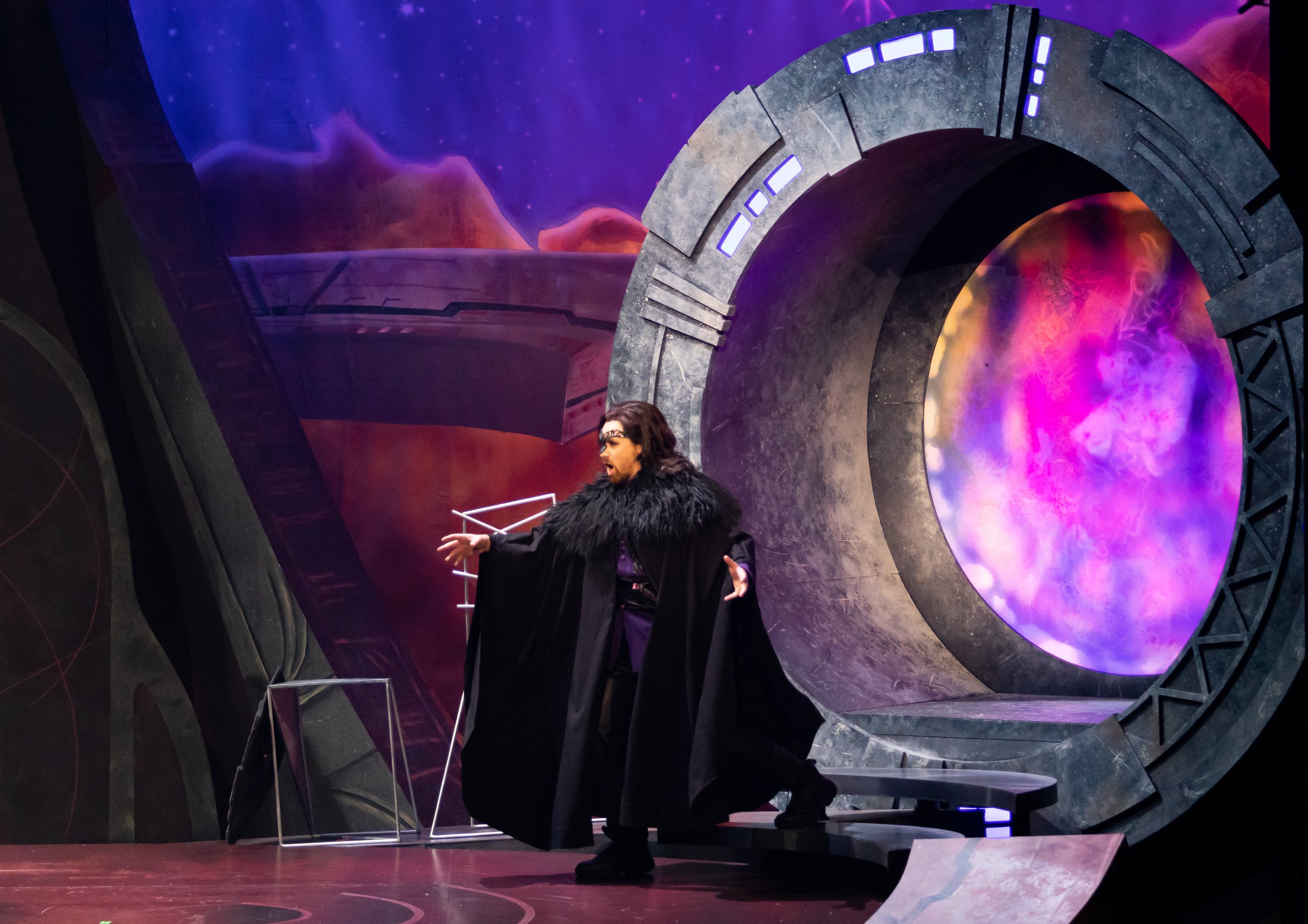
ORLANDO PALADINO
A.J. Fletcher Opera Institute
Directed by Steven LaCosse
Scenic Design:
Gisela Estrada
Lighting Design:
Petko Novosad
Wig & Makeup Design:
Madi Pattillo
Costume Design:
Logan Benson
Spring 2023, Technical Director
Draftsperson:
Chase Dietrich
Lead Carpenter:
Graham Savage
Assistant Technical Director:
Christopher Hackett
Automation Engineers:
Nomi Frank & Van Wei
Orlando Paladino is a three act Italian Opera about love, madness, and magic. This production took place at the Stevens Center in downtown Winston-Salem and would serve as the final opera for the A.J. Fletcher Opera Institute in the historic venue prior to its major renovation. As such, the creative team wanted to commemorate the occasion by going big and bold. The “Space Opera” as it became affectionately known was rooted in high camp, and pulp sci-fi. This production was such a fun challenge, recreating all of the unconventional and semi-organic architectural shapes. I tried to focus on the utilization of the CNC machine to streamline our process on the shop floor and make some of the projects more consumable. It was an honor to be part of this behemoth.
This production had an allotted scenery budget of $18,500. In my first pass of the budget with the original design, we landed around $18,000 over with a 20% contingency. Thus began the negotiation process. I set a base schedule for budgeting; wherein I would present and discuss numbers, within 24 hours I would have changes from the design team, and within 48 I would present the next version and start the process over again. On the sixth round of budgeting, the design had scaled back and become more specific and we landed with $53 to spare. Thus we agreed to move forward into production. This was a whirlwind process of about two weeks, but was a pleasant challenge.
See the original and final versions of the budget at the links below.
The first units I tackled in my technical design was the collection that came to be simply known as “The Main Platform”. These were permanent fixtures that played in every scene.
There were three “Moon Steps” units. These were steel platforms with eclipse shaped lids that allowed navigation diagonally across the raked platform. Two of the Moons had counter-raked legs on the offstage side of the playing space to allow a level entrance up to the “Transporter” unit when it played in acts one and three. To help in both the welding layout process as well as assembly, the outline of the steel frame was etched into the underside of the plywood lid when it cut out on our CNC.
The platform part of “Main Platform: was a large rake that came to be known as the “Disc”. It was an ellipse shaped platform, on raked studwalls, with a lightbox built into the facing. The lightboxes were the biggest challenge of the unit. The actual facing pieces were cut out of bendiply on the CNC. The pieces were made to attach underhung to the bottom of the Disc to help the unit to appear to be floating.
Next was the “Ramp”. This raked arc shaped platform was two layers of 3/4” ply laminated together on raked studwalls that were captured in place by another piece of plywood. This unit is where I started to explore the CNC machine as a method of speeding up the entire construction process and not just in cutting out unique shapes. The carpenters just had to make studwalls and put all the pieces together.
The last piece of this collection was affectionately known as “Chunk”. This fun piece of space debris was double raked and arc shaped. Once i wrapped my head around its shape, I decided to try my hand at a CNC puzzle piece plywood construction method. All the ribs slotted into each other and pinned with some 2x supports, then the whole thing was clad. This went on to inspire a large part of the “Tower” build.
Below are some images from my AutoCAD model, as well as a link to the full draft package for the unit.
The “Cave” pieces were the only flying hard scenery. Keeping with the theme of the production, the pieces were cut on the CNC with the layout for the steel frame etched into the back. To rig these I used forged eye-bolts, and Griplock connectors. The Griplocks allowed us adjustability from the ground. This was essential as these all played above the rake and there was no space to hide turnbuckles on the bottom.
Below are some images from my AutoCAD model, as well as a link to the full draft package for the unit.
The “Transporter” was a moving unit that parked onstage for acts one and three, but had to slide offstage for act two. It was meant to look like a futuristic portal to another dimension, thus be a seemingly floating tube. This unit also was meant mainly as an entrance and exit, and played with the “Main Platform” units. I started with a steel wagon base, and accompanying escape stair. This lead up to the platform landing, also steel. The main body of the unit was two bent steel frames wrapped in bendiply, these landed on semicircle footings and bolted together at the top. The back had a translucency flat that was pinned onto a 1/2” ply face that helped iris in the painted image. The front “wreath” piece was a buildup of various layers of plywood, and featured several cutouts and small lightboxes. The wreath piece split in two for transit and bolted onto the body. This unit is one of my favorite I have ever tech designed.
Below are some images from my AutoCAD model, as well as a link to the full draft package for the unit.
The final and largest unit was the “Tower”. This structure served as the main entrance for the magical enchantress and included an automated drawbridge. This unit had a staircase up to the landing that would lead to the drawbridge. This landing was surrounded on all sides by Hollywood flats to create a hallway. The face of the unit was Broadway style flats with some CNC’ed framing members to help establish their organic shape. Upstage of the unit on either side were two custom masking flats cut in the same silhouette of the rest of the tower to aide in sightlines.
The hallway was flanked on either side and on top by large flats with almost 2’ deep reveals. To accomplish such depth, I once again opted for the CNC puzzle piece method, to get an organic shape quickly. This applied to all of the thick flats except the tops of the side pieces, these were steel frames for added rigidity and support. These top pieces were flown on 1/4 Ton chain motors, landed and through-bolted to the rest of the structure. This unit was huge and i had a blast dissecting it into all its components and bringing it to life.
Below are some images from my AutoCAD model, as well as a link to the full draft package for the unit.
Above is the model made by our designer Gisela Estrada; below is the set during pre-show.
Below is a selection of production photos courtesy of Gisela Estrada.
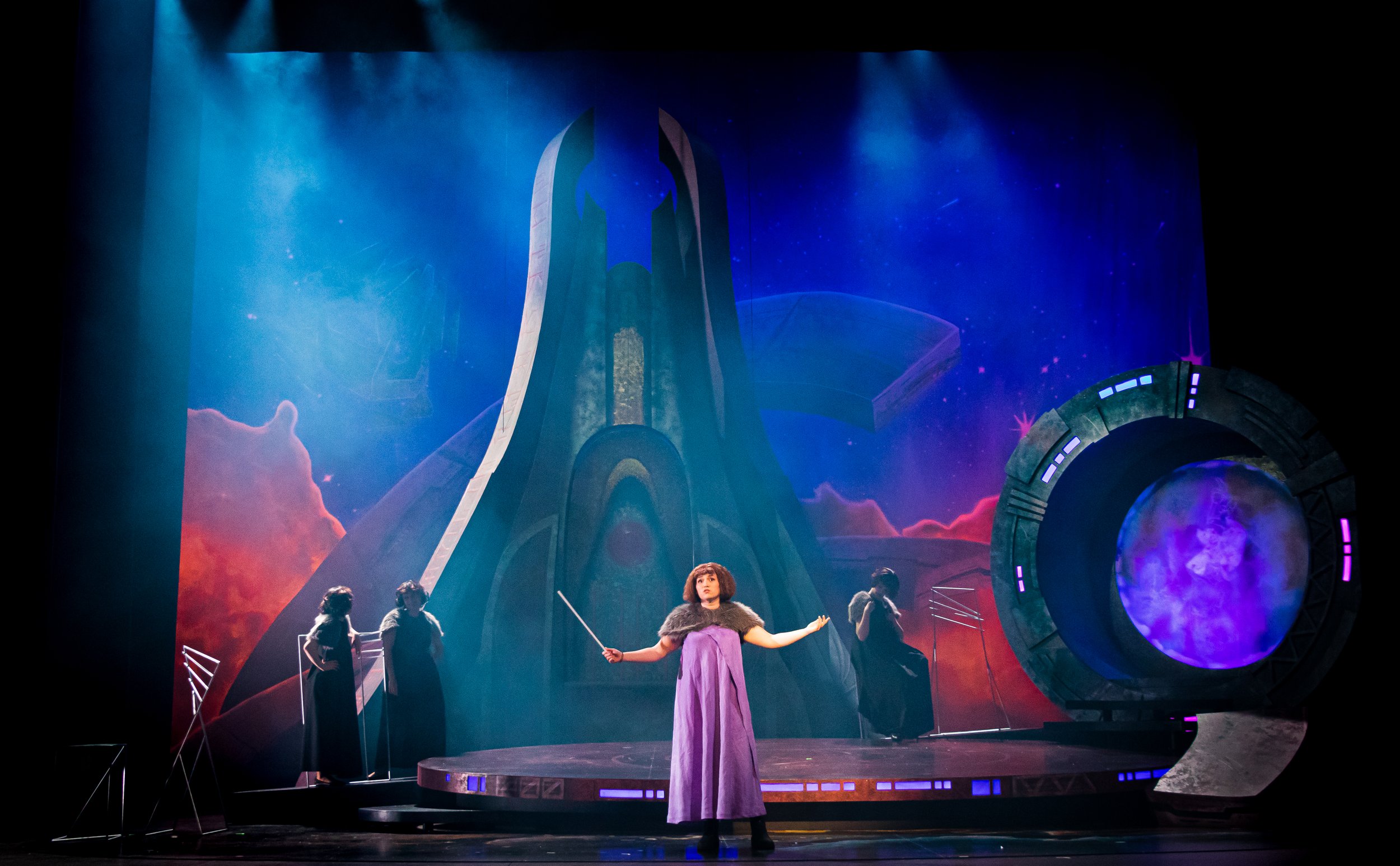


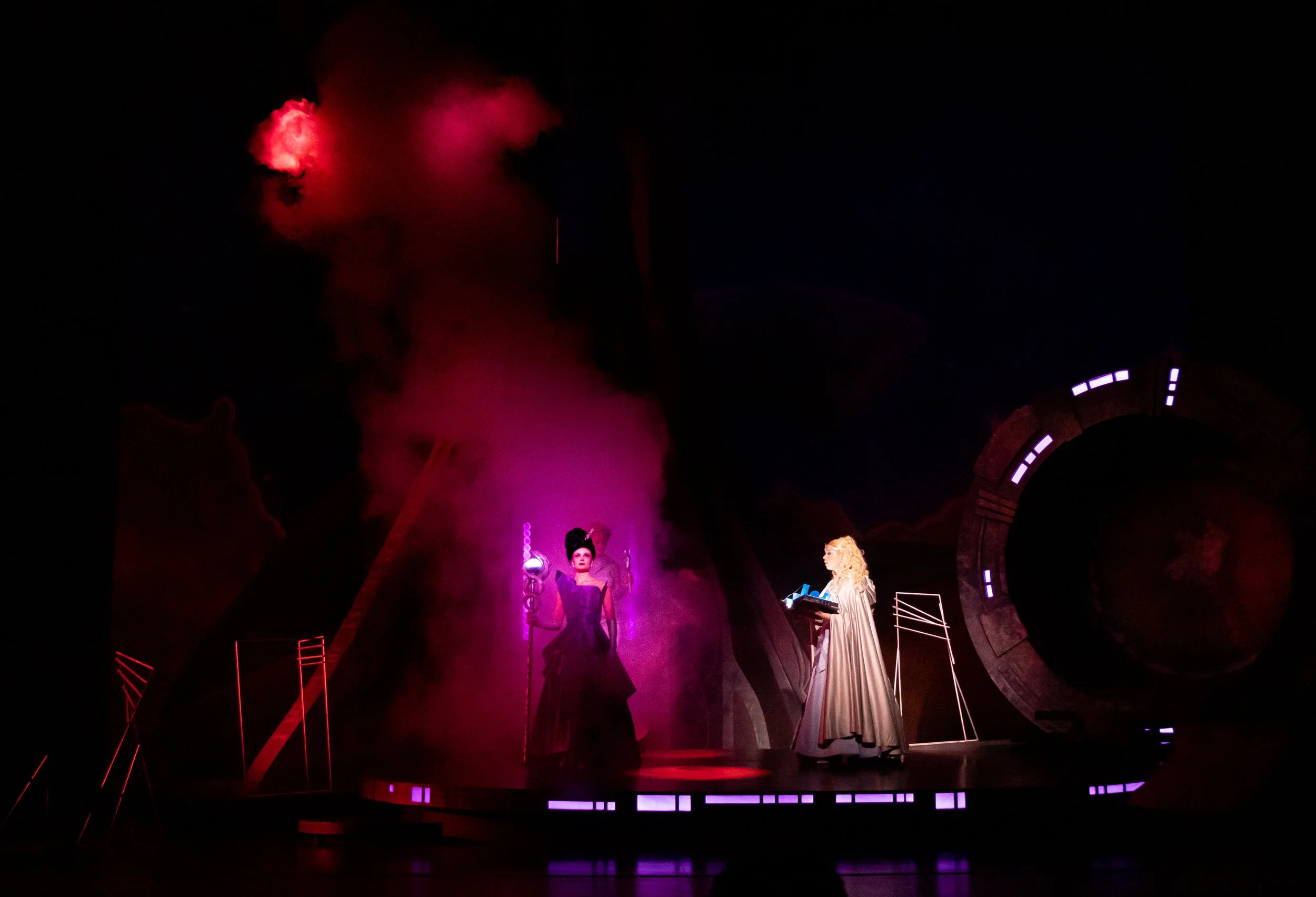
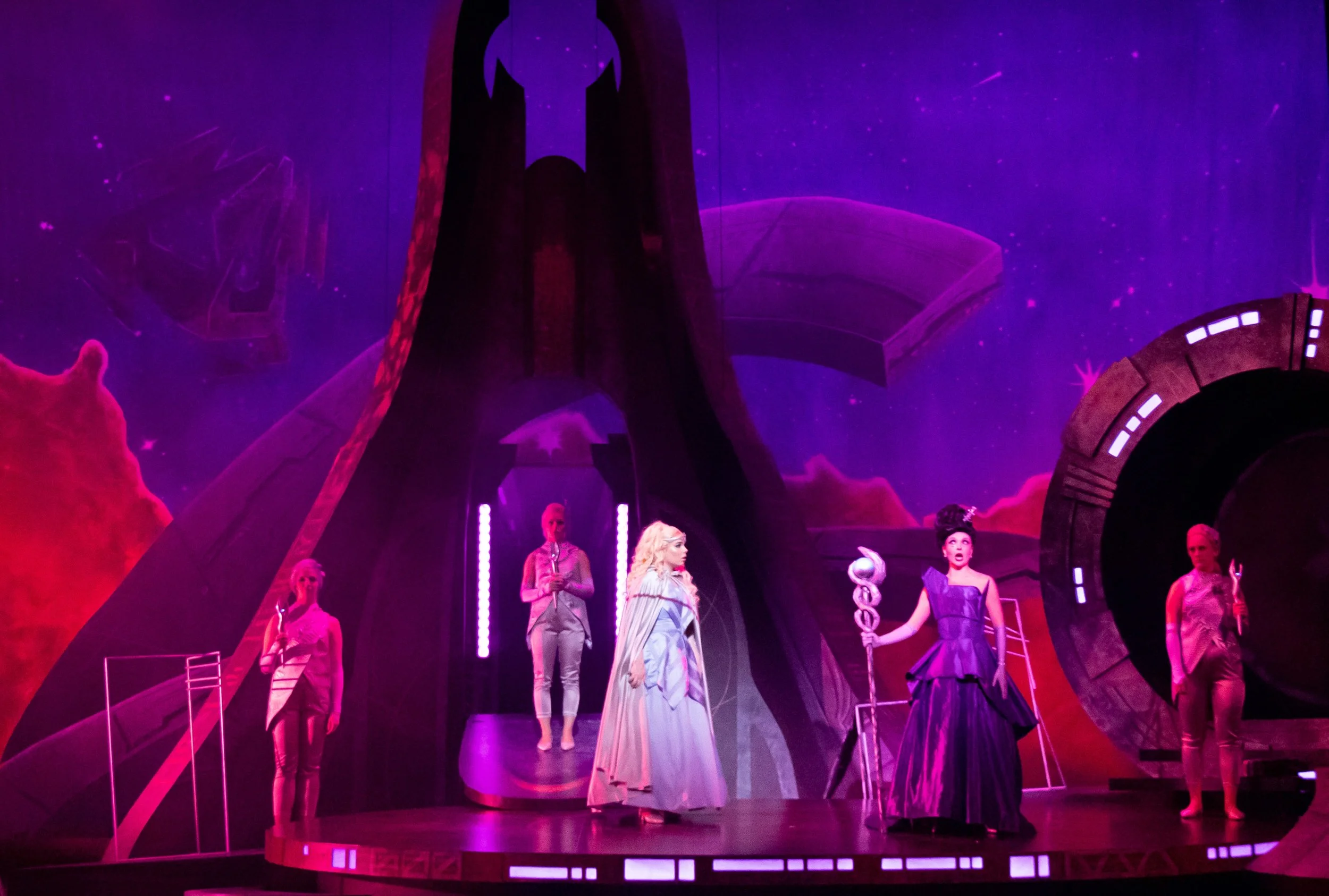
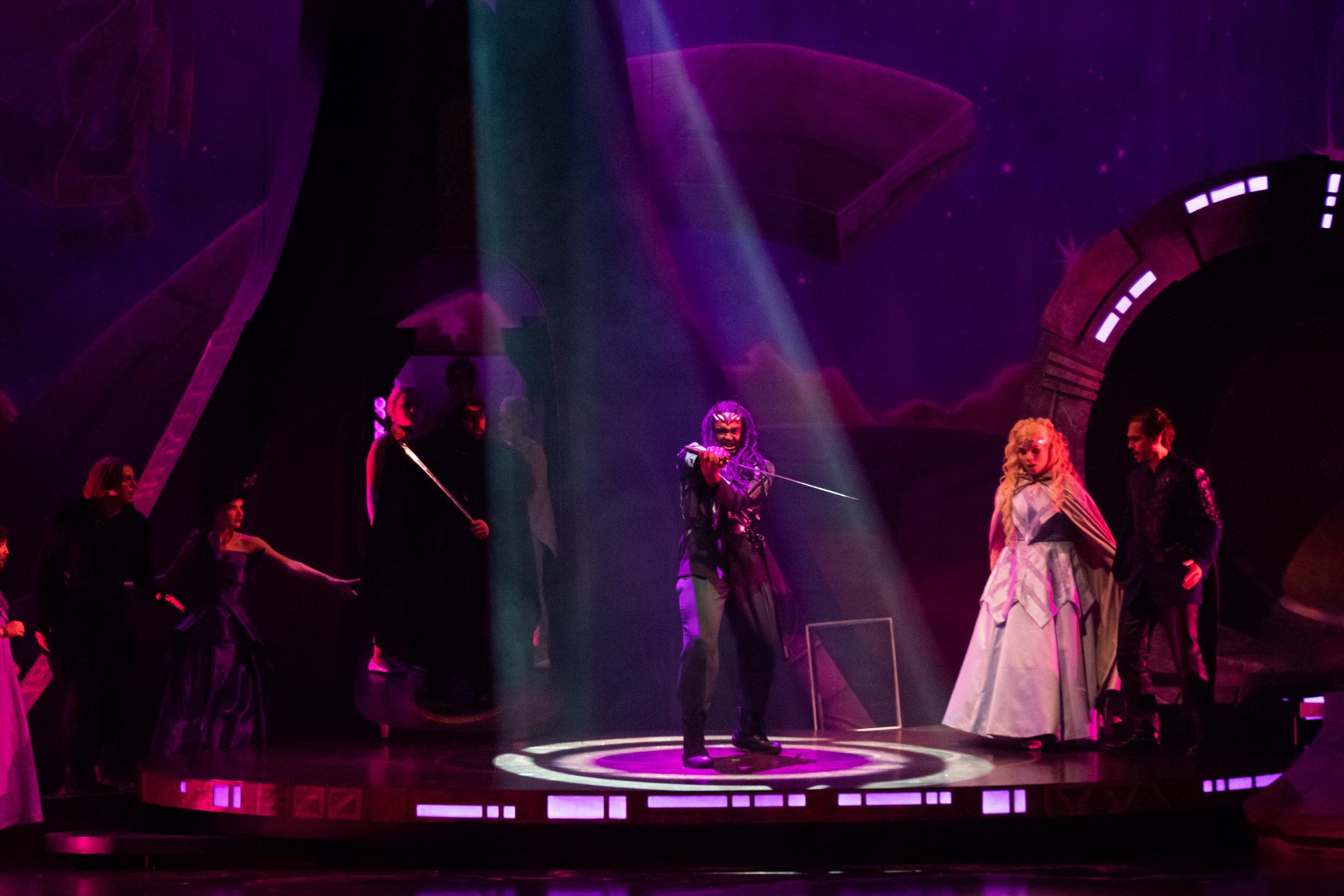
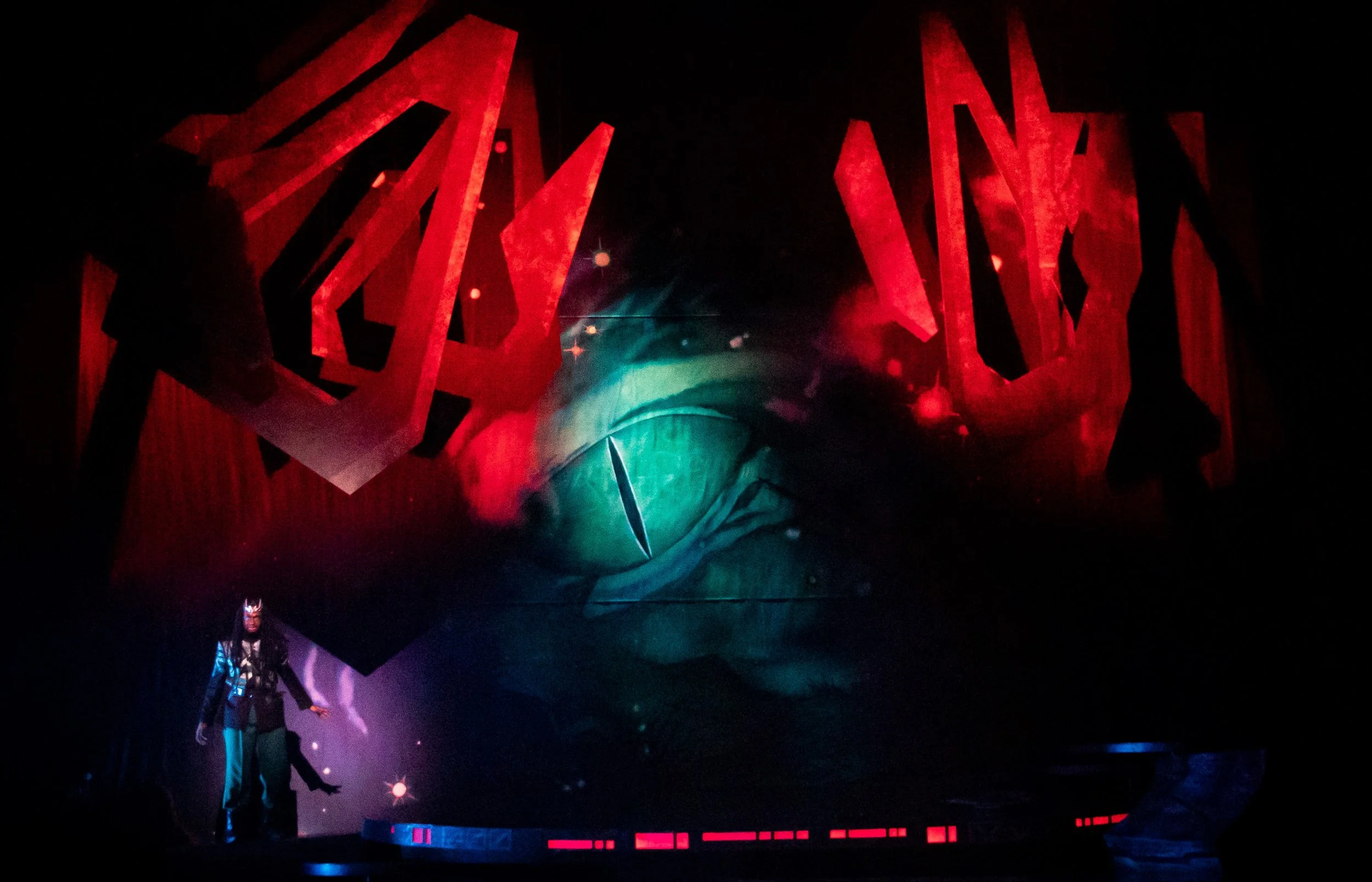

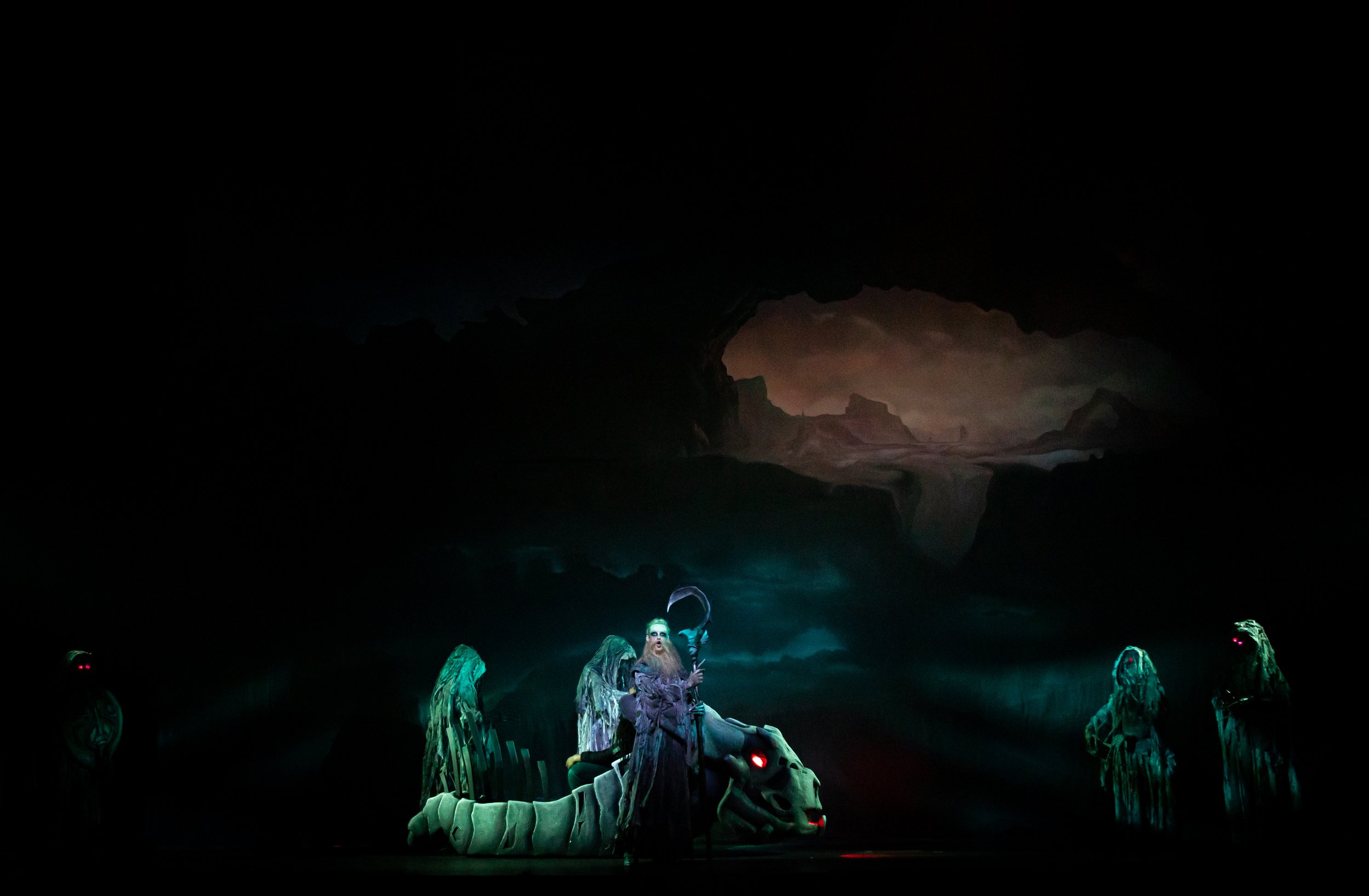
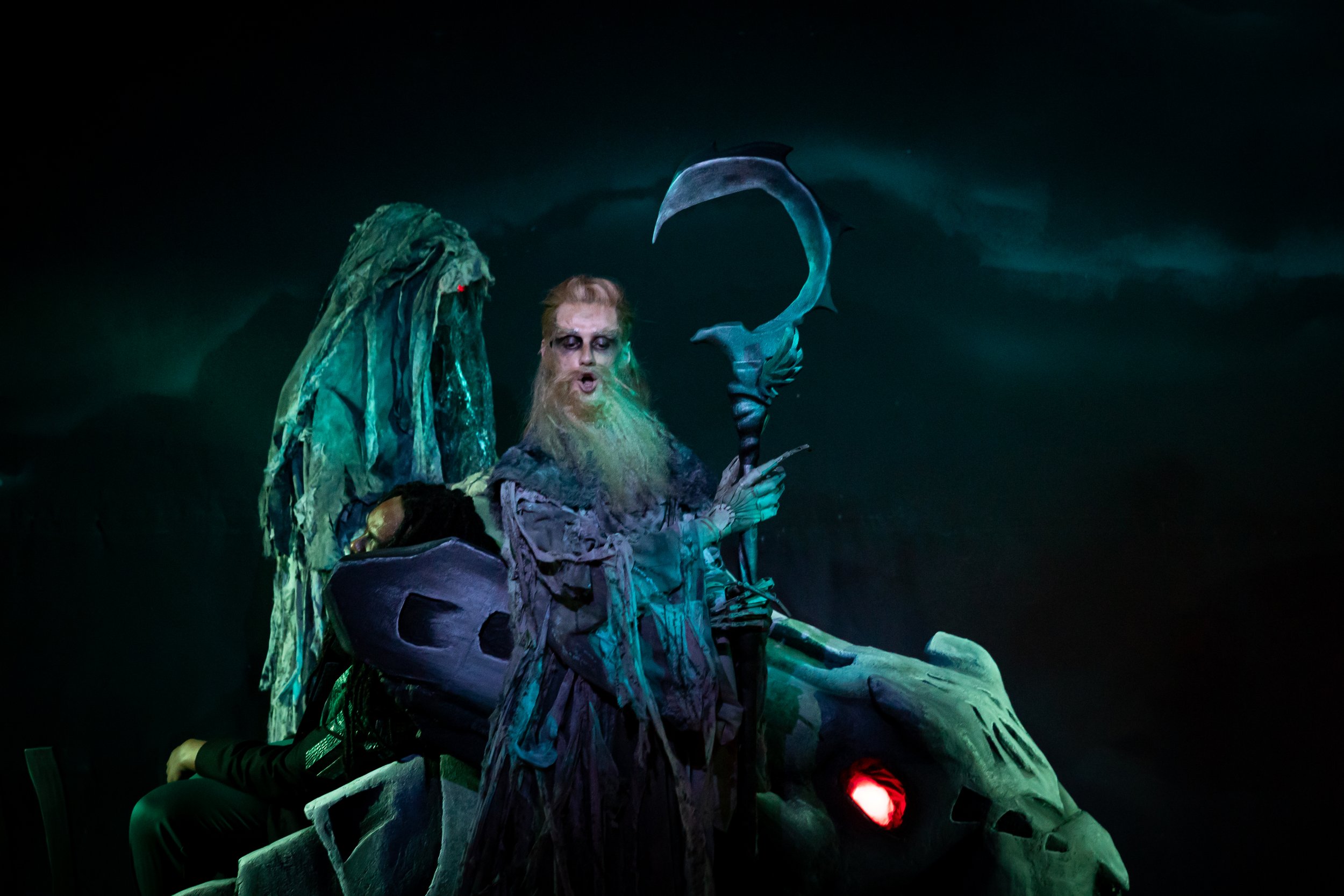


