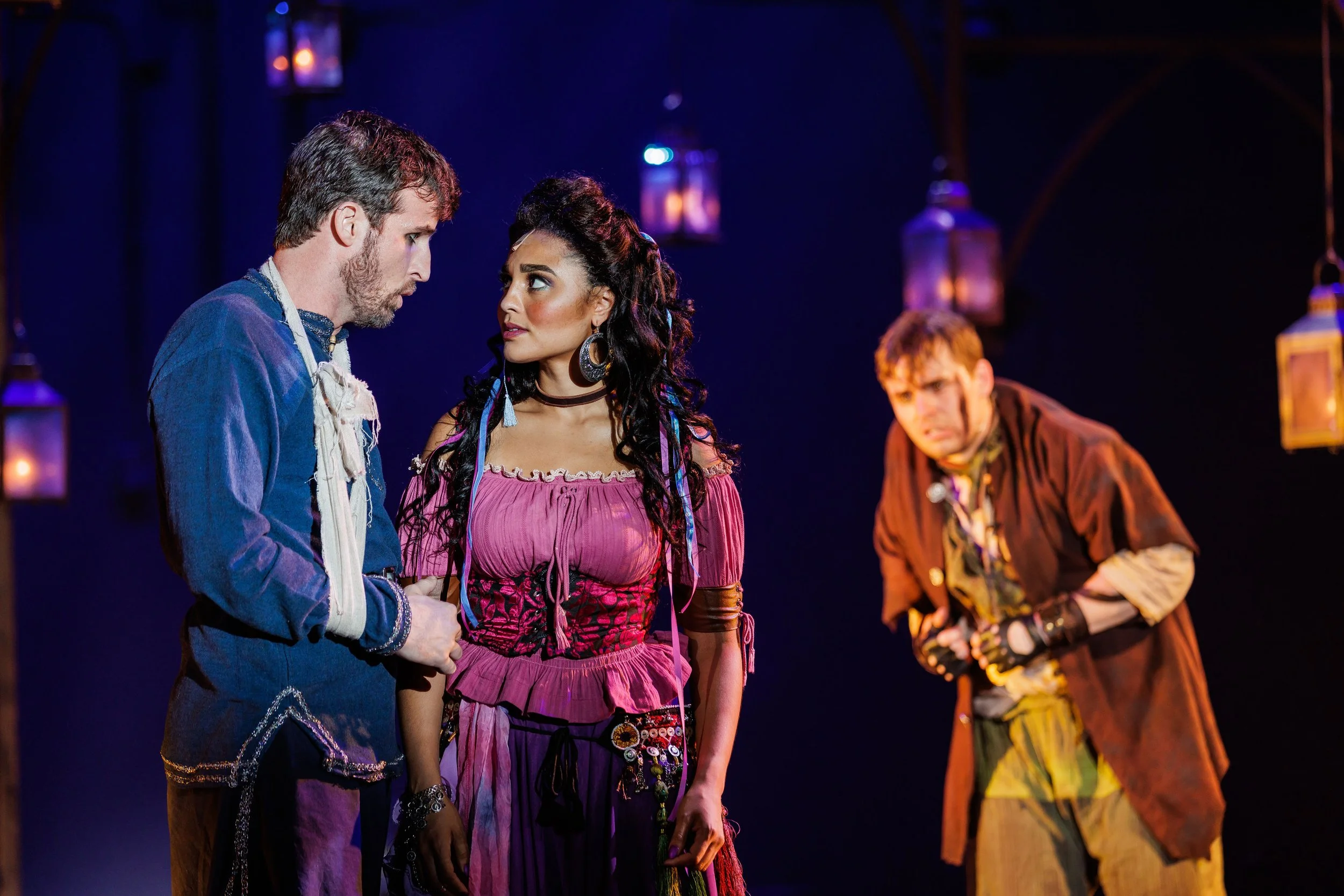
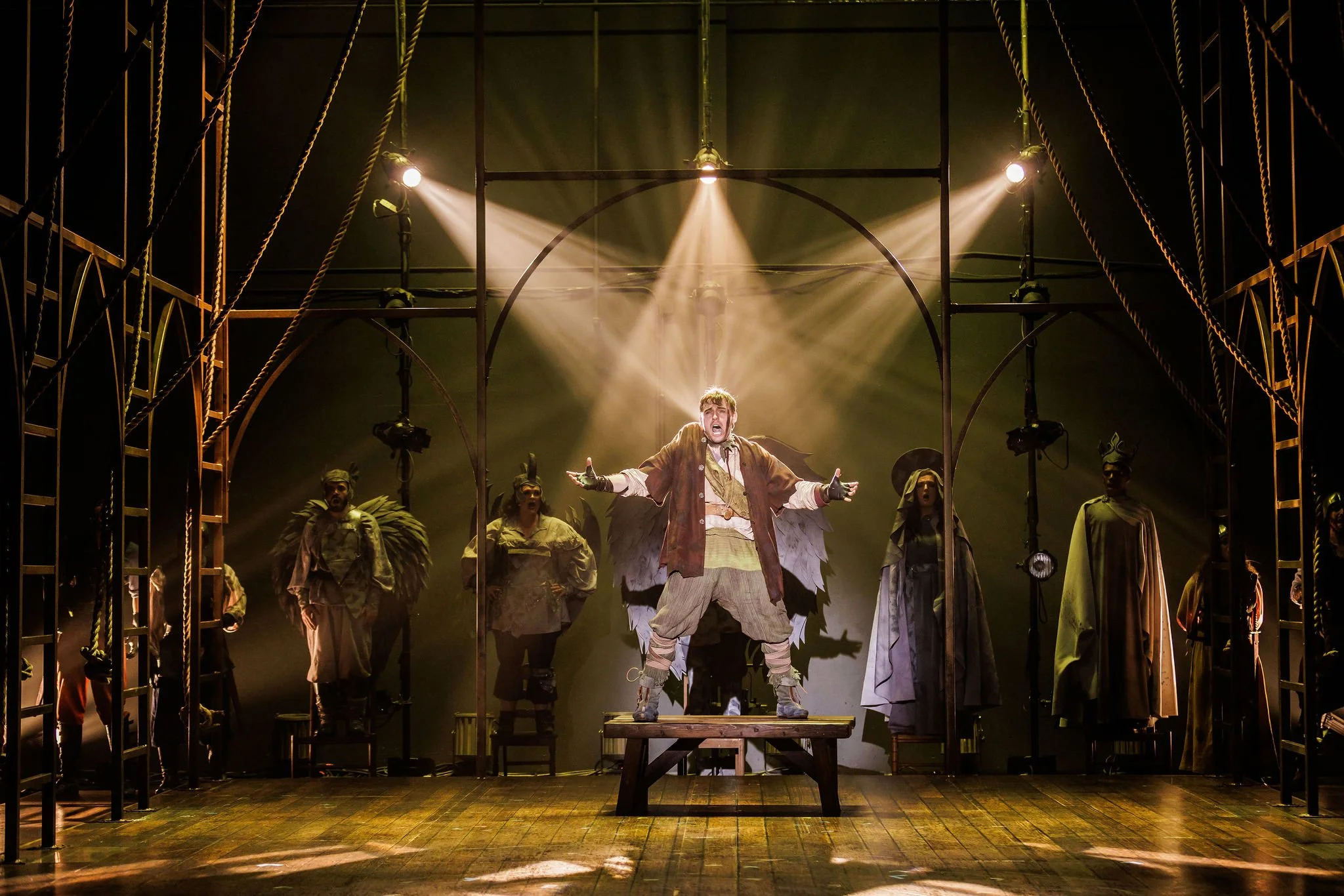
Production Photo credits:
Ron Heerkens Jr. / Goat Factory Media Entertainment
FB: @Goat Factory Media Entertainment
Twitter/Instagram: @gfmedia
Website: goatfactorymedia.com/